Deux polytechniciens startuppers dans la 3D
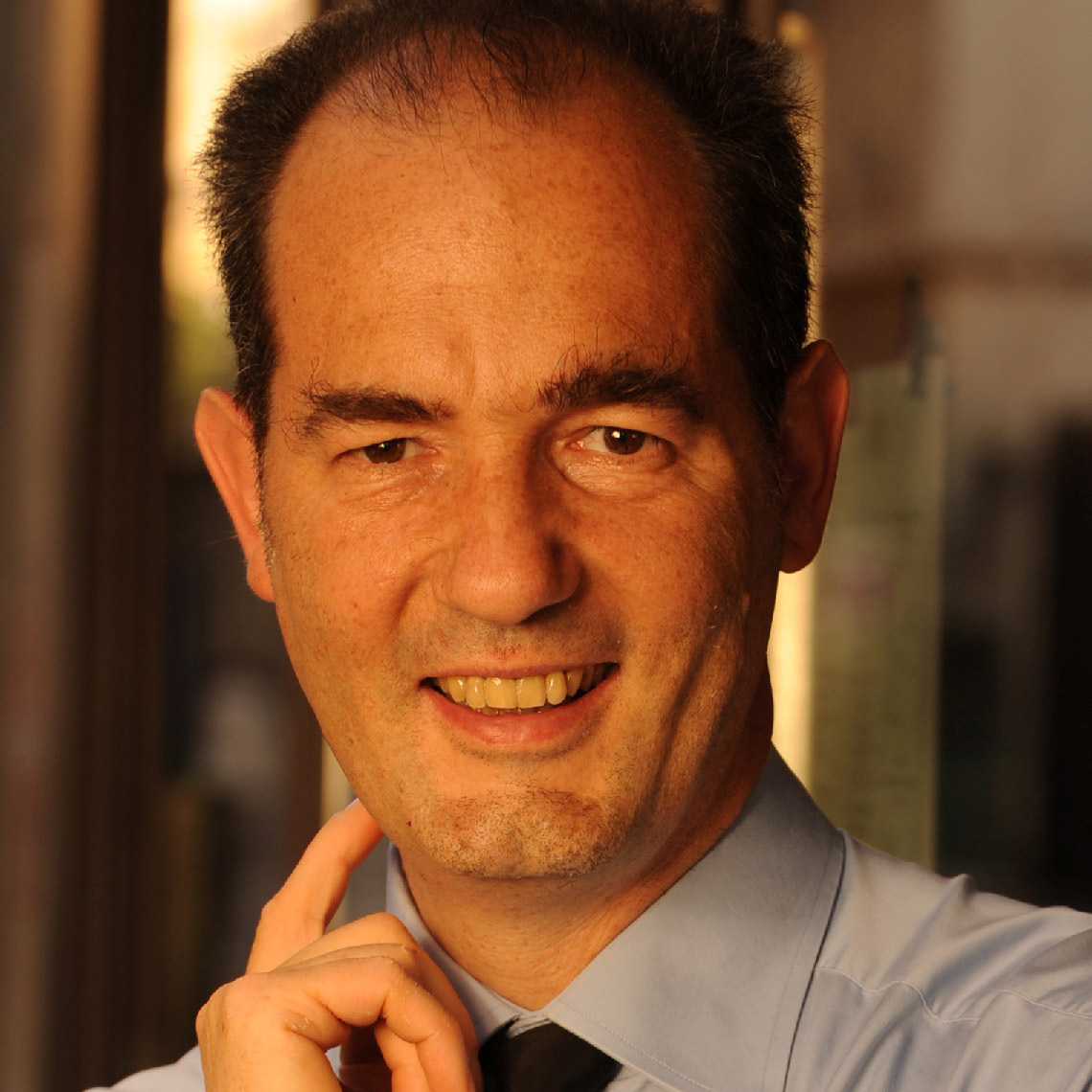


À la manière de la rubrique « 10 questions à un X entrepreneur », tenue avec maestria par le camarade Hervé Kabla (84), le coordonnateur du dossier de ce mois se livre à la présentation de deux start-up dirigées par des camarades : Multistation et Spartacus3D. Comment voient-ils l’avenir de la 3D ?
Quelle est l’activité de Spartacus3D ?
C. de F. : Spartacus3D accompagne les industriels dans le développement, l’industrialisation et la production de systèmes mécaniques par fabrication additive. Concrètement nous intervenons en assistance à la conception afin que les composants soient développés de manière optimale, puis nous pilotons toutes les étapes jusqu’à la production en série qui est réalisée dans notre usine de Mâcon où nous détenons quatre machines de fusion laser. Nous avons des clients dans de nombreux domaines d’activité, en priorité l’aéronautique et le spatial, mais aussi l’énergie, le luxe, l’automobile.
Comment t’est venue l’idée ?
Dans mon parcours industriel, j’ai toujours souhaité rester à la pointe de l’innovation, je suivais donc de près les développements de l’impression 3D alors que j’étais dans l’industrie du packaging. Dans les années 2000 ces technologies étaient principalement réservées au prototypage, à la maquette. L’idée était d’accompagner le passage de ces technologies à la production et, lorsque Frédéric Guinot (président de Farinia) a évoqué ses réflexions sur l’impression 3D métallique, nous avons rapidement trouvé un terrain d’entente.
Quel est le parcours des fondateurs ?
Frédéric Guinot est un entrepreneur avec une forte expérience dans le domaine de la métallurgie et particulièrement de l’automobile. Il a créé Farinia en reprenant des activités diverses dans la fonderie, la forge et l’usinage. Son groupe réalise actuellement 300 M€ de chiffre d’affaires. Pour ma part j’ai évolué dans différents contextes industriels, grand groupe d’abord avec Saint-Gobain, puis ETI familiale avec le groupe Pochet dont j’ai dirigé l’activité flaconnage en verre (200 M€ de chiffre d’affaires), enfin start-up industrielle avec Spartacus3D. Frédéric Guinot m’a donné le goût d’entreprendre et d’une certaine forme de liberté.
Qui sont les concurrents ?
Les concurrents sont de plusieurs types. D’abord des PME ayant démarré dans l’impression 3D plastique et le prototypage, puis ayant évolué vers le métal. Ces PME ont généralement débuté à la fin des années 90, certaines ont été rachetées par des entreprises de mécanique. Ensuite des entreprises de mécanique ayant démarré une activité de fabrication additive métallique, spontanément ou à la demande de leurs clients. Ce sont souvent des PME du secteur aéronautique. Ou encore quelques pure players avec la même approche entrepreneuriale. Et enfin nos clients sont aussi nos concurrents, car il peut y avoir dans certains cas une logique d’intégration.
Quelles ont été les étapes clefs depuis la création ?
La toute première phase a été la décision d’investissement et les travaux, puis la création de l’équipe et l’apprentissage du procédé. En parallèle il a fallu bâtir une histoire et se présenter sur le marché, aller chercher des clients, commencer une longue étape d’évangélisation. Nous avons dès le début ciblé le marché aéronautique, ce qui signifie une approche très rigoureuse du procédé et des processus qualité. Une étape importante a donc été la qualification de notre première machine par l’un de nos clients clefs, le groupe Safran.
En 2017 nous avons pris conscience de la nécessité de monter le niveau de qualité de notre outil industriel pour accompagner les donneurs d’ordre de l’aéronautique, nous avons donc décidé de transférer notre activité sur un nouveau site. Cette décision importante s’est traduite par un redémarrage de notre activité sur ce site fin 2018. En parallèle de ces choix industriels, il a été nécessaire de continuer à convaincre les actionnaires de financer le projet ; une dernière étape clef a été pour nous la levée de fonds effectuée en juin 2018 auprès de la société de gestion Demeter Ventures.
Quelle est l’activité de Multistation SAS ?
Y. L. : Multistation est aujourd’hui un intégrateur de solutions complètes de fabrication additive et digitale. Elle propose des machines, des logiciels et des services à une clientèle industrielle, prestataires de services comme Spartacus3D, ETI ou grands groupes, et bien entendu le monde de l’éducation.
Comment t’est venue l’idée ?
Alors dirigeant de la filiale française du premier groupe européen de machines-outils, j’ai eu l’occasion en 1987 de créer avec Dominique Humblot une société destinée à commercialiser les machines d’usinage 5 axes, alors fondamentalement novatrices, et les logiciels de fabrication assistée par ordinateur. Et dès le début des années 90 nous avons compris l’intérêt de l’ajout de matière, caractéristique de la fabrication additive par rapport à l’enlèvement de matière réalisé par les méthodes traditionnelles d’usinage. Nous avons créé en 1992 l’AFPR, Association française de prototypage rapide, première du genre au monde, et organisé les premières Assises du prototypage rapide à l’École polytechnique.
Quel est le parcours des fondateurs ?
Dominique est docteur en mathématiques et j’ai repris sa participation deux ans après la création de Multistation. J’ai commencé ma carrière au Bureau Veritas comme ingénieur naval, avant de rejoindre des sociétés internationales de commerce industriel.
“Les premières Assises du prototypage rapide
ont eu lieu à l’École polytechnique.”
Qui sont les concurrents ?
Notre portefeuille d’activités est aujourd’hui très diversifié, de la fourniture de machines à l’éducation ou à une plate-forme internationale de marché pour les grosses machines de fabrication additive industrielle. Nous avons de multiples canaux de distribution, ce qui fait que notre business modèle n’est pas très standard ; nous avons donc des concurrents différents selon chacune de nos activités.
Quelles ont été les étapes clefs depuis la création ?
Ces étapes clefs sont les crises économiques qui n’ont cessé de secouer l’industrie française… Mon obsession a été d’y survivre et donc de choisir un mode de remise en cause permanente, basé avant tout sur une offre originale, innovante et disruptive, des machines qui permettent de produire ce que l’on ne savait pas faire auparavant ! Cette expérience se révèle particulièrement utile dans cette période de pandémie où le rôle de l’impression 3D vient d’être mis en valeur par son agilité à réagir dans la crise de la Covid-19.
Quelles seront les étapes clefs dans le proche futur qui auront un impact sur notre activité ? J’en vois quatre. Tout d’abord que sera « le monde d’après » lorsque des pans entiers de l’industrie sont en situation de sidération… Nous voyons des concepts nouveaux se développer à grande vitesse pour prendre en compte la digitalisation, les difficultés logistiques, la remise en cause de la globalisation, l’impossibilité de se déplacer, et surtout le besoin de produire près des lieux d’usage… Après une phase de progrès puis d’innovation, la production industrielle se régénérera dans le monde d’après et nous essaierons d’être présents pour lui fournir de nouveaux équipements.
Le second point est la prise en compte du formidable essor de l’industrie chinoise, sa capacité d’innovation portée par son marché intérieur et sa volonté stratégique de venir en Europe, c’est la raison pour laquelle nous travaillons sur la création de Multistation China. Troisièmement, la fabrication additive doit faire l’objet d’une réflexion globale dans l’entreprise d’après, ce qui génère un fort besoin d’ingénierie et de consulting, d’où la création de notre filiale spécialisée Additiv3X en lien avec les majors du domaine. Enfin le marché de l’occasion, où nous sommes très présents via notre plate-forme mondiale Multistation second life, va faire l’objet d’une forte croissance : crise actuelle, lancement anarchique de nouveaux modèles vite obsolètes, misinvestment, volonté des primo-utilisateurs de faire leurs premières armes sur des machines moins chères…
Nous nous développerons en adaptant notre modèle au « monde d’après », volatil, incertain, complexe et ambigu, en suivant bien sûr la doctrine d’Edgar Morin : « Attends-toi à l’inattendu. »
“L’Europe se fait doubler par une Chine
lancée à toute vapeur.”
Pour terminer, une question commune pour les deux entrepreneurs : quel est l’avenir de la 3D ?
Le dicton affirme à juste titre que c’est en forgeant que l’on devient forgeron. Il en va de même avec l’impression 3D qui est une practice based technology et s’inscrit dans une chaîne de valeur universelle. Cet écosystème se décline suivant les métiers. Par exemple la haute joaillerie a parfaitement intégré l’impression 3D alors que le matériel minier n’en est qu’aux prémices. Les multiples procédés de fabrication additive génèrent une foultitude d’opportunités suivant les métiers, qui sont tous impactés. Mais une telle évolution, parfois anarchique, freine les investissements du fait des interrogations qu’elle suscite. Ce besoin d’ingénierie et d’étude des besoins de l’entreprise est récent et en pleine explosion. La POC (proof of concept) devient la règle universelle !
Dans le monde, il existe plusieurs centaines de fabricants d’imprimantes 3D : beaucoup de pâles copies des leaders, un flux d’entrants permanents et des échecs significatifs… Marketer l’impression 3D n’est pas simple car trop d’anecdotes nuisent à la crédibilité de la technologie. Cet engouement 3D est mondial et a créé de fortes disparités autour des trois pôles américain, chinois et européen. Prenons l’exemple de la courbe de Hype, qui décrit l’évolution de l’intérêt pour les nouvelles technologies ; il est facile de constater que les vitesses de déplacement de chaque technologie varient d’un pays à l’autre ; l’Europe, engluée dans ses normes et ses hésitations, se fait doubler par une Chine lancée à toute vapeur.
En résumé, la fabrication additive s’invite de plus en plus à la table des dirigeants, elle constitue un outil fantastique pour définir les orientations stratégiques en matière d’innovation produit et d’organisation de la production. Elle modifie en profondeur la pensée design de l’entreprise, en permettant un apport émotionnel à des fonctions jusqu’alors strictement opérationnelles. Elle a pour effet de raccourcir le délai entre le concept et la réalisation du premier prototype et également de personnaliser la production. La fabrication additive est l’outil idéal pour développer l’agilité de l’entreprise face à ses concurrents. Mais les écueils sont là et ont le mérite d’être de mieux en mieux identifiés. Car la fabrication additive génère un sentiment de volatilité et d’incertitude qui affecte certains salariés.
Thierry Rayna, enseignant chercheur à l’École polytechnique interrogé par Les Échos du 4 mai 2020, a déclaré : « Si une partie des productions reviennent en France ou en Europe, elles se feront sur des séries plus courtes et les nombres d’applications favorables à l’impression 3D augmenteront. Tout recul du commerce mondial et hausse des prix du transport constituent un bon point pour l’impression 3D. » Suivant le consultant Phil Reeves, la fabrication additive bénéficiera dans « le monde d’après » du développement de l’économie circulaire et de la réutilisation des objets : « Si l’on s’éloigne de cette économie de la consommation effrénée pour valoriser la réparation ou la réutilisation, l’impression 3D prendra une place majeure. On pourra fabriquer les pièces qui prolongeront la vie de nos objets du quotidien et leur donneront même une nouvelle fonction. »
Le monde d’après qui se profile constitue une formidable opportunité pour l’impression 3D, particulièrement la fabrication additive faisant appel au métal, désormais la plus prometteuse. Eu égard aux grandes tendances sociétales du monde de l’après-Covid, la fabrication additive bénéficie d’une image bien vertueuse !
