La batterie, composant clé de l’électromobilité
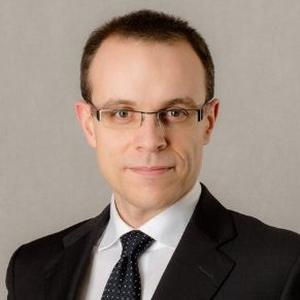
Quels sont les progrès réalisés et envisageables pour les batteries équipant les véhicules électriques ? L’Europe n’a‑t-elle pas une carte à jouer au moment où la technologie va connaître une rupture générationnelle ?
Les batteries lithium-ion sont devenues l’un des composants essentiels de l’électromobilité : stratégiques aussi bien pour l’industrie de par les barrières à l’entrée en termes de technologie (sécurité, performances) et de fabrication (qualité, coûts et effets d’échelle) que pour les États de par les enjeux d’indépendance technologique, d’emploi et d’impacts sur l’environnement. Le leadership est aujourd’hui en Asie : LG Chem, Samsung et SK Innovation (Corée), Panasonic (Japon) et CATL, BYD… (Chine). Le monde occidental compte quelques exceptions : Tesla aux États-Unis, et en Europe Saft (propriété du Groupe Total), ACC Automotive Cells Company (la coentreprise Stellantis-Total) et quelques nouveaux acteurs comme Northvolt.
L’enjeu technologique
Loin d’être une commodité, une batterie lithium-ion est un concentré de technologie s’appuyant sur la chimie du solide, la chimie organique, l’électrotechnique, la thermique et la mécanique, et elle incorpore de plus en plus de logiciels, d’algorithmes et de big data. La performance principalement attendue pour la mobilité électrique est l’autonomie et se décline au niveau de la batterie en objectifs de densité massique (Wh/kg) et de densité volumique (Wh/l). La densité massique affecte la consommation du véhicule (Wh/km) et est typiquement comprise entre 120 et 200 Wh/km (fonction du poids total du véhicule incluant la batterie et du profil d’usage routier).
La densité volumique affecte la capacité maximale d’énergie embarquée par le véhicule, typiquement entre 20 kWh et 100 kWh. Grâce à une amélioration de 5 % à 10 % par an en moyenne depuis trente ans, l’énergie embarquée à volume constant a été doublée ces dix dernières années, portant l’autonomie pratique d’une citadine de 120 à 300 km et pour les grandes berlines haut de gamme de 250 à 500 km. Si la densité est le paramètre le plus visible, les défis technologiques portent tout autant sur la sécurité (norme type UL ou ISO), la durée de vie (cyclique et calendaire) et la recharge rapide.
REPÈRES
Les importantes réductions de coût des batteries sur la période 2010–2018, environ ‑85 %, ont permis un essor des ventes mondiales de véhicules électriques, soit 2,6 % du marché en 2020. Pour autant la batterie représente encore 30 % à 45 % de la structure de coût d’un véhicule électrique pur. De nouvelles réductions de coût seront donc nécessaires pour permettre une croissance significative des parts de marché de l’électrique, attendues entre 30 % et 50 % en 2030.
Vers le lithium-ion solid-state Gen4
Le Japon et l’Europe ont été les leaders sur les deux premières générations de 1991 à 2008 : le graphite / LCO (lithium cobalt oxide), puis le graphite / NCA (lithium nickel cobalt aluminium). À la faveur d’une ambitieuse politique de recherche et d’industrialisation construite dès le début des années 2000, portée par l’essor de l’électronique grand public (ordinateurs portables, smartphones) mais pensée pour l’avènement de la mobilité électrique, les Coréens et les Chinois ont pris le leadership mondial sur la troisième génération, dite « Gen3 ». Elle est constituée de deux familles chimiques : le graphite / NMC (lithium nickel manganèse cobalt) et le graphite / LFP (lithium fer phosphate).
L’essor de la Gen3 depuis 2010 a été permis par deux facteurs : d’une part l’amélioration continue des performances de densité d’énergie et de durée de vie et, d’autre part, la réduction des coûts via la massification des moyens de production des matériaux et des cellules lithium-ion. Cette génération technologique arrive dans une fin de cycle à l’horizon 2025–2030, nécessitant une rupture pour aller vers de plus hautes performances en densité, tout en offrant une sécurité plus facile à maîtriser.
“Le leadership est aujourd’hui en Asie.”
La technologie lithium-ion SSB Solid-State Batteries, actuellement en développement, offre ce double avantage. En remplaçant l’électrolyte liquide par un électrolyte solide apportant une résistance thermique accrue, elle permet une sécurité intrinsèque améliorée. Surtout elle autorise des densités d’énergie jusqu’à 75 % plus élevées (de 300 Wh/kg aujourd’hui à 400–420 Wh/kg en 2025–2030, voire 500 Wh/kg à long terme), via l’utilisation d’une anode en lithium-métal pur et de nouvelles chimies de cathode, auparavant inaccessibles car inadaptées aux électrolytes organiques.
Différentes possibilités d’électrolyte solide existent, comme les polymères, les sulfures et les céramiques oxides. Tous sont encore à des niveaux de maturité technologique bas et la technologie solid-state n’arrivera que progressivement sur le marché, d’abord dans des applications d’électronique grand public ou des niches industrielles à haute valeur ajoutée (espace, défense) entre 2023 et 2028, avant de s’introduire progressivement dans la mobilité entre 2026 et 2030. La part de marché globale pourrait être de 15 % à 30 % à l’horizon 2030.
Le lithium-ion
La technologie lithium-ion repose sur la migration des ions lithium entre l’anode (la borne négative, en graphite) et la cathode (la borne positive, constituée d’un composé lithié, oxyde ou phosphate, à base de nickel, de manganèse, de cobalt ou de fer). Les trois premières générations utilisent un électrolyte liquide organique, mélangé avec des sels de lithium, qui imprègne les matériaux actifs de la cellule et permet la migration des ions lithium. Ce couple électrolyte / sels présente un double défi. De vieillissement : il se dégrade avec le temps et l’usage de la batterie, diminuant à la fois l’efficacité et l’énergie utile disponible. De sécurité : en cas de court-circuit interne ou d’incident, il est instable thermiquement et peut, s’il se décompose, produire des gaz toxiques comme le monoxyde de carbone.
Un enjeu industriel et économique
La capacité de production mondiale de lithium-ion a massivement crû dans les dix dernières années, tirée par le marché automobile et par le stockage stationnaire. En ordre de grandeur, une batterie de smartphone représente environ 10 Wh, soit pour 350 millions d’unités vendues annuellement un total de 3,5 GWh. Pour égaler le marché mondial des batteries de smartphones, seul 70 000 véhicules électriques dotés d’une batterie de 50 kWh suffisent (0,001 % du marché automobile). Ainsi, de 30 GWh par an en 2010, la capacité est passée à 100 GWh par an en 2015 (+ 27 %/an), puis 540 GWh par an en 2020 (+ 40 % par an). Elle pourrait atteindre plus de 2 000 GWh par an dès 2025.
Cette croissance, mobilisant de lourds investissements, environ un milliard d’euros pour une gigafactory de 10 GWh par an, a permis une décroissance des coûts supérieure à 10 % par an et une croissance des volumes supérieure à 20 % par an. Cette évolution pose de nombreux défis aux industriels : augmentation constante de la taille critique minimale, amortissement des investissements passés, croissance continue et pression sur les coûts fixes pour maintenir une rentabilité minimale. Un schéma similaire à celui de l’industrie des semi-conducteurs ou des panneaux solaires, avec la disparition dans les années 2013–2018 de nombreux acteurs de deuxième et troisième rang.
“L’émergence à l’horizon 2025–2030 de la 4e génération de batteries lithium-ion.”
La concentration de l’industrie des batteries lithium-ion en Asie pose des enjeux de souveraineté et d’emploi, en particulier pour les constructeurs d’automobiles occidentaux qui se convertissent progressivement à l’électricité sous l’impulsion des politiques environnementales et l’intérêt croissant des consommateurs. Volkswagen consacre ainsi, sur un total de 44 milliards d’investissements sur 2019–2023, 30 milliards d’euros à la mobilité électrique, aussi bien dans la recherche que dans la transformation de son outil industriel. Les chaînes de fabrication de batteries automobiles et de conversion-transmission électrique sont différentes et beaucoup moins intenses en main‑d’œuvre que leurs équivalentes thermiques.
La combinaison d’une disparition de ces usines et du manque de compétences dans l’électrique fait peser une menace importante sur les 13 millions de personnes employées dans l’industrie automobile européenne, particulièrement en Allemagne et en France. Des objectifs de localisation dans la fabrication et l’assemblage permettraient de répondre aux besoins de maintien du savoir-faire, de synergies entre le développement produit et la production, et de sauvegarde des emplois.
Un objectif environnemental et éthique
L’automobile a besoin de chaînes d’approvisionnement résistantes et frugales (énergie, CO2, coûts), en particulier pour les batteries dont le poids (coût logistique) et les enjeux éthiques (origine et extraction des métaux, en particulier le cobalt) poussent à une localisation la plus poussée possible. Une feuille de route marché incitative et contraignante, au regard de l’origine des matières premières, de l’empreinte CO2 cradle-to-grave, du taux de recyclage minimum (en boucle ouverte et en boucle fermée), du contenu maximum sur certains métaux, pourrait être requise pour permettre une durabilité de la filière ou au minimum favoriser les acteurs européens mobilisés sur ces sujets environnementaux.
Un avenir riche de possibilités
L’innovation dans les batteries lithium-ion pour la mobilité électrique ouvre par ailleurs de nouveaux sujets de réflexion, comme l’émergence d’utilisations complémentaires de la batterie (le véhicule électrique assure par exemple une fonction de stockage au profit du réseau, vehicle-to-grid, ou de l’habitation, vehicle-to-home), la possibilité d’application en seconde de vie, mais aussi comme les synergies avec de larges marchés connexes en croissance forte comme le stockage stationnaire des énergies renouvelables et la mobilité industrielle (ferroviaire, aviation, véhicules industriels), dont l’électrification est tout aussi importante pour la décarbonation de l’économie.
Une fenêtre d’opportunité existe donc avec l’émergence à l’horizon 2025–2030 de la 4e génération de batteries lithium-ion, dite SSB Solid-State Batteries. Si la course technologique est déjà lancée, les jeux ne sont pas faits, laissant à l’Europe une occasion unique de se repositionner, à condition d’actionner simultanément trois leviers : une feuille de route technologique ambitieuse ; une politique industrielle volontaire ; et enfin des normes marché contraignantes, à même de répondre aux défis environnementaux et éthiques. L’Europe a déjà su dérouler avec succès une telle stratégie sur d’autres sujets clés, comme la réduction des émissions de CO2 des moteurs thermiques ou les lanceurs spatiaux Ariane.
Commentaire
Ajouter un commentaire
Une question plutôt sur les super condensateurs, quelles sont les perspectives dans ce domaine ?
J’avais retenu leur capacité de charge immédiate qui pourrait améliorer la récupération d’énergie au freinage par exemple.