FORMNEXT : le plus grand salon mondial de l’impression 3D
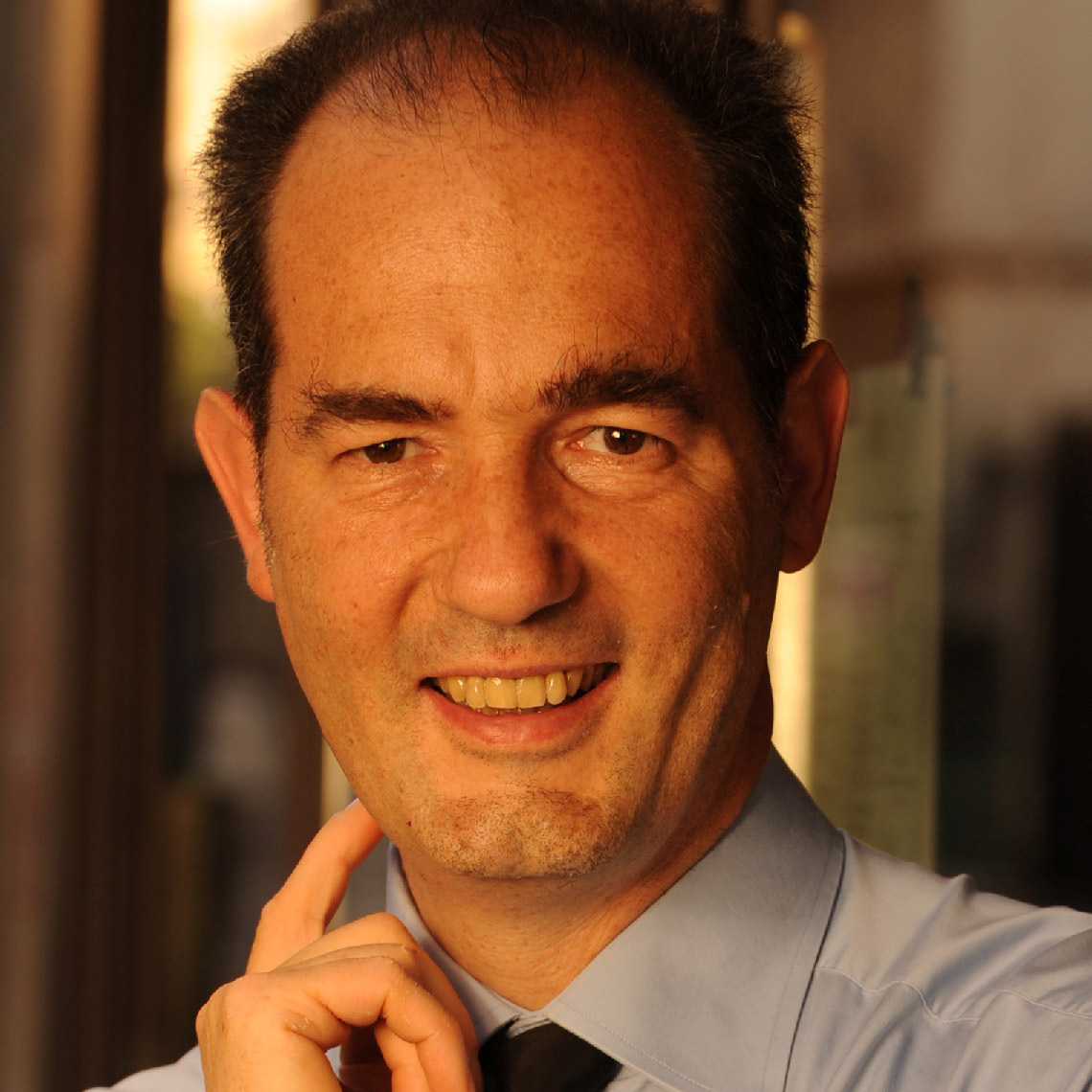
Cette manifestation plutôt récente s’impose comme le véritable rendez-vous mondial de la fabrication additive (FA), ou additive manufacturing en anglais. Pourquoi en parler ? Parce que tous les acteurs de la chaîne de valeur sont présents à ce salon et parce que, crise de la Covid oblige, c’était le dernier événement réunissant l’impression 3D, les rendez-vous de ce printemps ayant tous été annulés.
On vient à Formnext des quatre coins du monde. Après l’Allemagne, les pays les plus représentés sont la Chine, les États-Unis, la France, l’Italie, le Royaume-Uni, l’Espagne et les Pays-Bas. Tout l’écosystème de la FA est présent, logiciels de design et de conception, matériaux, procédés, machines d’impression, les post-traitements des pièces produites, leurs contrôles. Sans oublier l’impact humain sur les équipes et leur sécurité ainsi que les contraintes environnementales que doit respecter la fabrication additive.
REPÈRES
Depuis 2014, la fabrication additive se réunit fin novembre à Francfort dans le parc d’exposition Messe. Ce salon, qui tenait sur un seul niveau d’un hall d’exposition lors de la première édition, puis l’année précédente sur un hall et deux niveaux gigantesques, occupait pour cette dernière édition (2019) deux halls et quatre niveaux, soit + 60 % de surface d’exposition entre 2018 et 2019 et + 240 % en cinq ans. Il fallait au moins deux pleines journées pour parcourir les 50 000 m2 d’exposition de l’édition 2019. Cette cinquième édition affiche une forte croissance, tant par le nombre d’exposants, 867 contre 632 en 2018 (+ 37 %), que par celui des visiteurs, 35 000 contre près de 27 000 en 2018 (+ 28 %). 285 entreprises – soit un tiers des exposants – venaient pour la première fois au salon.

La fabrication additive est vue comme un futur Eldorado
Un des fins observateurs des cinq éditions me le faisait remarquer : ce salon est un vrai contraste entre la débauche d’opérations marketing et la réalité du marché de l’impression 3D. En effet, si Forbes estime début mai 2020 que l’en
semble de la chaîne de valeur de la fabrication additive représente près de 12 Md$ en 2019, avec 25 Md$ attendus en 2025, la plupart des acteurs ont du mal à gagner de l’argent. La plupart ne sont pas cotés et ne publient donc aucune information financière mais, si l’on considère trois des sociétés qui ont parmi les plus beaux stands du salon et qui sont cotées, on trouve :
SLM Solutions (Allemagne), dont le chiffre d’affaires 2018 était de 72,0 M€ pour 13,4 M€ de pertes et dont le chiffre d’affaires 2019 est de 49,0 M€ pour 47,1 M€ de pertes, a une capitalisation boursière début mai 2020 de 130,0 M€ – alors que GE avait fait une offre sur cette société à environ trois fois le pic historique de sa capitalisation boursière. Hélas pour les dirigeants et actionnaires, un fonds activiste américain a voulu faire monter les enchères et GE a changé du jour au lendemain son fusil d’épaule pour un concurrent… Le capital-risque me l’a appris, les occasions de rêve ne passent jamais deux fois.
Stratasys (USA, Israël), dont le chiffre d’affaires 2018 était de 663,0 M$ pour 8,8 M$ de pertes et dont le chiffre d’affaires 2019 est de 636,0 M$ pour 11,7 M$ de pertes, a une capitalisation boursière début mai 2020 de 900 M$ alors que la société avait dépassé les 5 Md$ en 2014.
3D Systems (USA), historiquement la première société d’additive manufacturing, dont le chiffre d’affaires 2018 était de 688,0 M$ pour 45,5 M$ de pertes et dont le chiffre d’affaires 2019 est de 629,0 M$ pour 67,7 M$ de pertes, a une capitalisation boursière début mai 2020 de 850 M$ alors que la société avait dépassé la valeur de 10 Md$ en 2014.
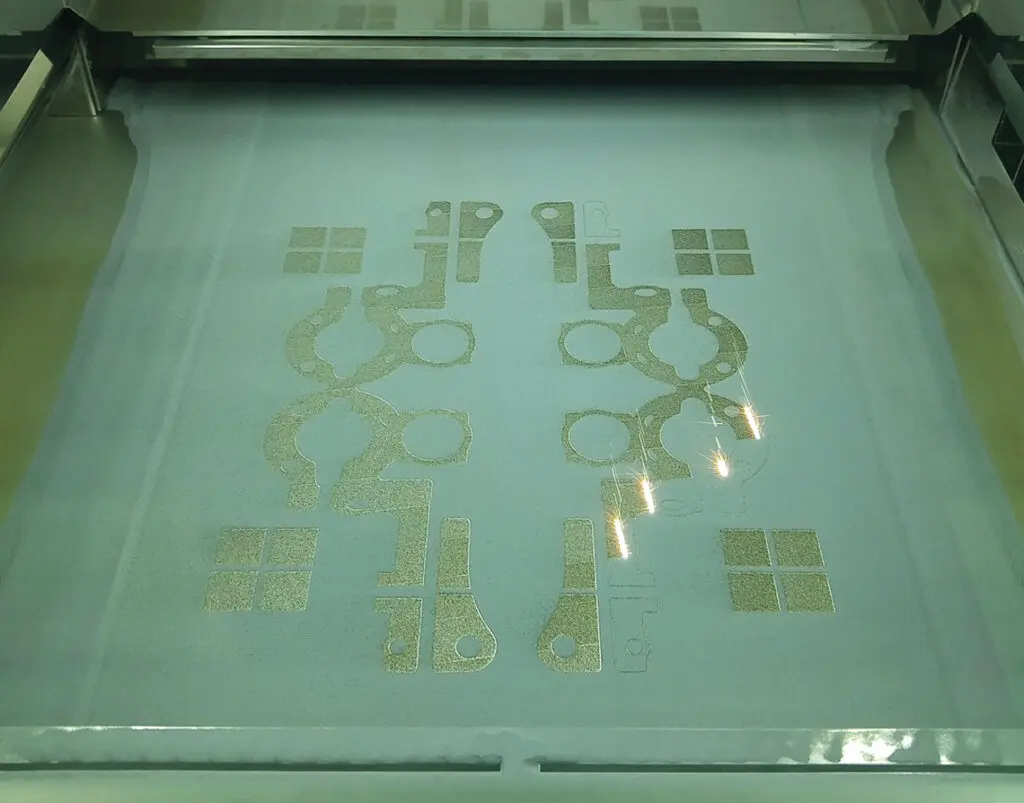
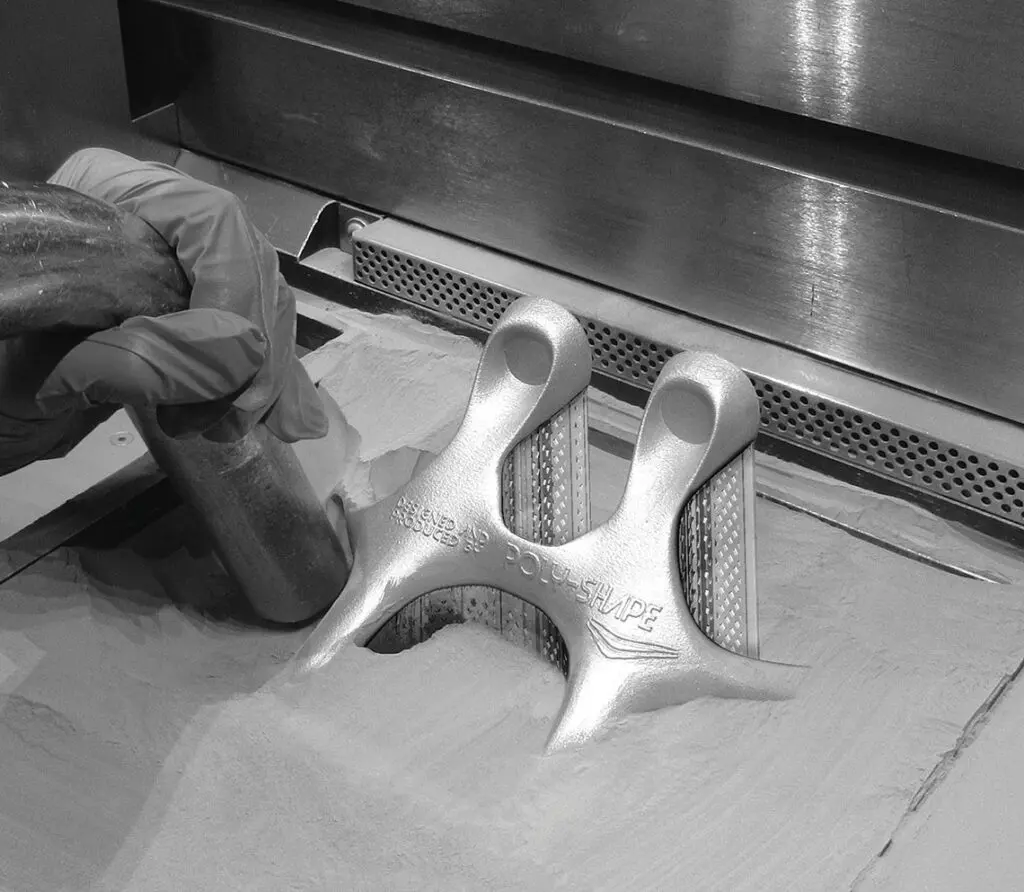

Une brève histoire de la fabrication additive
Tout commence en 1984, à la fois sur le plateau de Saclay – où l’invention, brevetée, restera dans des cartons – et aux États-Unis où Chuck Hull fondera 3D Systems avec le premier procédé mis au point, la stéréolithographie : elle utilise un laser ultraviolet qui chauffe un photopolymère liquide et le solidifie couche par couche. Très vite, un concurrent de taille va apparaître dans le domaine des machines d’impression des matériaux polymères, Stratasys : ces deux constructeurs d’imprimante pour polymères domineront le marché jusqu’en 2014–2015 où leur capitalisation boursière dépassera les 5 Md$, multipliant les acquisitions de technologies ou de start-up achetées beaucoup trop cher et le plus souvent mal intégrées. L’histoire se répète pour General Electric qui a procédé à de très nombreuses acquisitions achetées très cher, comme les fabricants de machine Concept Laser et Arcam – pour 1 250 M€ en 2016, un prix stratosphérique à en croire les experts. L’offre initialement faite sur SLM Solutions était 850 M€, soit 1,4 Md$ pour à la fois Arcam (seul fabricant au monde d’imprimantes métal à faisceau d’électrons) et SLM Solutions, des montants extravagants en termes de ROI.
Depuis 2014, des géants industriels comme GE, HP, Ricoh, et l’année dernière Rank Xerox, etc., sont entrés à différents niveaux d’implication dans la FA et présentent de beaux stands à Formnext… Que ce soit dans les matériaux polymères ou dans les matériaux métalliques, l’offre 2020 fourmille de très nombreuses solutions ou machines, à tel point qu’il devient difficile de choisir… De nouveaux modèles et technologies apparaissant, on peut être tenté d’attendre la prochaine machine de fabrication additive, plus précise, plus rapide, avec de plus grands volumes de production…
“Tous les segments
de la 3D sont devenus très concurrentiels.”
Une douzaine de famille de procédés
Beaucoup de techniques se sont développées et on recense aujourd’hui plus d’une douzaine de familles de procédés différents suivant les matériaux utilisés (plastique, métal, céramique, composite, sable, résine, silicone…), leur forme (poudre, filament, fil, bâtonnets…) ou le type d’énergie utilisé (laser, faisceau d’électrons, arc électrique, plasma, simple chauffage…). L’avantage de l’impression 3D tient à la rapidité de la chaîne conception-fabrication et son faible investissement (pour un système complet de production). Son inconvénient est la cadence de production trop basse ou trop chère en général pour une production de masse, mais il y a des exceptions et elles vont se multiplier. Notons qu’on peut imprimer des pièces directement ou imprimer des moules pour obtenir de grandes séries, comme le fait Michelin qui imprime un million de moules par an pour les sculptures de ses pneus. Suivant le métier (aéronautique, médical, dentaire, joaillerie, construction, énergie, biologie…), la géométrie des pièces, leur niveau de précision ou de criticité, l’état de surface recherché, la taille des séries, le souci de personnalisation…, l’enjeu est de sélectionner le bon procédé.
La fabrication additive métallique
Le plus fort développement est attendu dans la FA métallique et composite, avec des moyens de production hybride combinant divers procédés additifs et soustractifs. Il y avait moins d’une dizaine d’acteurs dans le métal il y a dix ans, ils étaient 150 exposants sur l’édition Formnext 2019, les fournisseurs aussi bien de poudre que de machines, que de post-traitements, que de soft pour des simulations, etc. Le métal est un écosystème largement développé qui a la croissance la plus élevée. Pour prendre l’impression 3D en métal la plus répandue, la technologie laser-lit de poudre (SLM ou LBM), on dénombre les acteurs industriels allemands SLM Solutions, EOS, Trumpf, DMG Mori, l’anglais Renishaw, le hollandais Additive Industries, le français AddUp, le chinois Farsoon, les américains Velo3D, General Electric qui a racheté l’allemand Concept Laser en 2016, 3D Systems qui a racheté le français Phenix Systems en 2013. Tous ces acteurs sont sur le salon avec des stands énormes, voire démesurés pour GE, EOS, Trumpf. Le procédé SLM est très utile si on a besoin de précision, de structures complexes géométriquement, avec une santé-matière très exigeante, ou de densité très forte.
AddUp, filiale de Michelin et Fives créée fin 2015
En ce qui concerne les nouveautés dans le métallique, citons SLM Solutions qui a montré la proof of concept d’une machine métal avec une dizaine de lasers ; la multiplication du nombre de lasers permettrait d’augmenter la productivité ou d’accélérer la vitesse de construction des pièces. Parmi les machines en technologie laser-lit de poudre offrant un grand volume, citons la SLM 800, avec 4 lasers agissant sur une chambre de volume 500 x 280 x 850 mm. Le français AddUp est présent avec des solutions pour ses machines laser-lit de poudre qui peuvent utiliser des poudres extrêmement fines pour des pièces métal de grande précision, tout en assurant une sécurité maximale pour les opérateurs. AddUp accueille aussi les machines BeAM – achetées mi-2018 à une valorisation très bien négociée par Jean-Dominique Senard, à l’époque PDG de Michelin, qui est très mal passée pour la plupart des prestigieux actionnaires qui avaient permis à cette société de naître et de se développer. BeAM construit des machines de projection de poudre métallique, technologie beaucoup plus rapide, adaptée à la construction de grandes pièces et au rechargement (pour la réparation de pièces, de moteur d’avion par exemple) comme à l’ajout de fonctions sur des pièces réalisées par d’autres procédés : l’une de ces machines équipe le laboratoire de mécanique de l’X. AddUp a aussi acheté le français Poly-Shape, prestataire de services spécialisé dans la réalisation de pièces techniquement très avancées pour Dassault Aviation, Airbus, etc., qui possède un parc machines de plusieurs constructeurs.
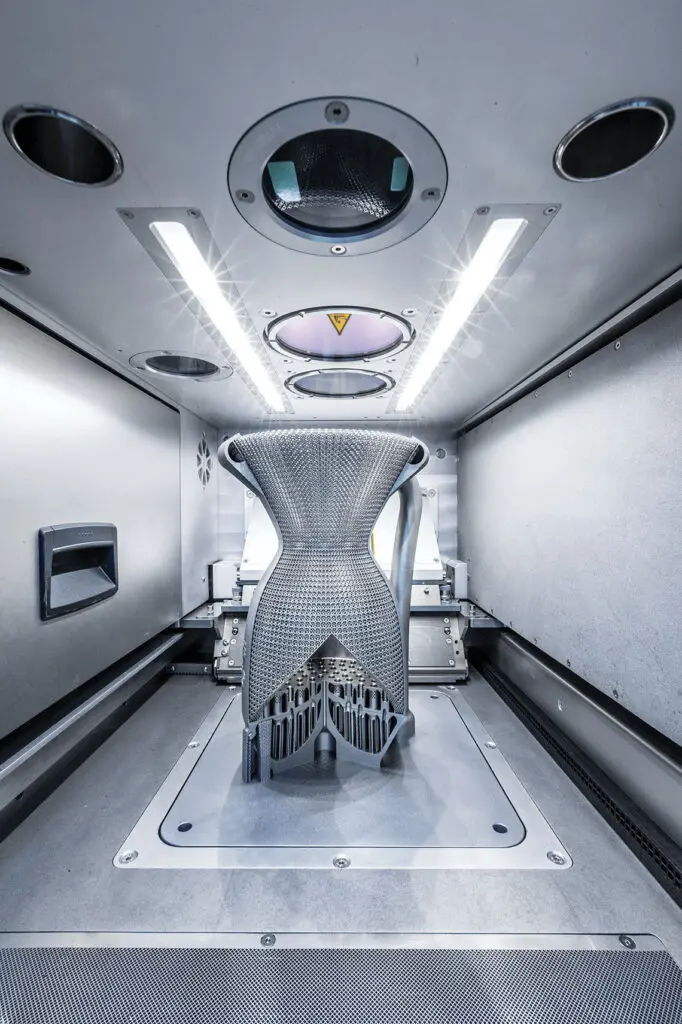
et les post-traitements imprimée sur SLM 280 en superalliage base nickel 718 en 5 jours : parfait exemple de lightweight construction.
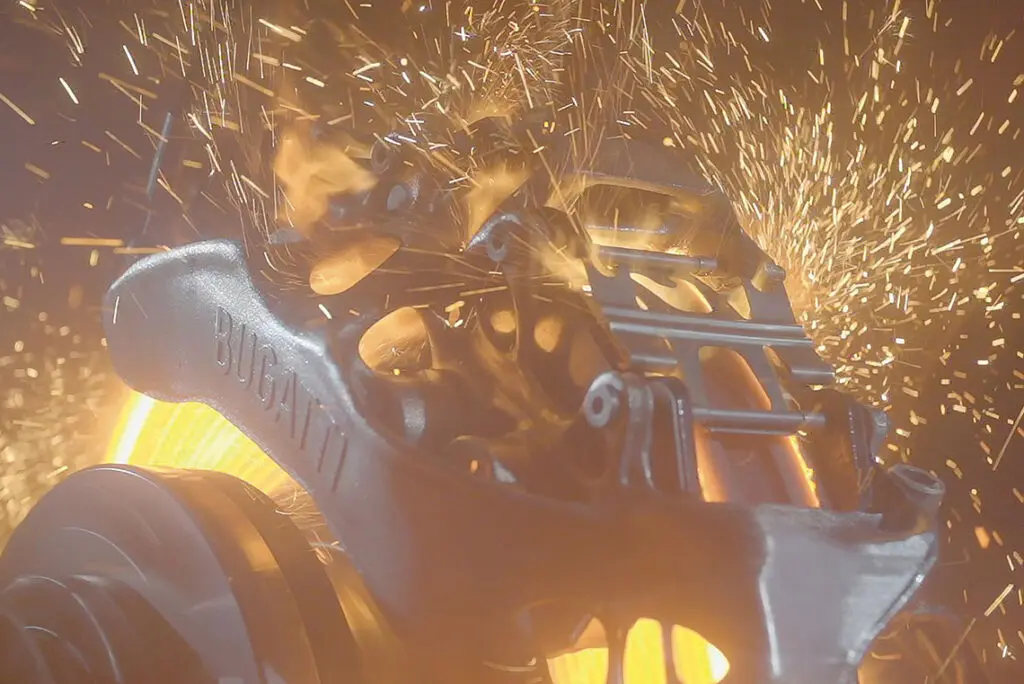
Stratasys nous en fait voir de toutes les couleurs
Sur le plateau supérieur, on retrouve 3D Systems qui présente des machines d’impression métal ou polymères et, tout proche, son concurrent de toujours, Stratasys, qui présente des machines d’impression en résines et polymères. Notons que leur nouvelle machine J850 est la première machine d’impression 3D au monde qui permette d’imprimer avec plus de 500 000 nuances de couleurs certifiées par Pantone une infinité de matériaux composites, présente une capacité de charger jusqu’à sept matériaux différents mixés au niveau du voxel – qui est à la 3D ce que le pixel est à la 2D – avec une précision de ± 100 µ pour un volume de fabrication de 490 x 390 x 200 mm.
Un point sur le binder jetting
C’est une technologie d’impression nettement plus rapide. Sur des métiers qui vont demander une productivité plus importante ou un nombre de pièces en série plus important, le binder jetting – qui construit des pièces plus rapidement que la technologie SLM – peut être une réponse très intéressante. Sur ces machines, à chaque passage il y a un dépôt de matière sous forme de poudre et de liant ; cette matière (poudre) est frittée, c’est-à-dire chauffée dans des fours très haute température – il faut bien entendu enlever toute poudre non utile car sinon, au moment du frittage (élévation de température), la poudre non désirée pourrait s’agglomérer avec la pièce. Il y a un retrait très important, de l’ordre de 20 % à 24 %, et la pièce devient dense à 98 % – comme on le fait avec la céramique. Cette technologie n’est cependant pas adaptée pour certaines structures complexes : les pièces métal nécessitant de très hautes précisions continueront à utiliser le procédé laser-lit de poudre. Les producteurs de ces machines d’impression 3D sont ExOne (Israël) et Digital Metal (Suède), ExOne, le pionnier de cette technologie, produisant aussi des machines qui impriment du sable et vendant des systèmes depuis de nombreuses années. Il y a aussi Desktop Metal (start-up et licorne issue du MIT, née en 2015, qui a levé 440 M$, soit le financement en capital-risque le plus important jamais réalisé dans la fabrication additive) et HP. Pour HP comme pour Desktop Metal, cela reste un effet d’annonce, avec pour l’instant quelques machines de bêta-test sans offre commerciale autre que pour polymères.
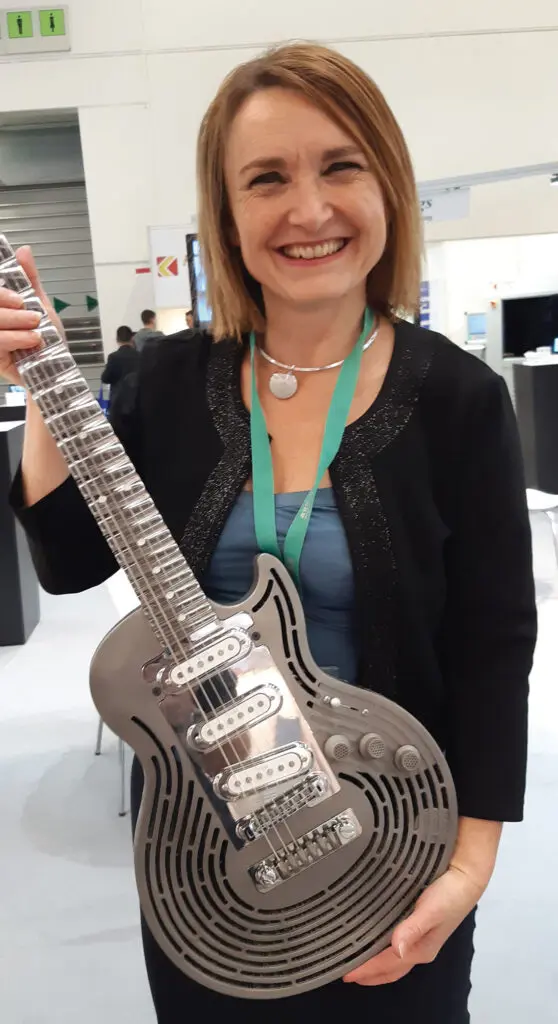
Aubert & Duval, chef des ventes pour les poudres métalliques.
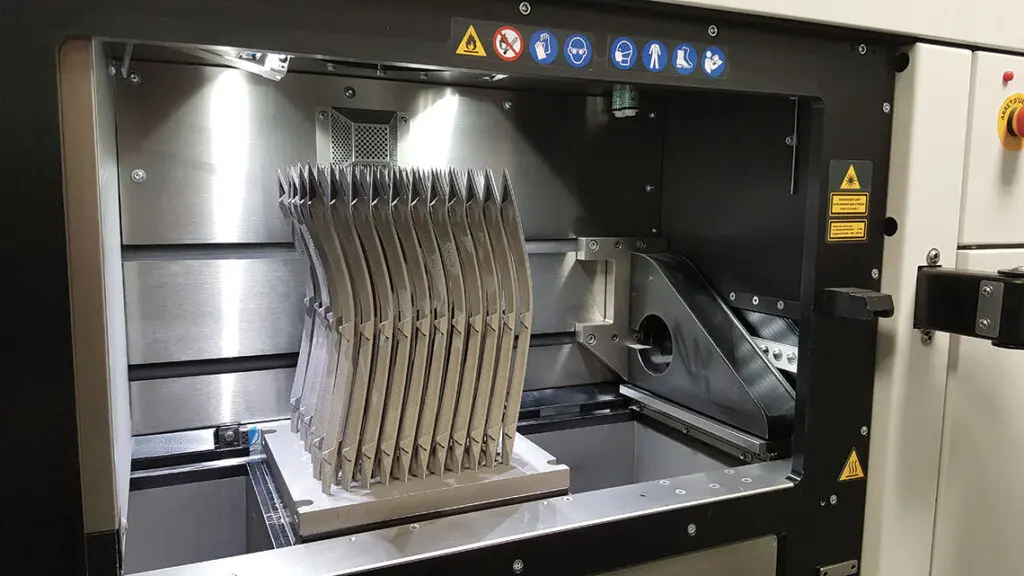
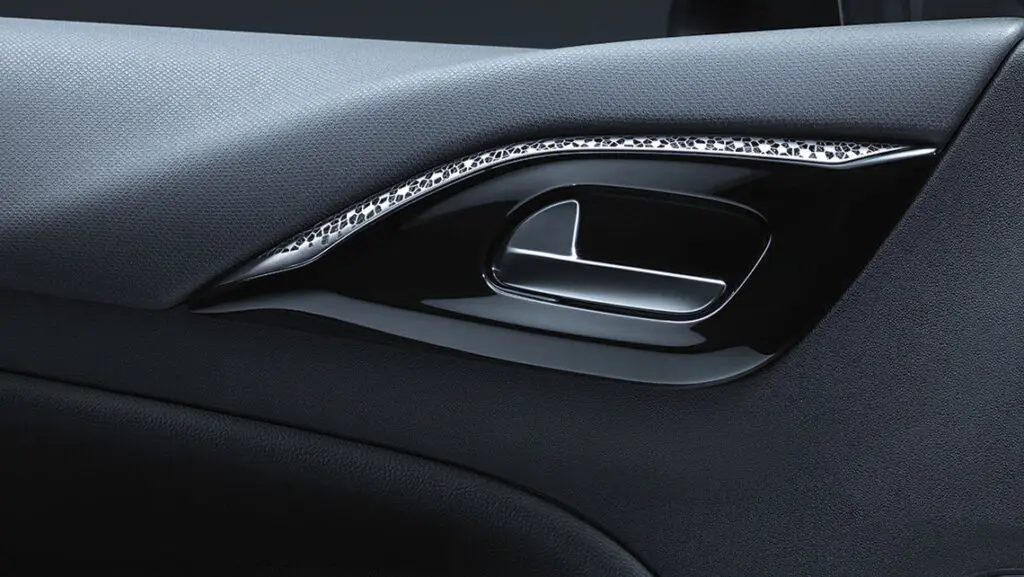
La galaxie EOS
Dans le troisième hall, on entend le son puissant d’une guitare électrique indestructible smash-proof imprimée en titane par le suédois Sandvik qui fait résonner des accords très rock. À l’étage, on trouve le fabricant allemand EOS. Avec un chiffre d’affaires de 350 M€, la société fondée en 1989 est le leader dans le secteur du frittage laser direct métal ainsi que polymère, avec un total de 3 800 imprimantes 3D industrielles vendues dans le monde, dont 450 systèmes en 2019. Le triptyque système-matériau-paramètres d’EOS permet de garantir qualité et répétabilité des pièces imprimées, et donc de produire en série des pièces industrielles, aussi bien en plastique – avec des volumes jusqu’à 700 x 380 x 580 mm – qu’en métal avec des volumes jusqu’à 400 x 400 x 400 mm et 4 lasers. Des modules sont disponibles pour automatiser au maximum toutes les étapes de fabrication et intégrer l’impression 3D dans des chaînes de production. EOS possède cinq autres sociétés dans l’additive manufacturing détenues à 100 %, dont ALM (Advanced Laser Materials) – pour le développement de poudres plastiques (PEKK et plastiques haute performance). EOS est détenue par la famille du fondateur qui vient de céder sa place de dirigeant à sa fille. C’est un écosystème, la famille ayant créé un fonds de capital-risque, AM Ventures, qui a des participations dans vingt sociétés, toutes dans la fabrication additive. On y retrouve par exemple DyeMansion, qui traite la partie post-processing pour les polymères, coloriages et traitements des surfaces, les sociétés de software 3YourMind et Additive Works, Sintratec, de toutes petites imprimantes en lit de poudre plastique, Lithoz, des imprimantes en céramique, AM Metals, qui développe des poudres métalliques (différents types d’aluminium, d’acier). La famille détient aussi en direct Scanlab, qui fait des scanners pour numériser des objets en 3D.
Les horaires du salon sont très classiquement de 9 h à 18 h mais le soir, à Formnext, nombreux sont les stands qui organisent une fête pour continuer de parler de FA. Ainsi, AM Ventures fait le deuxième soir avec toutes ses participations une soirée devenue un rendez-vous quasi incontournable baptisé avec à‑propos Rave til AM, où la bière coule à flots et rassemble tout cet écosystème…
Les logiciels
Parlons maintenant des logiciels, secteur en forte croissance. Commençons par le français Dassault Systèmes (3DS) qui offre une panoplie qui se complète chaque année et qui, après avoir mis sur le marché en 2017 une solution de modélisation 3D intégrant nativement de l’optimisation topologique pour des pièces soumises à des contraintes statiques, a dévoilé sa nouvelle solution d’optimisation fluide : optimiser la forme d’un conduit en minimisant les turbulences de perte de pression en sortie. Il y a bien sûr pléthore de logiciels de CAO : Autodesk, Siemens, 3DS (avec Catia) et Altair (roi de l’optimisation topologique). Il y a des logiciels de préparation de pièces pour la FA qui font le « supportage » et le « tranchage ». Le plus connu a été mis au point par le belge Materialise, un des grands prestataires de services pour la fabrication additive qui commercialise ainsi le soft qu’il a créé pour lui. De facto c’est le standard, mais il y a aussi Autodesk (Netfabb) et Siemens (NX), et encore Dassault Systèmes (Delmia). Passons au soft de simulation du procédé : il s’agit de lancer une analyse thermique qui va calculer la carte des températures pendant l’impression 3D. Dans le cas de gradients thermiques trop importants, la pièce accumule des contraintes résiduelles qui vont provoquer la distorsion de la pièce. Prédire ces distorsions et essayer de les éviter en changeant les paramètres du procédé de fabrication (puissance du laser, vitesse d’impression…), c’est ce que font Autodesk, Siemens, 3DS, Ansys (qui a racheté 3DSIM pour ce produit) et MSC (qui a acheté Simufact il y a quelques années), maintenant détenu par Hexagon.
Pour optimiser la production avec ESI Group
Additive Works (start-up de l’université de Brême) est un logiciel de simulation d’impression métal qui permet de visionner les tensions internes dans une pièce, anticipe les torsions, suggère un design en amont pour la fabrication. Par exemple, en CAO, on dessine une pièce de 10 mm mais, à la sortie, il va y avoir une distorsion de 1 %. Additive Works permet de redessiner la pièce, telle qu’on l’obtiendra à la sortie de 3D. Cette possibilité existe également chez Dassault Systèmes avec son application Virtual to Real Shape Morphing. Citons encore le français ESI Group qui propose avec ses spécialistes en physique des matériaux une solution complète, ESI AM, qui simule le procédé à différentes échelles et répond aussi bien à des questions liées à la fabricabilité (distorsions, contraintes résiduelles) qu’à l’optimisation en production et aux interrogations sur les propriétés matériaux et leur certification.
Les soft de gestion de la production
Grow est une solution de DRM (gestion des droits digitaux) concurrente d’Identify3D et de notre opérateur national Orange qui est leader dans ce domaine : c’est un élément-clé de ces process industriels. Il s’agit par exemple de permettre à un prestataire de faire un nombre limité d’impressions (voire une seule impression) en lui transmettant les fichiers de la géométrie de la pièce et du mode opératoire pour la machine qui réalise l’impression : il pourra n’être autorisé à fabriquer qu’une seule pièce. Autre élément-clé, Link3D est une solution de MES (c’est-à-dire gestion de la production) concurrente de 3YourMind, Authentise, 3dTrust… La gestion de la production devient extrêmement complexe dès qu’il y a plusieurs machines. Il y a des temps d’attente, il faut préparer les pièces avant, les détacher du plateau en fin de production, les sabler, préparer les finitions, mettre les pièces à cuire dans des fours pour obtenir les bonnes caractéristiques mécaniques, etc. Dassault Systèmes a fait l’acquisition en 2013 de la société Apriso, c’est devenu le nom de leur solution capable de gérer des sites avec différentes localisations géographiques et d’optimiser l’ensemble des tâches nécessaires et séquentielles du processus de production. 3YourMind s’intègre avec les ERP. Ce logiciel s’insère dans les logiciels CAO et 3YourMind propose les différents prestataires capables de fabriquer la pièce.
Les structures lattices, spécialité de nTopology
Il y a de plus en plus de logiciels qui proposent des structures lattices qui sont des empilements de microstructures constitués de petites barres cylindriques. L’ensemble de la pièce est sous forme de grille ou treillis à l’intérieur de la pièce, avec pour but l’allégement maximal pour une structure très solide. Les sociétés très actives sont Materialise, Siemens, 3DS. L’américain nTopology se focalise sur la création de lattices, conçoit ces structures avec des calculs très sophistiqués nécessitant de grosses puissances de calcul et les envoie à d’autres logiciels pour la construction de pièces comme Catia, Siemens. Le problème des lattices, c’est la taille des modèles. Un CAO classique peut faire 1 000 à 2 000 éléments, mais pas 100 000. Il faut avoir codé une structure de données particulières pour être efficace, et c’est ce que fait particulièrement bien nTopology.
Positionner intelligemment les pièces sur le plateau avec Etteplan
Cette société d’engineering, basée en Finlande, propose le moyen de faire un maximum de pièces sur un plateau avec des supports qui s’enlèvent facilement, presque à la main. On prend la même pièce dupliquée en X et Y, mais aussi en Z. On peut ainsi augmenter le nombre de pièces que l’on veut imprimer. Peu ou pas de support – il faut du savoir-faire ! – ou alors des supports très faciles à enlever, ce qui fait gagner énormément de temps, l’enlèvement des supports et la finition des pièces pouvant être des activités délicates et très chronophages, qui coûtent très cher : le parachèvement, c’est souvent 50 % du prix de la pièce métallique en impression 3D. Notons aussi la tendance à augmenter la puissance d’un laser (ainsi, en une passe, on saute d’une impression de 30 microns à 90 microns, donc on fait moins de tranches, on peut aller beaucoup plus vite). Prenons exemple d’une pièce métal de 200 mm de haut qui peut prendre à titre indicatif 40 heures en SLM : la méthode indiquée permet de gagner 60 % de temps.

Construction : 3 jours et 3 heures.
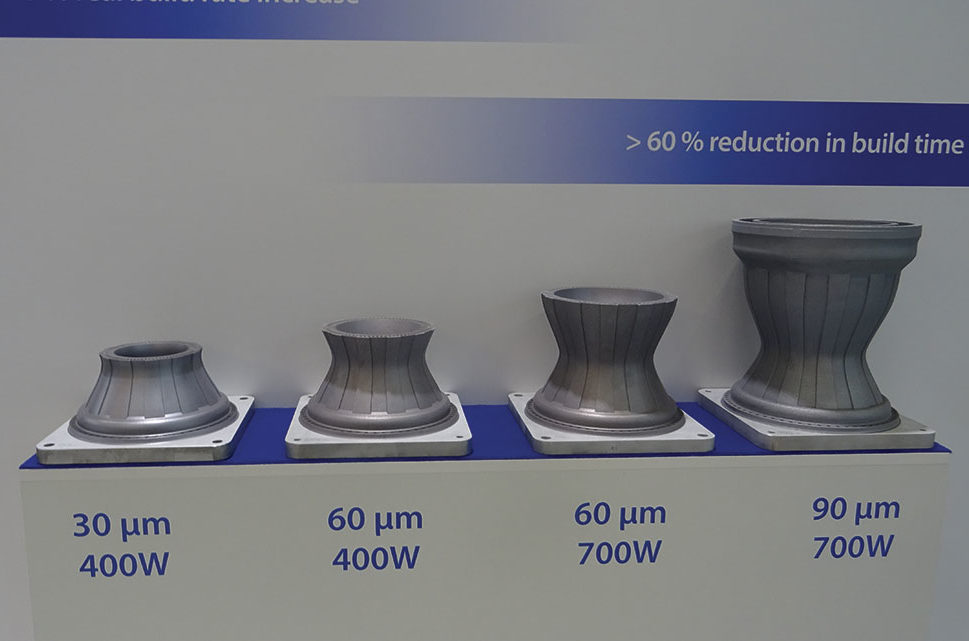
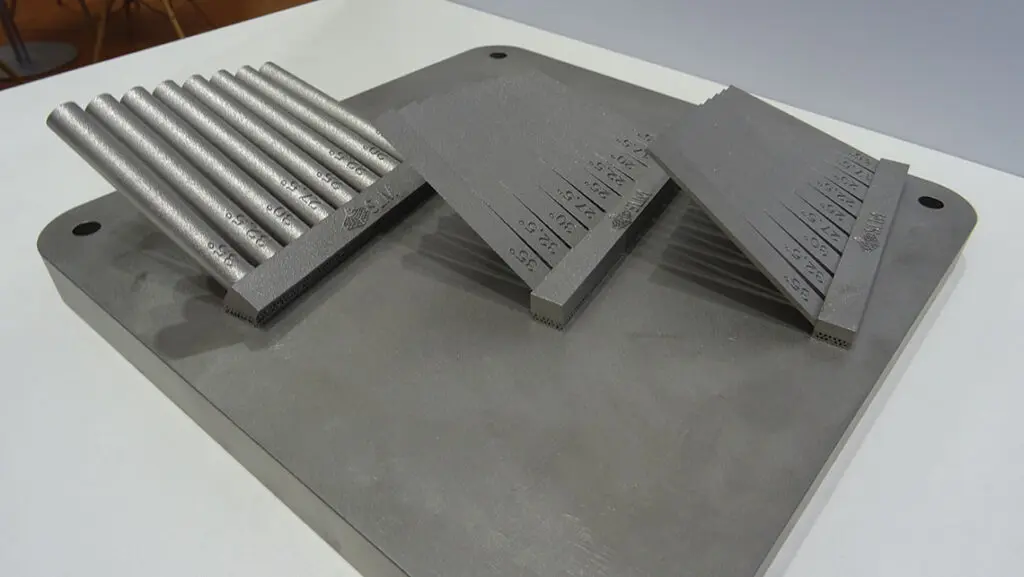
L’impression de fil métal
La promenade le long des allées révèle des objets extraordinaires, parfois très imposants – notamment en matériaux plastiques ou composites – comme la carrosserie d’une voiture, mais aussi en métal avec nombre de bras robotisés qui impriment à partir de bobines de filament des objets de grande taille de plusieurs mètres de long. Par exemple, la technologie Gefertec est fondée sur le procédé WAAM du soudage à l’arc, associé à une cinématique 3 ou 5 axes : une buse guide un fil métallique qui est fusionné et déposé par un arc électrique sur un substrat, avec une haute qualité métallurgique. L’utilisation de fil bon marché comme matériau de base ainsi qu’un faible coût d’outillage offrent aux utilisateurs une technologie très attractive en ce qui concerne le coût de fabrication. En utilisant ce type de procédé, Naval Group a imprimé une pale d’hélice de sous-marin. Creuse, l’hélice est ainsi plus légère et permettra de tester différents matériaux absorbants pour améliorer la discrétion du bâtiment.
Les matériaux
Venons-en enfin aux fabricants de matériaux. Ils sont tous présents, il y a les fabricants très spécialisés ou les géants connus comme BASF, moins connus comme Covestro. Mentionnons les acteurs français :
Aubert & Duval, les poudres métalliques
Fournisseur de poudres métalliques, il présente une nouvelle gamme de matériaux haute performance pour des machines laser-lit de poudre comme EOS, SLM Solutions, AddUp, etc. : des alliages base nickel destinés à un usage à haute température jusqu’à 900 °C, résistant à l’oxydation, pour des applications telles que les moteurs spatiaux, les turbines aéronautiques et à gaz et la compétition automobile ; des poudres acier inoxydable en 316L et 17–4PH pour usages médicaux, industriels et du luxe, Aubert & Duval a développé un procédé unique qui permet d’obtenir une très grande propreté des poudres produites sur les plus grands atomiseurs du monde avec une charge de plus de 10 tonnes ; ainsi que des poudres de titane, pour usages aérospatiaux et médicaux.
“Des moulages
par injection pour les chaussures d’Usain Bolt.”
Arkema décline une infinité d’applications
Chimiste de spécialité, spécialiste de matériaux avancés, Arkema a développé des applications de produits en impression 3D pour accompagner les secteurs-clients de longue date comme l’aéronautique et le sport. C’est aujourd’hui toute une palette de produits qui concerne, outre les 2 secteurs nommés, le dentaire, le médical, l’automobile. Arkema développe une gamme de produits qui couvre les principales technologies d’impression 3D et s’appuie sur des partenariats avec des leaders de la fabrication de machines comme HP, EOS, Prodways ou Carbon. Citons le Kepstan® PEKK, qui est un polymère qui tient les hautes températures (260 °C) pour les applications aéronautiques. Arkema développe avec ses partenaires des filaments et des poudres de PEKK chargés, ce qui permet l’impression de pièces renforcées très résistantes et légères particulièrement adaptées aux contraintes aéronautiques. Citons encore les résines photoréticulables (utilisées par exemple par les machines Prodways en bijouterie ou en dentisterie). Ce sont ces mêmes résines qui sont utilisées avec la machine Carbon pour la fabrication annuelle de dizaines de milliers de semelles de chaussure de sport. Un marché qu’Arkema connaît bien puisque son thermoplastique élastomère phare Pebax® est utilisé depuis des années en moulages par injection pour les chaussures d’Usain Bolt. Le Pebax® justement, ce matériau à mémoire de forme, est maintenant disponible pour l’impression 3D sous forme de filament ou de poudre. Sa légèreté et son élasticité uniques attirent l’attention des secteurs du sport et de l’électronique où Arkema est très présent, par exemple dans les écrans de téléphone – avec les polymères électroactifs de Piezotech – ou dans les batteries. Arkema est le seul chimiste au monde à produire du Polyamide 11, un matériau qui possède une ductilité et une résistance aux chocs uniques dans le monde de l’impression 3D. Ce matériau est utilisé par la société anglaise HEXR qui fait des casques de vélo sur mesure très solides, légers, avec beaucoup d’aération… BMW propose dans la nouvelle version des Mini le programme Mini Yours : chaque client peut personnaliser la planche de tableau de bord qui fait face au passager, toujours en PA11, seul matériau qui tenait les très hautes exigences de sécurité, en cas d’accident, car la planche de bord doit résister au choc du passager et ne pas éclater.
Erpro établit un record avec les brosses de mascara Chanel
Biosourcé (d’origine végétale), le PA11 est un matériau vendu sous la marque Rilsan®. L’une des utilisations remarquables de ce Rilsan est faite par la société Erpro, un fabricant français de pièces qui utilise différentes machines d’impression 3D et de multiples matériaux. Pour Chanel, Erpro a réussi à imprimer sur des machines EOS une brosse de mascara en Rilsan® PA11 à la fois flexible et très résistant, qui permet de déposer le mascara sur les cils d’une façon homogène sans avoir à recharger la brosse : « Le Volume Révolution de Chanel ». À cette occasion, Erpro a établi un record du nombre de pièces en fabrication additive, en imprimant un million de brosses par mois, avec une production en mai 2020 de 18 millions de brosses. Gageons que ce n’est qu’un début…
Références
- L’impression 3D : Porte d’entrée dans l’industrie du 21e siècle, Joël Rosenberg, Pascal Morand, Dominique Turcq, septembre 2015 – CCI Paris-IdF & CGARm & Institut Boostzone – téléchargeable gratuitement sur internet : https://www.cci-paris-idf.fr/sites/default/files/etudes/pdf/documents/impression-3d-etude-1509.pdf
- Fabrication additive, Claude Barlier, Alain Bernard, Dunod, avril 2016.
- L’impression 3D et le droit d’auteur, CSPLA, juin 2016.
- Futur de la fabrication additive, DGE, CGET, Pipame, janvier 2017.
- Wohlers Report 2020.