Produire dans l’Europe à Vingt-Cinq : réalité et idées reçues

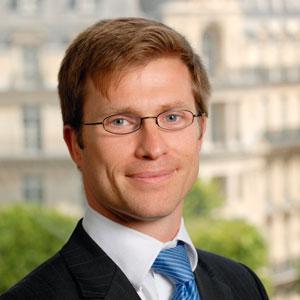
Faut-il installer des unités de production dans des pays à bas coûts ? Le risque est-il maîtrisable ? L’avantage de coût est-il pérenne ou s’agit-il d’un effet de mode ?
Ces questions, de nombreuses entreprises se les posent au moment de redéfinir leur stratégie industrielle et de décider ou non de franchir le cap. En particulier, compte tenu de barrières logistiques et culturelles relativement faibles, l’ouverture des pays d’Europe de l’Est a rendu cette question brûlante pour de nombreuses activités manufacturières.
Notre expérience d’accompagnement de nos clients nous a amenés à un constat clair : malgré (à cause de ?) la masse d’informations disponibles sur le sujet, de nombreuses « idées reçues » subsistent sur ces questions. Encore aujourd’hui, ces a priori transforment la réflexion économique en débats de convictions, paralysent les processus de décision, et, in fine, peuvent conduire les entreprises à rendre les mauvais arbitrages. Pourtant, la plupart de ces idées reçues ne résistent pas longtemps à l’épreuve des faits et méritent qu’on leur « torde le cou » une fois pour toutes.
Idée reçue n° 1 : « L’avantage de coût de main-d’œuvre n’est pas pérenne »
« Vous allez voir, l’inflation et les augmentations de salaire vont vite réduire le différentiel de coût à la portion congrue » : argument massue, le plus fréquent, remettant en cause la pérennité de tout projet d’implantation dans un pays à bas coûts.
Certes, des augmentations de coûts salariaux de 10 % à 15 % par an ne sont pas rares. Toutefois, le différentiel de salaire en valeur absolue ne se résorbe pas aussi vite que l’on pourrait le penser (cf. figure 1) : une augmentation de 10 % du salaire d’un opérateur slovaque, soit 4 000 € annuels, engendre un surcoût de 400 €. Pendant ce temps, une augmentation « classique » de 2 % du coût du travail d’un opérateur français (soit 30 000 €) engendre un surcoût de l’ordre de 600 €.
À cet égard, un regard historique sur l’Espagne et le Portugal est riche d’enseignements (cf. figure 2) : le coût du travail ouvrier dans ces pays représentait au milieu des années soixante-dix respectivement 60 % et 35 % du coût constaté en France. En 2002, soit plus de quinze ans plus tard, ces ratios étaient encore de 70 % et 30 %. L’écart est donc resté relativement stable malgré l’adhésion à la Communauté européenne en 1986.
Enfin, si l’on peut sans doute s’attendre à une lente convergence des niveaux de vie et des salaires, celle-ci se fera sur une échelle de temps sans rapport avec celle d’un investissement industriel. On investit aujourd’hui dans une usine avec une perspective de dix à vingt ans et le retour sur investissement d’un tel projet est généralement inférieur à cinq ans.
En pratique, si des déceptions existent dans le domaine des coûts, elles relèvent davantage de business plans mal préparés et exagérément optimistes que d’une réalité macroéconomique.
Idée reçue n° 2 : « Les coûts et la complexité logistique rendent le projet irréaliste »
L’argument logistique apparaît aussi fréquemment dans le débat : « Vous verrez lorsque vos produits seront bloqués par la neige en Pologne »…
Certes, la qualité des infrastructures logistiques est un élément déterminant du projet : le réseau autoroutier en République tchèque ou dans l’ouest de la Slovaquie est d’excellente qualité, contrairement à l’est de la Slovaquie ou à la Pologne. Cependant, même dans des contrées apparemment reculées, des industriels parviennent à maîtriser leurs flux logistiques : l’usine de composants Bosch Siemens de Michalovche (est de la Slovaquie) livre quotidiennement une vingtaine de camions et fournit l’Allemagne, l’Italie, l’Angleterre, les États-Unis…
Là encore, il suffit de se pencher sur une carte pour constater que la frontière est de la Slovaquie n’est géographiquement pas plus éloignée de Paris que le sud de l’Espagne ou de l’Italie.
Certes, les formalités aux frontières ont été pénalisantes en termes de temps de transport routier jusqu’à récemment ; l’élargissement récent de la Communauté européenne devrait toutefois remédier à cette difficulté.
En pratique, on s’aperçoit que les problèmes rencontrés par certaines entreprises relèvent davantage d’une mauvaise maîtrise de la Supply Chain ou d’un manque de relais locaux que de réels problèmes structurels.
Idée reçue n° 3 : « La productivité de la main-d’œuvre locale est inférieure à celle des pays d’Europe de l’Ouest »
Par exemple, on entend fréquemment que la productivité en Europe de l’Est serait inférieure à celle d’Europe de l’Ouest. Pourtant, si l’on réfléchit de manière pragmatique, quelle différence structurelle pourrait bien faire qu’un opérateur d’assemblage slovaque, tchèque ou hongrois produirait moins de pièces par jour qu’un opérateur réalisant les mêmes tâches en France, en Allemagne ou aux États-Unis ?
En réalité, cette vision biaisée de la réalité nous vient en grande partie des… économistes. En effet, les mesures de productivité pratiquées par les organismes officiels se basent sur des mesures de PIB par heure travaillée (cf. figure 3).
Ces mesures, pour la question qui nous intéresse, présentent plusieurs effets pervers :
• mesurées en dollars ou en euros, elles ne rendent pas purement compte d’une production en volumes ;
• calculées par pays, elles sont influencées par la nature même de l’économie du pays : une économie à dominante agricole générera un PIB par heure travaillée inférieur à une économie de services ;
• surtout, elles ne rendent pas compte de l’arbitrage capital-travail : dans un pays à faible coût de main-d’œuvre, les investissements dits « de productivité » se justifient moins. Pour un volume de production donné, on aura donc plus de main-d’œuvre dans un pays à bas coûts mais beaucoup moins de capital.
On constate ainsi que les données macroéconomiques doivent être maniées et interprétées avec discernement.
Enfin, certains argueront que, par exemple, trente ans de communisme ont laissé des traces en Europe de l’Est en termes de goût de l’effort et d’ardeur au travail… C’est sans doute vrai (quoique de moins en moins) en moyenne. Mais là encore, les entreprises implantées sur place qui prennent la peine de sélectionner et de former leurs collaborateurs parviennent à surmonter ce problème.
Au contraire, le fait de démarrer une unité de production « From scratch » dans un pays à bas coûts permet de mettre directement en œuvre un certain nombre de bonnes pratiques. Ces mêmes pratiques, pour être implantées en France ou en Allemagne, nécessiteront de longues négociations et de redoutables efforts en termes de gestion du changement. Ainsi, deux équipementiers automobiles nous ont déclaré que leurs usines européennes les plus performantes en termes de productivité se trouvent pour l’un en Hongrie, pour l’autre en Pologne…
Idée reçue n° 4 : « Il faut utiliser les usines dans les pays à bas coûts pour les produits en fin de vie »
Aujourd’hui encore, certains soutiennent que lancer directement de nouvelles lignes de produits dans des usines situées dans des pays à bas coûts constitue un risque inacceptable. La maîtrise des procédés et des process n’y serait pas aussi bonne que dans les usines « historiques » du groupe, les ingénieurs n’y seraient pas assez performants, la qualité serait insuffisamment présente dans les mentalités. Ainsi, au sein du dispositif industriel, les usines des pays à bas coûts ne seraient destinées à recevoir que les produits en fin de vie, fabriqués sur des équipements plus ou moins obsolètes.
Cette approche, là encore, trouve très vite ses limites : de nombreuses entreprises réussissent à trouver des ingénieurs d’excellente qualité dans des pays à bas coûts. Au contraire, souvent confrontées à un chômage endémique, les autorités locales font preuve d’une adaptation exemplaire en termes de formation. Plusieurs des entreprises que nous avons pu rencontrer en Pologne, en République tchèque ou en Slovaquie ont établi des partenariats avec les universités locales de manière à disposer des formations et des talents adaptés à leurs besoins spécifiques.
S’il faut, bien entendu, du temps pour transférer le savoir-faire nécessaire à la maîtrise du lancement de nouveaux produits, il s’agit de gérer convenablement une transition et non d’un handicap structurel.
Enfin, un certain nombre d’entreprises, notamment des équipementiers automobiles, ayant tenté une telle approche par le passé l’ont vite abandonnée pour deux raisons :
• le principe de transférer des lignes de production en fonction du cycle de vie du produit génère des surcoûts importants ;
• il est difficile de motiver le personnel d’une usine dans de telles conditions.
Si l’on trouve encore aujourd’hui quelques usines fonctionnant suivant cette « philosophie », celles que nous avons visitées sont loin de constituer des « Best practices » et tendent fort heureusement à devenir l’exception.
On vient de le voir, la plupart des idées reçues en termes d’implantation dans des pays à bas coûts ne résistent ni à l’analyse ni à l’épreuve des faits. Certes, il ne faudrait pas pour autant en déduire que tout projet d’implantation est économiquement justifié et que la mise en œuvre ne comporte pas de risque. Des échecs existent encore aujourd’hui. Ils sont liés parfois à des choix stratégiques erronés (pari sur des marchés locaux surestimés, projections économiques erronées…) et, assez fréquemment, à des erreurs dans la mise en œuvre (manque de préparation, planning irréaliste, sous-estimation des spécificités locales…).
Quoi qu’il en soit, ces échecs ne sauraient servir de prétexte à des conclusions à l’emporte-pièce quant au bien-fondé de la démarche.
En effet, souvent brandies face au spectre de la désindustrialisation, ces idées reçues ne servent généralement qu’à se voiler la face dans un contexte concurrentiel global, mouvant et difficile.
Au contraire, les entreprises qui réussissent sont celles qui, lucides et responsables, évitent les combats d’arrière-garde et essaient d’anticiper et de concilier intelligemment les opportunités offertes par la globalisation avec le maintien de leur implantation historique.
À travers une analyse factuelle et détaillée des lois économiques de l’entreprise, de ses marchés présents et futurs, de ses réalités et contraintes opérationnelles ces entreprises parviennent à repenser leur organisation, leurs process et leurs marchés dans une perspective globale.
Loin de tout a priori… et de toute idée reçue !