Expérimenter pour mieux relever les défis de la transformation industrielle


Le passage à l’industrie du futur est pour la France une opportunité d’accélérer sa transformation industrielle, à condition de savoir relever les défis induits par cette transformation. L’expérimentation est indispensable pour la comprendre et la maîtriser et c’est ce qui a amené le BCG à ouvrir des centres d’expérimentation.
L’industrie 4.0 se caractérise par l’intégration de nouvelles technologies au sein des processus de fabrication, elle fait vivre une profonde transformation à nos sites industriels, tant sur les lignes de production que dans les méthodes de management. Après les robots, c’est au tour des cobots (robots collaboratifs) d’apparaître dans les usines. Les opérateurs peuvent alors programmer eux-mêmes ces compagnons de travail qui réalisent les tâches les plus simples et libèrent du temps qui sera consacré aux tâches à plus forte valeur ajoutée. Avec les dispositifs de réalité augmentée (via des lunettes par exemple), les manuels d’utilisation disparaissent et les opérateurs ont un accès immédiat aux gestes justes et même, dans certains cas, à des experts à distance. L’internet industriel permet quant à lui de connecter les différentes technologies entre elles et en décuple la performance. Autre exemple, l’accès et l’analyse de données en temps réel permettent une meilleure gestion de l’énergie, un meilleur contrôle des paramètres de production ou la mise en place de programme de maintenance prédictive. Ce ne sont que quelques exemples de cette vaste transformation.
REPÈRES
Comparable aux trois précédentes révolutions industrielles caractérisées par la machine à vapeur, le fordisme puis l’automatisation, l’industrie 4.0 ou industrie du futur se déploie dans nos usines depuis plusieurs années.
Une productivité et une réactivité fortement accrue
Le déploiement des nouvelles technologies industrielles permet des gains de productivité de l’ordre de 15 à 25 % sur les coûts de production hors matières premières et des gains de flexibilité de 25 à 40 %. De tels bénéfices sont de nature à remettre en cause les équilibres établis observés durant des décennies : pourquoi produire loin des pays de consommation lorsque les gains de productivité sont à portée de main localement ? Pourquoi produire dans des usines spécialisées et de grande taille quand la technologie permet dorénavant de capturer les effets d’expérience de façon distribuée ? Pourquoi produire sur stock quand les coûts de changement de lot de production sont réduits à zéro ? L’industrie 4.0 permet dorénavant de produire localement des lots uniques à des coûts équivalents. Le paradigme est ainsi renversé, les nouvelles technologies permettent à nos usines de changer d’ère. Terminées les usines de grande taille et spécialisées par produit. Le fonctionnement en stock laisse place à la production à la demande, permettant de vendre des produits adaptés à chacun, au plus près du lieu de consommation.
Quatre défis pour les industriels
Avec quels défis ? Afin de capturer ces bénéfices sur l’intégralité de la chaîne de valeur, plusieurs défis s’imposent aux industriels. Il faut en premier sensibiliser les directions et leurs équipes. L’industrie 4.0 demeure méconnue : seuls 13 % des dirigeants de PME et ETI considèrent la transformation digitale comme une priorité stratégique d’après un sondage réalisé en 2017 par Bpifrance. Ceux-ci doivent devenir familiers de cette transformation afin d’en impulser l’élan et de mobiliser leurs équipes.
Deuxième défi : développer les talents adéquats. Des professions deviendront obsolètes et de nouveaux savoir-faire – traitement des données, programmation… – seront incontournables dans l’usine du futur. L’apparition de nouveaux métiers et de nouvelles compétences appelle à une transition sociale et place la formation – des jeunes générations et des actifs – en priorité stratégique.
Troisième défi : accompagner la transition. Un accompagnement orchestré par des experts du digital et des questions de lean management constitue la condition sine qua non à la réussite de cette transformation.
Enfin, dernier défi : mobiliser l’écosystème. L’implication des acteurs industriels doit s’accompagner d’un engagement de l’écosystème dans son intégralité : entreprises privées, pouvoirs publics, écoles, universités, fournisseurs de technologies…
“Deux ans après son ouverture,
le centre de 1500 m² a accueilli plus de
3 000 dirigeants industriels venus du monde entier”
L’occasion d’accélérer la transformation industrielle de la France
Si plusieurs initiatives vont dans le bon sens, la dynamique de déploiement de l’industrie du futur en France reste trop lente. Afin d’infléchir cette tendance et de répondre aux défis précédemment mentionnés, le BCG – en partenariat avec l’Institut Montaigne – a publié en septembre 2018 un rapport préconisant l’ouverture de centres d’accélération de l’industrie du futur sur l’ensemble du territoire français. Au nombre de 15 à 20, ces centres maillant filières industrielles et territoires permettront de mettre en relation l’intégralité de l’écosystème pouvant concourir au développement de ces nouvelles technologies. Dès lors, fournisseurs de technologies, start-up, universités, écoles, entreprises de conseil mais aussi organismes de financement permettront d’impulser la dynamique sous la gouvernance d’industriels et en étroite relation avec les régions. En remplissant trois objectifs – encourager l’innovation, permettre la formation et proposer un accompagnement aux PME et ETI – ces centres doivent aider la France à faire face à la vélocité de nos concurrents étrangers et à renouer avec sa tradition manufacturière.
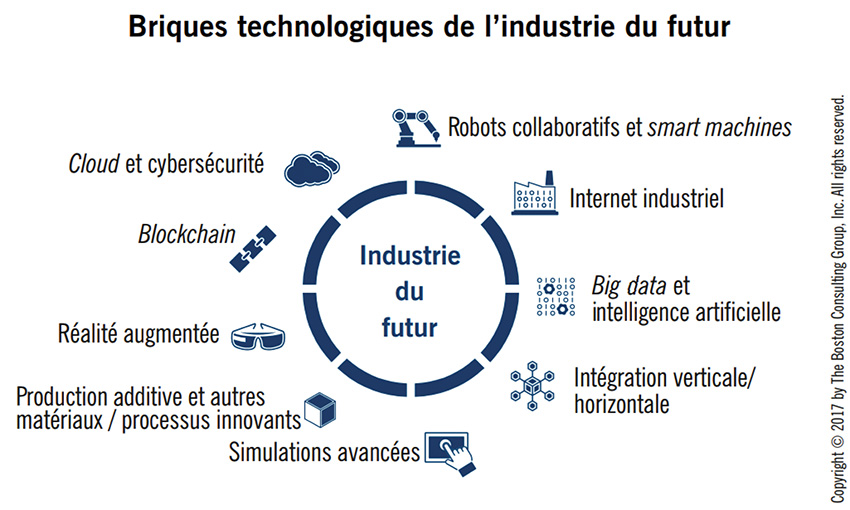
L’ICO, centre d’expérimentation de l’industrie du futur à Saclay
Afin d’accompagner et de sensibiliser l’intégralité de l’écosystème industriel, le BCG a ouvert en septembre 2016 l’Innovation Center for Operations (ICO). Un concept innovant et pionnier ! Implantée sur le plateau de Saclay, cette usine pilote dispose de deux lignes de production grandeur nature : une ligne produisant en même temps des scooters électriques et des sèche-linges, la seconde produisant des bonbons. Qu’il s’agisse de problématiques touchant aux industries de process (sollicitant fortement les équipements) ou d’assemblage (sollicitant plus fortement les employés sur les lignes de production), le centre permet d’étudier très concrètement l’impact des nouvelles technologies sur la performance des opérations (coût de production, productivité, consommation énergétique…). La palette de technologies implémentées est large : robots et machines collaboratives, fabrication additive, réalité augmentée, big data et solutions analytiques, intelligence artificielle, intégration digitale, cybersécurité et blockchain. Sur la chaîne de scooters, les roues pesant plus de quinze kilos sont guidées par des cobots (robots collaboratifs). Ceux-ci aident les opérateurs et améliorent leur ergonomie. La charge cognitive est quant à elle optimisée lors de l’assemblage du compteur. Celui-ci est en effet assisté par la réalité virtuelle, ce qui permet une réduction par deux du temps d’assemblage. Sur la ligne de bonbons, les capteurs nouvelle génération permettent de mesurer en temps réel une multitude de données (température, vitesse de production…). Celles-ci sont transmises aux opérateurs grâce à des tablettes. Grâce à l’intelligence artificielle (IA), leur analyse rend possible la détection d’anomalies. Ces exemples permettent de développer de nombreux cas d’usage et font de l’ICO une structure apprenante dont la productivité et la performance s’améliorent en permanence.
Au-delà de sélectionner les bonnes technologies, l’usine-école du BCG permet d’appréhender concrètement leur intégration entre elles, les contraintes liées à leur mise en place et les modalités d’exécution rapide pour améliorer les performances industrielles de manière massive et pérenne. Les solutions sont intégrées à des machines de différentes marques, anciennes comme récentes. Elles reflètent la réalité et la complexité d’un site de production.
Loin de se cantonner à ces lignes de production, l’ICO dispose d’un espace dédié à la supply chain et aux services 4.0. On découvre alors l’impact de la technologie sur les fonctions dites back et middle office (gestion administrative et comptable, ressources humaines, procurement, etc.). Les solutions présentées permettent dans ce cas d’automatiser des processus intellectuels grâce au RPA (Robotic Process Automation) et à l’IA.
Afin de garantir une expérience complète et immersive, l’ICO anime un écosystème innovant qui accueille à la fois des acteurs académiques – comme CentraleSupélec – mais aussi des start-up technologiques comme Braincube, Surycat, iObeya, Metron, Diota, Mesotechnic et des groupes internationaux spécialisés comme Kuka, Infeeny|Econocom, Fanuc, Universal Robots ou Tulip. De grands industriels – tels que Dassault Systèmes ou Microsoft – sont également impliqués depuis la genèse du projet.
La mise en place de ces technologies modifiera l’environnement de travail en le rendant paradoxalement plus enrichissant, plus humain et beaucoup plus évolutif. Le centre souligne en ce sens l’importance de l’humain dans cette transition : la technologie est un levier qui ne pourra être activé sans la mobilisation et l’engagement des équipes.
Deux ans après son ouverture, le centre de 1 500 m² a accueilli plus de 3 000 dirigeants industriels venus du monde entier. Le BCG a également développé le réseau ICO : des centres similaires ont ouvert en Allemagne, au Brésil, aux États-Unis ainsi qu’à Singapour. Souvent qualifiés d’accélérateurs de réflexion par les visiteurs, ceux-ci permettent de démystifier l’industrie 4.0 en rendant palpables les enjeux qui l’accompagnent. Les experts de l’ICO permettent aux entreprises et à leurs dirigeants de préparer au mieux la transformation digitale de leur site à grande échelle. Une nouvelle adresse française – dédiée à l’industrie pharmaceutique à Strasbourg – étoffera le réseau en 2019 !
Relocalisations
Le manufacturing 4.0 dessine donc une nouvelle géopolitique industrielle : les usines quittent peu à peu les pays émergents pour rejoindre nos pays matures sous un format plus réduit, plus agile et plus écologique.