L’innovation au cœur de l’action dans la construction navale
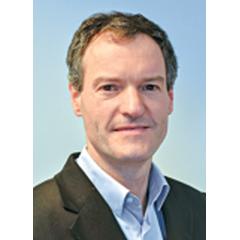
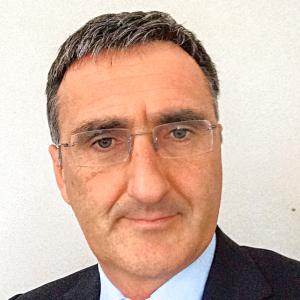
Pour améliorer la performance des navires qu’elle construit, STX France a concentré ses efforts de R & D sur les thèmes identifiés comme les plus stratégiques :
- la profitabilité pour les armateurs et notamment la réduction de la facture énergétique des navires ;
- la prise en compte des nouvelles exigences environnementales induites par la réglementation et par une sensibilité du public (croisiéristes, riverains des ports, etc.) ;
- la sécurité des navires et de leurs passagers ;
- la compétitivité du chantier.
REPÈRES
Il faut prendre la mesure de la complexité d’un projet de conception et de fabrication d’un paquebot géant tel que l’Oasis III, le plus grand paquebot du monde. C’est l’équivalent d’une petite ville avec tous ses services associés, comme la production d’énergie (presque 100 MW), la production et la distribution d’eau, le traitement des déchets ; un casino, des salles de spectacle, des restaurants, un hôpital ; etc. Tout doit être conçu, fabriqué, assemblé et testé en 36 mois, de la signature du contrat à sa livraison à l’armateur.
Il faut pour cela mobiliser dans un temps très court plus de 450 ingénieurs et techniciens regroupés en plateau pendant 24 mois. Il faut ensuite faire intervenir sur le chantier de construction plus de 2 500 personnes couvrant une large palette de métiers, des soudeurs, charpentiers métalliques, mécaniciens, tuyauteurs, électriciens, peintres et agenceurs, aux ingénieurs en réseaux et télécommunications ou en système de contrôle-commande intégré, ou encore des spécialistes en acoustique et vibration, qui vérifieront au cours des essais que les performances définies au stade du projet sont atteintes. La construction de cette ville flottante exige une planification et une coordination précises et réactives.
Efficacité énergetique et environnementale
L’augmentation du prix des combustibles, associée à la mise en place de nouvelles réglementations limitant l’utilisation de fuel lourd bon marché mais hautement soufré donc polluant, a largement réduit la profitabilité des armements. La facture énergétique est devenue, pour les navires de croisière, le premier poste de dépenses.
“ Concentrer les efforts de R & D sur les thèmes les plus stratégiques ”
Anticipant le besoin de navires plus économes en carburant et plus respectueux de l’environnement, STX a lancé en 2007 son programme de R & D « Ecorizon ». Une équipe dédiée d’ingénieurs a pour mission de diviser par deux la consommation d’un paquebot d’ici 2020, par rapport à des navires mis en service en 2010, et de répondre aux exigences des nouveaux règlements environnementaux, notamment sur les fumées d’échappement.
À ce jour, la moitié du chemin est parcourue. STX peut afficher un gain de 25 %, notamment grâce à ses travaux sur la cogénération, la récupération de l’énergie thermique des moteurs, l’hydrodynamisme des carènes, l’efficacité des propulseurs, la production et la distribution de l’énergie électrique.
Pour la question des émissions polluantes, STX est aujourd’hui en mesure de proposer des solutions fiables, économiques et dépassant les exigences réglementaires grâce à ses travaux sur la propulsion au gaz naturel liquéfié et sur les technologies de capture du soufre dans les fumées (scrubber).
Optimisation des processus
Dans un contexte de concurrence internationale très forte, une autre composante essentielle du programme de R & D porte sur les processus d’études et de construction des navires. Nous mettons en œuvre un processus de « réalisation concourante » : pour tenir les délais très courts (36 mois en moyenne), la fabrication et le montage du navire sont démarrés alors que la totalité des études n’est pas terminée.
“ L’utilisation d’outils de simulation numérique s’est largement répandue ”
Pour ce faire, des solutions très innovantes d’ingénierie-PLM (product life-cycle management) sont mises au point, reposant sur l’interfaçage très étroit entre outils de CAO et ERP (enterprise resource planning) autour d’une maquette numérique unique.
L’utilisation d’outils de simulation numérique s’est largement répandue, que ce soit dans le domaine des calculs pour optimiser l’hydrodynamisme des carènes ou dans celui de la réalité virtuelle grâce au soutien de l’association Clarté de Laval (par exemple pour la simulation de l’accessibilité d’un équipement dans une zone du navire particulièrement dense).
Cela permet d’améliorer la qualité des études et d’éviter les modifications ultérieures, sources de surcoût.
Un robot intelligent
L’utilisation d’outils de simulation numérique s’est largement répandue.
Les procédés de fabrication font également l’objet d’une activité de R & D et d’optimisation soutenue. Le projet « Charman », par exemple, consiste à développer un robot de soudage de coque (bordé) en collaboration avec l’Institut de recherche technologique Jules-Verne de Nantes. Il s’agit d’un robot capable de se mouvoir sur un bordé vertical pour réaliser la jonction de deux blocs de navire.
Ce robot aura toute l’« intelligence » nécessaire pour suivre la bonne trajectoire et adapter son cordon de soudage à la géométrie des tôles à souder. C’est un exemple significatif d’accroissement de la productivité (plus besoin des échafaudages nécessaires au soudage manuel) mais aussi de la sécurité des opérateurs (plus de travaux en hauteur).
En 2014, nous avons également mis en service une nouvelle unité de fabrication : l’unité d’armement des panneaux (UAP). Elle a permis d’atteindre, pour l’Oasis III, un taux de préarmement des panneaux et des blocs (tuyaux, gaines de ventilation, chemins de câbles, etc.) inégalé jusqu’à présent, avant leur assemblage dans la cale. Les gains de productivité sont significatifs.
Ces mêmes blocs sont peints et équipés de leurs balcons dans des abris mis en place sur l’aire de prémontage : on s’affranchit ainsi des aléas météo, tout en améliorant la qualité.
Enfin, le nouveau portique, d’une capacité de 1 400 tonnes, permet de construire des blocs plus lourds et plus volumineux, d’où une réduction du nombre de blocs et de la durée d’assemblage des navires.
Les énergies marines
Le chantier naval de Saint-Nazaire, son environnement industriel, les compétences en matière d’ingénierie et de fabrication qui s’y trouvent constituent un excellent terreau pour le développement de nouvelles activités industrielles en mer.
C’est pourquoi STX France s’est naturellement tourné depuis quelques années vers l’une de ces activités en fort développement : les énergies marines. À titre d’exemple, deux modules offshore ont été réalisés en 2014 à Saint-Nazaire.
Le premier est destiné aux marchés des énergies marines renouvelables : il s’agit d’une station électrique (topside, fondation jacket et piles) d’une puissance de 210 MW, élevant le courant d’une tension de 33 kV en provenance des éoliennes à une tension de 132 kV pour pouvoir l’exporter vers la terre.
Cette station électrique est aujourd’hui en opération en Grande-Bretagne dans le parc éolien offshore de Westernmost Rough. Un des principaux enjeux a été son très court délai de réalisation (17 mois).
Le deuxième est destiné au marché pétrole et gaz puisqu’il s’agit d’un module technique électrique et de conditionnement d’air destiné à la FPSO Girassol en Angola (floating production storage and offloading unit, unité flottante de production, de stockage et de déchargement), pour en augmenter la capacité de production.
Un des principaux enjeux de la réalisation de ce module a été de concevoir une structure légère de manière à pouvoir réaliser les travaux d’intégration offshore avec le moyen de levage mobilisé à cet effet.
Offshore pétrolier et éolien
Dans le domaine de l’offshore pétrolier, le développement de nouvelles technologies a accompagné l’évolution des unités de production fixes vers des unités flottantes (FPSO) ancrées à des profondeurs de plus en plus importantes, rendant ainsi accessibles de nouvelles ressources en hydrocarbures.
Module technique de conditionnement d’air installé en Angola.
STX France a déjà réalisé plusieurs études de conception de FPSO ou d’unité flottante de production de GNL axées sur la structure du flotteur, ou sur les quartiers d’habitation. Les fabrications elles-mêmes peuvent être exécutées ailleurs qu’à Saint-Nazaire.
Le secteur des énergies marines renouvelables est encore peu mature, à l’exception de l’éolien offshore posé qui dispose à ce jour d’une base installée opérationnelle de taille significative. En juillet 2014, on comptabilisait (d’après les statistiques de l’EWEA – European Wind Energy Association) plus de 8 GW raccordés au réseau électrique.
En France, six projets éoliens offshore au large des côtes métropolitaines ont été attribués à différents groupements, pour une puissance totale de l’ordre de 3 GW. Ces projets devraient voir le jour dans les années qui viennent, et d’autres vont être lancés pour poursuivre le déploiement en France et ainsi contribuer de manière significative à l’objectif de 32 % d’énergies renouvelables dans la consommation finale d’énergie en 2030 fixé par la loi sur la transition énergétique.
Pour y parvenir il faudra toutefois que l’innovation et le déploiement à grande échelle puissent en réduire les coûts à un niveau acceptable pour le consommateur : notamment par l’augmentation de la puissance unitaire des turbines (il existe des développements de machines pouvant aller jusqu’à 10 MW), par l’augmentation de la taille des rotors (meilleur facteur de charge des machines), par la réduction des délais de construction (donc de la durée d’immobilisation du capital).
Grâce à l’innovation et à la R & D, les postes de transformation électrique offshore et les fondations métalliques d’éolienne offshore peuvent aussi fortement contribuer à la réduction des coûts de l’électricité éolienne offshore.
Optimiser les plateformes
Station électrique de Westernmost Rough (Grande-Bretagne).
Les postes de transformation offshore ont une fonction clé dans la ferme éolienne, qui consiste à concentrer l’électricité produite par les éoliennes, en élever la tension et l’exporter vers la terre. Un certain nombre de systèmes de supervision et de sécurité de la ferme éolienne y sont également installés.
Le programme de recherche et développement « Watteole » est lancé depuis trois ans. Il poursuit plusieurs objectifs dont celui de la standardisation. En effet, avec six projets aujourd’hui attribués en France d’une puissance d’environ 500 MW chacun, il paraît tout à fait réaliste de travailler sur la définition d’une plateforme commune.
Elle permettrait de passer d’une logique de « produit unitaire » à une logique de « produit série ». Les gains obtenus liés à l’industrialisation du produit et à la courbe d’apprentissage ou encore au volume d’achat seraient significatifs.
“ Un excellent terreau pour le développement de nouvelles activités ”
Un autre objectif de ce programme est de réduire la masse de la structure en acier de la plateforme. En effet, la masse est un important inducteur du coût de la plateforme ; la réduire permet de diminuer les coûts de fabrication, de transport et d’installation en mer, et de réduire également la masse de la structure support de la plateforme.
L’enjeu est important et c’est bien une analyse de coût complet de la fonction qui doit être réalisée. Il sera parfois préférable de ne pas pousser à l’extrême la cure d’amaigrissement : par exemple, les qualités des aciers devront être adaptées à leur utilisation, tout en étant raisonnablement disponibles sur le marché.
Des structures des navires à celles des plateformes
Une des innovations mises en œuvre pour réduire les masses repose sur l’utilisation de méthodes de conception de la structure issues de la construction navale plutôt que celles habituellement utilisées dans l’offshore pétrolier.
“ Le croisement d’idées est une source importante d’innovation ”
Le standard de l’offshore pétrolier, dont s’est naturellement inspirée l’industrie de l’éolien offshore, est de concevoir des structures dites de type « poteaux-poutres » : seuls les poteaux et les poutres sont structurels, les cloisons verticales et les ponts ayant des fonctions telles que l’étanchéité ou l’isolation.
Dans les plateformes électriques conçues par STX France, les cloisons verticales et les ponts sont fabriqués en panneaux d’acier raidis et contribuent à la tenue de l’ouvrage. Outre la réduction de masse, c’est aussi l’industrialisation des procédés qui permet de réduire les coûts de fabrication.
En effet la fabrication de panneaux d’acier raidis peut être plus facilement automatisée que l’assemblage par soudage de poteaux et de poutres.
Croiser les idées
Les différents thèmes d’innovation et de R & D évoqués illustrent la complexité des problématiques rencontrées et permettent de souligner l’importance de la collaboration entre les différents acteurs. Ils démontrent aussi que, comme souvent, le croisement des idées en provenance de différents domaines tels que celui de l’offshore pétrolier, celui de la construction navale et celui des énergies marines renouvelables, est une source importante d’innovation.
Rappelons qu’un fort développement des énergies marines renouvelables en France contribuera aussi à la mise en place d’une industrie pérenne source de création d’emplois : c’est aussi l’objectif de STX, qui a décidé d’investir 20 millions d’euros dans la réalisation d’une unité de production dédiée aux énergies marines, actuellement en construction, qui déploiera des moyens et des méthodes de production de pointe.
Dans les plateformes électriques conçues par STX France, les cloisons verticales et les ponts sont fabriqués en panneaux d’acier raidis.