Le nickel innove
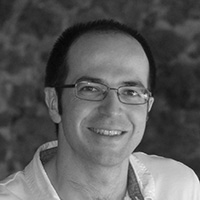
Dans une science qui existe depuis l’Antiquité, dans une industrie qui travaille selon un procédé établi dans les années 1970, les innovations sont plutôt rares. C’est pourtant le défi relevé par la société Le Nickel (SLN).
Il serait présomptueux de résumer ici les 139 ans d’existence de la SLN. Sur son caillou, au milieu de l’océan Pacifique, elle a vu défiler le XXe siècle. Des premiers colons à la crise des subprimes, en passant par le million d’Américains débarqués dans les années 1940, la SLN a vu la grande histoire affecter la sienne, et les longs cycles du cours de l’ « or vert » lui donner des années d’abondance et d’autres de disette.
Nickel : pourquoi et comment innover ?
Le nickel est aujourd’hui en bas de cycle depuis plusieurs années, peut-être même de façon structurelle du fait du développement de capacités de production dans des pays très compétitifs. Des frémissements de jours meilleurs se font sentir, au bon vouloir du développement des batteries pour automobile. La situation est difficile pour l’ensemble des acteurs du nickel. L’innovation est essentielle pour rester en tête de peloton : les entreprises de cet âge le savent, elles ne peuvent survivre sans continuellement se réinventer et challenger leurs certitudes. C’est le défi actuel de la SLN.
Mais comment améliorer un procédé, inventé ici même il y a plus de cinquante ans ? Depuis la découverte et la mise en service du procédé de fabrication de ferronickel RKEF (Rotary Kiln Electric Furnace), des générations d’ingénieurs se sont succédé pour comprendre l’influence de chaque levier, déterminer l’intérêt de chaque point de fonctionnement, tester la véracité de telle ou telle hypothèse. Avec le temps, de très nombreux sujets ont été méthodiquement étudiés puis consignés sur papier, machine à écrire et plus récemment ordinateur. Nos prédécesseurs ont posé et résolu avec les quelques approximations inévitables de très nombreuses équations pour déterminer ce qui se passe dans un four de fusion : électricité, dynamique des fluides, échange thermique pour le côté physique, cinétique et thermodynamique dans un milieu multiphasique pour le côté chimie.
REPÈRES
Si nous fêtons cette année les 150 ans de la publication de la classification périodique des éléments de Mendeleïev, la SLN, fière de ses 139 années d’existence, supporte plutôt bien la comparaison. On pourrait presque lui rajouter les quelques années de différence, puisque, si la société a bel et bien été créée en 1880 à Nouméa, le premier brevet d’exploitation du nickel calédonien a été déposé en 1876 par Jules Garnier, dix ans après la découverte par ce même Jules Garnier du minerai de nickel qui porte maintenant son nom : la garniérite.
Détour par la théorie
Le côté théorique est peut-être le plus abordable si on le compare à ce que l’expérience requiert comme préparation, comme précaution. Il faut dire que l’environnement du four de fusion n’est pas l’endroit au monde le plus accueillant : le métal en fusion, le monoxyde de carbone en quantité importante et la puissance électrique gigantesque transforment chaque nouveau prélèvement, chaque nouvelle mesure en un petit exploit.
Et finalement, cette grande victoire d’avoir réussi à collecter la donnée manquante pour confirmer tel ou tel modèle développé par nos anciens se transforme souvent en grande désillusion. Car, après avoir déchiffré les équations manuscrites d’un double carbone, avoir réalisé la mise en place d’un nouveau point de mesure, le travail du chercheur va pouvoir commencer… et, comme annoncé, les difficultés continuent d’apparaître.
Le diagramme d’Ellingham, le livre de chevet de l’ingénieur en pyrométallurgie, qui permet de déterminer l’ordre des réactions chimiques de conversion des oxydes métalliques en métaux, n’est pas vraiment respecté : pas suffisamment en tout cas pour permettre d’anticiper avec suffisamment de précision la qualité du métal produit pour nos clients. L’équilibre de Boudouard, qui détermine l’avancement de la combustion du monoxyde de carbone en dioxyde et par extension la quantité d’énergie nécessaire pour produire du métal, n’est localement pas respecté non plus. La grande majorité des données reflète la prépondérance des phénomènes cinétiques. Malgré un temps de séjour de plusieurs jours passés dans le four de fusion, la cinétique reste vainqueur de son combat contre la thermodynamique.
Elle finira par perdre, bien sûr, et les différences locales de température, de composition s’atténueront, mais cela se produira hors du four, lorsque le métal sera en cours d’élaboration pour être transformé en produit commercial. En attendant, la principale transformation du minerai oxydé en métal se fait hors équilibre.
“La cinétique l’emporte sur la thermo-dynamique”
Pourquoi fonctionner hors équilibre ?
Par obligation tout d’abord. Il est évident que, thermiquement, il est impossible d’avoir un four de 350 m² de surface au sol à la même température en tout point. Avec un apport conséquent d’énergie en son centre, jusqu’à 60 MW par four, il est nécessaire de refroidir au mieux les parois pour assurer leur pérennité. Un gradient thermique entre le cœur du four à plus de 1 500 °C et l’extérieur de la paroi à moins de 100 °C est irrémédiablement imposé par le procédé. Mais une raison économique pousse aussi à travailler hors équilibre. Avec le minerai actuel, qui est d’ailleurs en constante évolution, il est intéressant de se situer à une certaine distance de l’équilibre chimique des bains. Et toute la difficulté de notre industrie réside là : piloter avec la plus grande précision et la plus grande stabilité un procédé hors équilibre avec, pour principal appui, l’expérience.
Le XXIe siècle tend à mettre fin ou, tout du moins, à fortement réduire le recours à l’expérience humaine pour l’analyse de données. La data science vise typiquement à faciliter la prise de décision pour ce genre de problématique. Un optimum existe, hélas mouvant du fait d’aléas que l’on peut anticiper (variation de composition chimique du minerai, maintenance programmée d’équipement) ou non (panne, hétérogénéité locale). La SLN, soutenue par sa maison mère Eramet, s’est ainsi lancée dans cette démarche et voit aujourd’hui émerger ses premiers modèles de prédiction par data science.
Le challenge semble accessible pour ces modèles empiriques. Les actions sur les réglages mettent plusieurs jours pour être visibles sur les observables de sortie : l’évolution pendant ces quelques jours est donc déjà écrite dans les grandes lignes. C’est cette trajectoire qu’on anticipe. Les algorithmes s’affinent en permanence et fournissent un faisceau de trajectoires de plus en plus précis. Leur seule limite ? Ils sont incapables de prédire les situations nouvelles. Ainsi, métallurgiste et data scientist forment un binôme complémentaire pour les innovations de demain.
Retrouvez les autres articles de notre dossier sur la chimie