L’approche LEAN appliquée au développement des produits
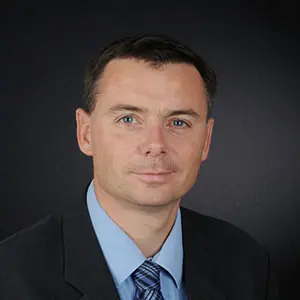
REPÈRES
Lean (« dégraissé ») est une méthode de gestion de production » sans gaspillage « , mise au point au Japon par Toyota. Elle recherche la performance par l’élimination des gaspillages : production excessive, attentes, transports inutiles, stocks, etc., classés en sept catégories.
Pourquoi appliquer la méthode lean aux activités de développement et d’ingénierie ?
Une statistique bien connue et unanimement acceptée suffit à poser clairement les enjeux d’un développement maîtrisé et réellement efficace : 70 % à 80 % des coûts de cycle de vie d’un produit sont déterminés en fin de phase de conception, alors que seuls 10% à 30% des coûts ont été réellement engagés.
La culture du pompier
Quelle situation observons-nous dans nos entreprises ? Des projets en dépassement de délai, dont les calendriers ont été imposés « par décision du management « , sous la pression forte des marchés ou des clients. Un dialogue de plus en plus difficile entre l’encadrement et les équipes d’ingénieurs et de techniciens, restreint bien souvent aux éléments de gestion.
Créer les rituels de management
Quelles réunions, quelle durée, avec quels participants, à quelle fréquence ? Ces rituels garantiront que les informations sont effectivement à jour et exploitées. L’idée est de privilégier les réunions courtes (15 à 45 minutes) et fréquentes (hebdomadaire à quotidienne, selon la phase du projet). Le gain se situe dans un partage beaucoup plus efficace des informations et donc une meilleure anticipation ou une plus grande réactivité en cas d’imprévu.
Une communication essentiellement fondée sur les outils de messagerie électronique et sur les échanges écrits, laissant très peu de place à la communication visuelle et aux échanges physiques. La mise en avant de la culture du pompier, celui qui a réussi, pour se dépêtrer d’une situation inextricable et fortement compromise, à trouver la solution par son inventivité et sa débrouillardise.
Des processus de travail à la complexité grandissante, parce que la complexité des produits et des organisations est elle-même grandissante. Enfin, des impasses techniques nombreuses, les décisions étant prises bien souvent au plus tôt, au plus vite – n’est-ce pas plus rassurant ? -, sur des bases techniques non explicitement validées. Face à cette situation, les propositions faites au titre de l’approche dite lean product development peuvent être regroupées en trois grandes familles de principes, sous-tendues par différentes méthodes et différents outils.
Éliminer toute forme de gaspillage
Éviter les remises en question
Est-il raisonnable de vouloir prendre plus de temps dans les phases amont, alors que l’on est systématiquement en retard ? Il faut comprendre que l’on ira d’autant plus vite en conception détaillée que l’on aura fait les bons choix en conception générale. On évitera les remises en question, toujours très coûteuses, dans les phases aval du développement, de l’industrialisation et de la mise en production.
Il est possible de transposer au monde du développement les bien connues sept formes de gaspillage énumérées en lean manufacturing. Le principe est alors, pour un processus donné, de repenser ce processus sous une forme plus simple, avec les acteurs et les clients. Seulement 30% à 40% des temps passés par les équipes de développement le sont pour des tâches à valeur ajoutée. Les techniques de value stream mapping (cartographie de la chaîne de valeur) peuvent être utilisées, avec un succès certain. On observe habituellement un gain de l’ordre de 20 % à 30%.
Promouvoir le management visuel
La communication visuelle permet de percevoir 80% des informations présentées
Plus de 80 % des informations que nous retenons sont des informations que nous avons vues. Le lean product development encourage l’utilisation de techniques extrêmement visuelles pour accompagner la communication et la prise de décision. En pratique, cela passe par l’utilisation de standards de conception tels que les limit curves (courbes aux limites) ou trade off curves (courbes de sensibilité), sous forme de documents A3. Ces documents permettent de matérialiser très simplement les intervalles de solutions admissibles pour une application donnée et de positionner visuellement les arbitrages entre différents métiers. Cela passe également par la mise en place d’obeyas, espaces dédiés dans lesquels sont affichées et mises à jour régulièrement au cours des réunions les informations utiles à l’équipe projet.
Retarder les décisions
Un processus de développement, en particulier l’amont de ce processus (conception préliminaire), est une succession de choix et donc de décisions, plus qu’une séquence d’activités déterministes. L’une des clés pour éviter que ne soit remise en question la conception du produit est la qualité de la prise de décision. À quel moment telle décision doit-elle être prise, quels éléments objectifs justifient cette décision ? L’approche du lean product development suggère que les décisions soient prises le plus tard possible (mais pas trop tard) et insiste sur la qualité des justifications techniques.
Prendre les décisions le plus tard possible sur la base de connaissances validées
Très souvent, nous observons qu’au contraire nous allons prendre les décisions au plus tôt et fermer les portes dès que possible. Avons-nous à ce moment-là tous les éléments qui permettent de conclure, du point de vue tant de l’expression des besoins que des justifications techniques ? Ne peut-on pas prendre un peu plus de temps pour étudier plusieurs alternatives si effectivement une solution ne paraît pas évidente ? La difficulté sera de définir la séquence des décisions ou des choix, de déterminer clairement les interdépendances entre certains de ces choix, au besoin d’identifier les alternatives et de planifier en conséquence la séquence de décisions, de façon cohérente et synchrone entre les métiers – ce sont les méthodes dites set-based concurrent engineering.
Une réduction de 30% du cycle de développement
Qu’en est-il aujourd’hui du déploiement de ces méthodes ? Le lean product development n’a certainement pas atteint le même niveau de maturité que le lean manufacturing. Le secteur le plus avancé, proximité avec l’initiateur nippon de ces démarches oblige, est celui de l’automobile. Les entreprises du secteur hightech ont également avancé de façon significative dans ce domaine. Suivent l’aéronautique, le spatial, l’énergie et les équipements industriels. Les donneurs d’ordre du secteur automobile constatent aujourd’hui une réduction du cycle de développement de l’ordre de 30% pour un produit nouveau.
Deux difficultés
La complexité grandissante des organisations est probablement plus contraignante que celle des produits eux-mêmes. Les rachats, fusions et autres restructurations ont amené les entreprises à adopter des organisations très souvent peu lisibles et extrêmement changeantes, induisant une perte de repères. On peut imaginer des organisations conservant un niveau suffisant de lisibilité et privilégiant la proximité et la réactivité. Les unités élémentaires de conception, comparables aux unités autonomes de production en lean manufacturing, apportent une réponse.
On peut aussi douter de notre aptitude à appliquer avec toute la discipline nécessaire les standards définis (produits, processus, méthodes). L’Europe, la France en particulier, peut-elle être comparée au Japon ? A minima, il est important de confier le soin de définir les standards à ceux qui devront les mettre en application.
Commentaire
Ajouter un commentaire
Executive VP – Europrop International
Bravo Stéphane pour cette synthèse de bonnes pratiques ! Certes les secteurs que tu cites ont tous généralisé le lean en développement (sans oublier le naval dans les années 1995–2000) mais les grands projets « phares » ont toujours autant de mal à être à l’heure. Il y a un contributeur majeur des dérapages de projets complexes, que nous appréhendons très mal, c’est l’instabilité des spécifications amont. C’est un fait, même quand il y a des phases de conception conjointe client-fournisseur, parce que les clients eux-mêmes ne vivent pas dans un environnement stable. On peut retarder des franchissements de jalons mais on risque fort de n’avoir jamais tous les éléments pour conclure… sauf à la fin. On a vu des produits complexes certifiés bons pour le service alors que leurs spécifications continuaient à évoluer en profondeur. Comment intégrer cette réalité en développant « à risque objectif » ? A te lire ! Vincent Ginabat (90)