La fabrication additive dans le domaine naval


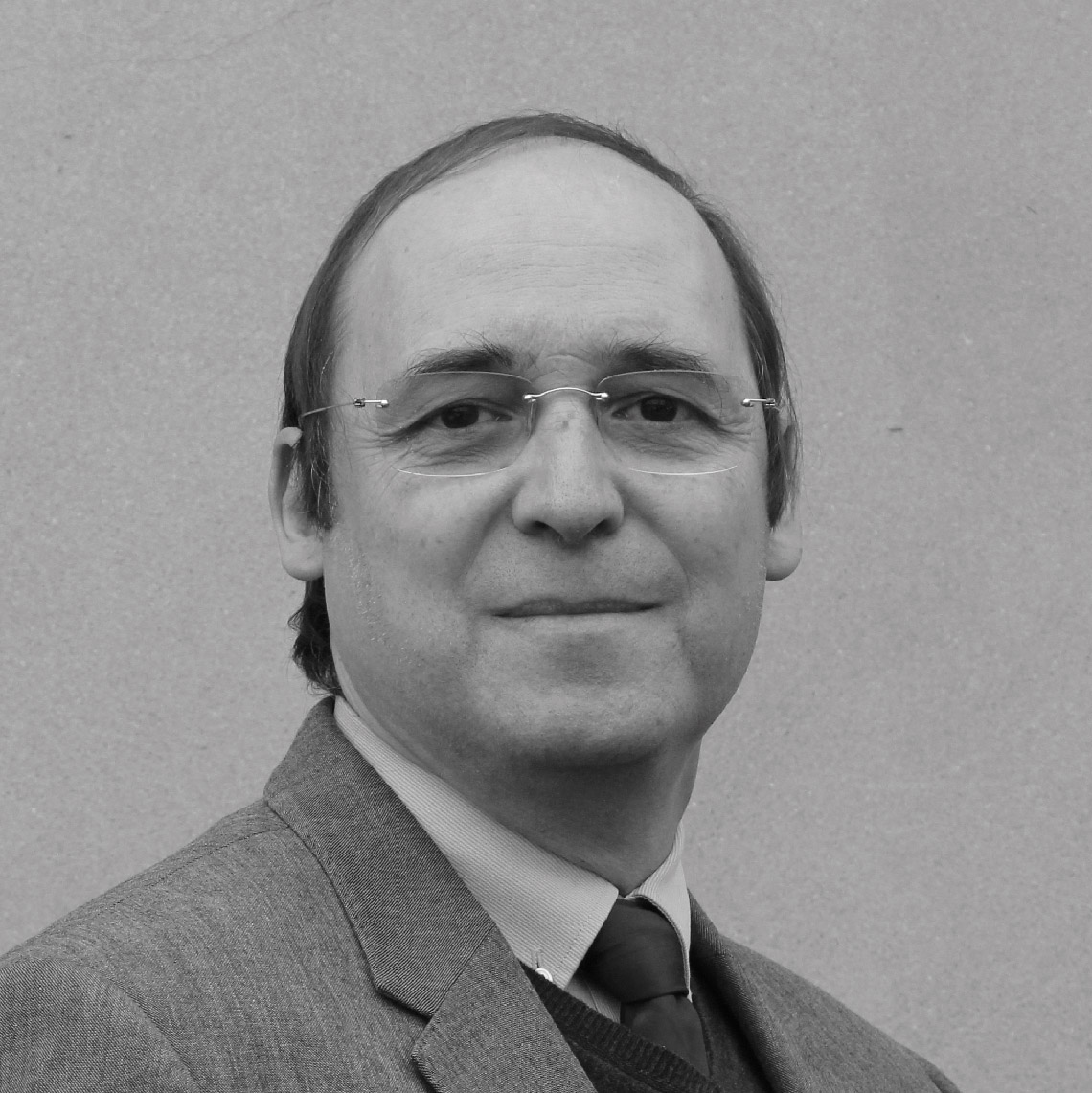

Naval Group introduit les nouvelles technologies de fabrication additive sur l’ensemble de ses sites de production. Cet exemple particulier illustre pour le domaine naval, au travers de multiples cas, la capacité de mettre en œuvre des concepts innovants grâce à un procédé de fabrication additive et une chaîne numérique maîtrisée de la conception à la fabrication.
La fabrication additive est désormais une réalité industrielle à Naval Group en tenant compte des spécificités de son domaine (équipements de petites à très grandes dimensions, conditions d’utilisation sévères, effet de série limité et contraintes économiques fortes). Un premier exercice d’identification des cas d’usage en fabrication additive a incité l’industriel à orienter ses efforts sur deux voies principales : d’une part l’amélioration de la disponibilité des navires grâce à la mise en place d’une offre complète de services depuis l’identification des cas jusqu’à la production de réparations ou de pièces de rechange conformes ; d’autre part l’amélioration des performances en service par une optimisation de conception rendue possible grâce aux possibilités offertes par les procédés de fabrication additive.
Pour répondre aux besoins de disponibilité des navires et apporter des solutions efficaces aux cas d’obsolescence en particulier, les différents sites de production de l’industriel s’organisent en réseau afin d’apporter des solutions à la chaîne de valeur complète pour la mise à disposition de solutions de réparation ou de pièces de rechange à fabriquer à quai ou à bord selon les cas. En outre, l’entreprise se dote d’équipements industriels différenciants pour la fabrication de produits de grandes dimensions, tels que les hélices de propulsion de navire, et il aborde en parallèle la démarche de qualification afin d’attester la conformité des pièces avant installation à bord.
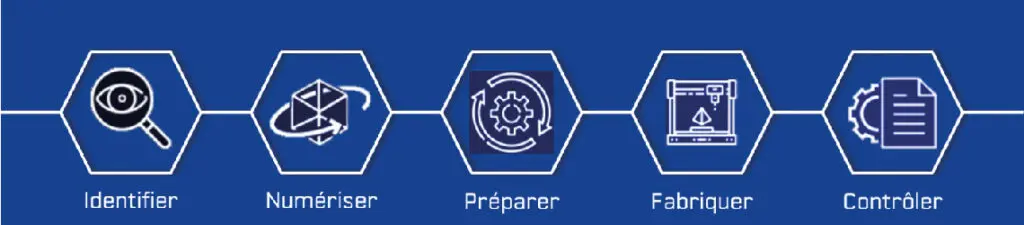
Des ambitions élevées pour la fabrication additive
Les besoins du groupe justifiant de recourir aux différentes solutions de fabrication additive sont multiples et variés ; des premiers cas de prototypage et d’outillage ont conduit les sites d’ingénierie et de production à s’équiper depuis plusieurs années, pour désormais offrir des solutions de réparation ou de rechange en maintenance, ainsi que des pièces à géométrie extrêmement complexe pour l’amélioration des performances ou la réduction de l’encombrement en construction neuve. Le groupe s’appuie désormais sur des compétences et moyens complémentaires, organisés en réseau autour d’une expertise développée par sa direction de l’innovation et de l’expertise technologique à partir des premiers projets de R & D lancés depuis une décennie. Une première expérimentation de fabrication additive embarquée a été proposée dès 2018 à bord du bâtiment de projection et de commandement (BPC) Dixmude. L’objectif était de mieux appréhender les besoins des équipages et d’expérimenter des impressions 3D à distance de pièces d’équipement opérationnel. Au-delà de l’appropriation de cette nouvelle technologie par les marins, cette première expérience a fourni une première liste de cas de rechange en mission.
Ainsi, pour répondre aux besoins opérationnels de ses clients, l’industriel met en place une nouvelle offre de services, depuis l’identification du besoin jusqu’à la livraison d’une pièce avec acceptation de sa conformité, à partir de moyens d’impression organique installés à bord des navires. Le principe consiste à fournir une pièce de rechange imprimée à partir d’une bibliothèque de fichiers de modèles 3D de référence (voire d’un scanner 3D pour modéliser la pièce à remplacer). Le simple fait de disposer d’un moyen d’impression 3D ne suffit pas à accéder rapidement et en sécurité à la fabrication de pièces fonctionnelles et de qualité. La solution comporte donc plusieurs étapes d’accompagnement et d’aide à la décision ; elle s’appuie sur une interface construite à partir de plusieurs algorithmes et une hotline technique et elle croise l’expérience acquise sur les procédés de fabrication additive et la compétence d’architecte-systémier-intégrateur de navires. Une dernière étape consiste à apporter la preuve de la conformité par une série de tests à bord ou à quai selon la criticité de l’usage.
“Une première expérimentation de fabrication additive embarquée.”
De plus, les conditions d’utilisation sévères des navires militaires justifient de répondre à des exigences fortes pour la fabrication des équipements et systèmes qui les constituent. Les pièces réalisées par fabrication additive doivent donc répondre à des règles spécifiquement adaptées pour ces nouveaux procédés. En l’absence de normes applicables dans le domaine, une démarche de qualification est entreprise au sein du groupe, avec l’appui de partenaires comme le Bureau Veritas, afin d’apporter la justification nécessaire à l’introduction de pièces critiques à bord dans un avenir proche de deux ans. Sur le fondement d’un socle solide, Naval Group ambitionne finalement une utilisation intense des différents procédés de fabrication additive au profit des grands programmes nationaux et export à venir (sous-marins et bâtiments de surface).
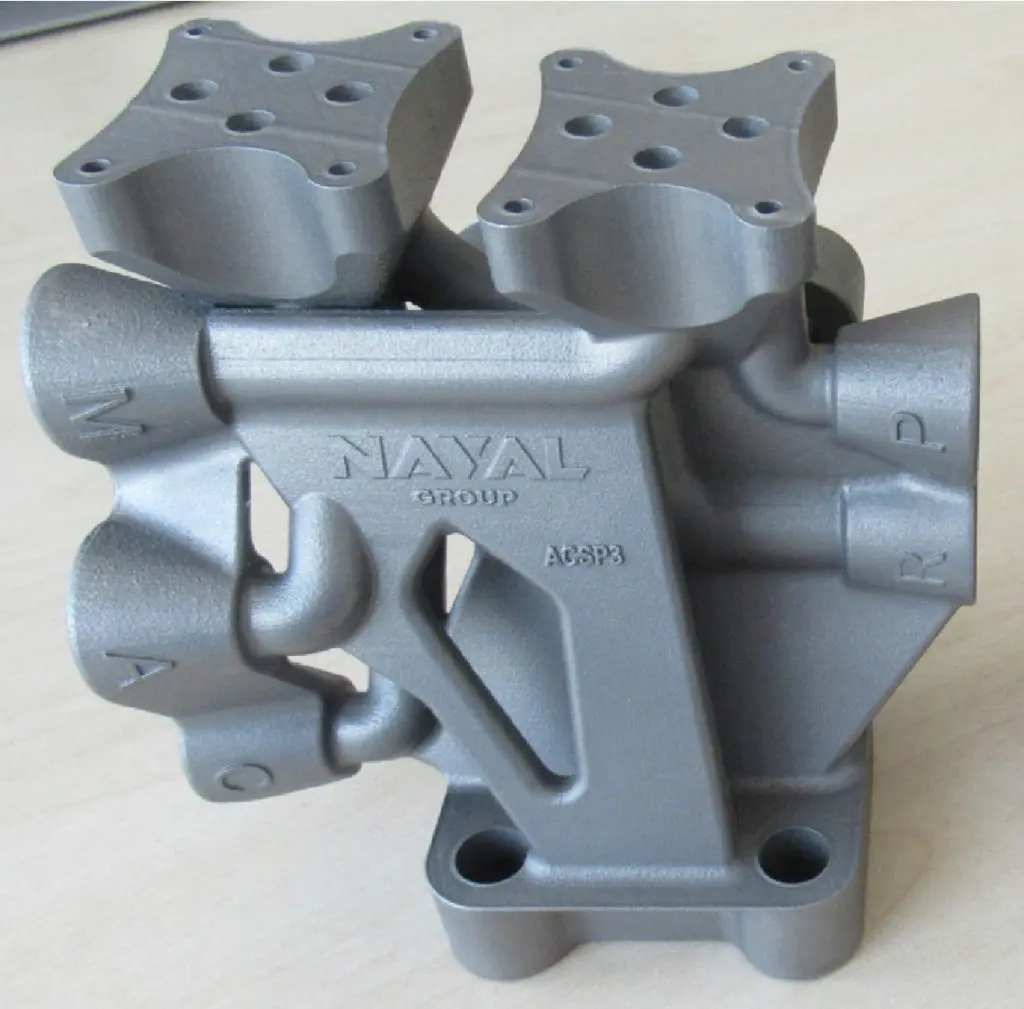
De premières réalisations emblématiques
Les travaux engagés depuis 2015 sur le procédé de dépôt de fil métallique ou WAAM (Wire Arc Additive Manufacturing) ont rapidement confirmé l’intérêt d’une telle solution comme remplacement crédible aux procédés conventionnels pour la fourniture d’ébauches de pièces complexes de grandes dimensions. En effet, les premières réalisations du Joint Laboratory of Marine Technology (JLMT), laboratoire commun entre l’École centrale Nantes et Naval Group, ont démontré la capacité du procédé à offrir des performances « matériau » au moins égales, voire supérieures, à celles connues pour la fonderie dans des délais de fabrication compatibles avec les enjeux industriels. Ce type de procédé agile apporte de surcroît une liberté de conception en permettant de placer la quantité de matière juste nécessaire à l’endroit où elle est requise.
Ainsi, sur la base d’une conception optimisée, un premier démonstrateur de pale creuse en acier austéno-ferritique a été réalisé au sein du JLMT dans le cadre du projet européen H2020 RAMSSES (Realisation and Demonstration of Advanced Material Solutions for Sustainable and Efficient Ships), financé par la Commission européenne. Les gains de performance associés pour ce cas d’étude sont significatifs : réduction de la masse de la pale de 50 % et amélioration du rendement propulsif de l’ordre de 5 %, offrant également la possibilité d’une signature acoustique réduite et personnalisée. Dès lors, forte de cette première expérience prometteuse, l’entreprise s’est dotée d’un moyen industriel d’envergure sur son site de production de Nantes-Indret, dans le but de fournir des ébauches pour ses équipements. En premier lieu, des pales d’hélice ont été réalisées en série pour une expérimentation à la mer sur un bâtiment militaire, prévue à l’été 2020. Des commandes sont déjà prises pour de prochains programmes et les études de R & D continuent en parallèle sur des moyens équivalents pour apporter les solutions innovantes de demain, qui permettront aussi de s’affranchir des difficultés d’obtention d’ébauches moulées ou forgées de qualité.
Par ailleurs, les procédés de type fusion sur lit de poudre métallique ou Laser Beam Melting (LBM) apportent des solutions nouvelles pour la fabrication de composants de géométrie complexe inaccessible par des procédés conventionnels. Le site d’Angoulême-Ruelle, qui s’équipe d’un moyen industriel pour la fabrication additive métallique, propose par exemple des solutions d’allègement significatives pour des distributeurs hydrauliques (réduction de 80 % de la masse par rapport à une pièce usinée) à partir d’une reconception adaptée au procédé de fabrication additive. Ainsi, une pièce de rechange a été réalisée pour équiper un système d’armes lors d’une opération de maintenance d’un navire militaire. Les différents essais sur témoins et sur la pièce concernée ont validé son usage à bord.
“Un démonstrateur de pale creuse a été réalisé à Nantes.”
Un nouveau modèle de service
Le domaine des usages de la fabrication additive est vaste et les investissements en recherche et développement se renforcent pour identifier les très grandes possibilités offertes. Mais, en parallèle, l’industrialisation au profit du naval de défense est en cours, la qualification est déjà acquise pour des premiers cas d’usage. Un nouveau modèle de service est également proposé pour apporter des solutions au plus proche des besoins des marins, en conciliant approche innovante et sécurisation de la démarche. Avec l’hélice de propulsion de navire et le distributeur hydraulique pour système d’armes, deux pièces à fortes contraintes mécaniques et d’usage réalisées en fabrication additive et montées à bord de navires militaires en 2020, Naval Group change de rythme sur la fabrication additive et dispose donc d’une solution agile différenciante dans sa boîte à outils industrielle, au profit de la disponibilité des navires et de l’amélioration de leurs performances.
Références
Evaluation of wire arc additive manufacturing for large-sized components in naval applications, Queguineur (A.), Rückert (G.), Cortial (F.), Hascoët (J.-Y.), Welding in the World, Springer, December 2017.
On the benefits of metallic additive manufacturing for propellers, Muller (P.), Rückert (G.), Vinot (P.), Sixth International Symposium on Marine Propulsors (smp’19), Rome, Italy, May 2019.