L’innovation au service de l’industrie pétrolière
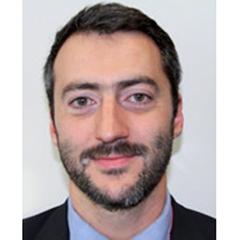
Quelles sont les principales évolutions connues par le groupe ?
FMC — Food Machinery Corporation — a été créé par John Bean dans les années 1870. La société est notamment l’inventeur du spray qui est utilisé pour diverses applications aujourd’hui.
Historiquement, FMC s’est d’abord spécialisée dans l’industrie agroalimentaire avant de se diversifier sur différents marchés, dont l’armement, les applications et les équipements aéroportuaires ou encore l’énergie.
Dès le début des années 2000, l’entreprise a fait le choix de se recentrer exclusivement sur l’industrie pétrolière et gazière. Les activités ont donc été séparées en FMC Technologies pour l’activité Oil & Gas, et John Bean Corporation pour le reste des activités du groupe.
Dans les années 50, FMC Technologies crée le premier bras de chargement à Brea en Californie, et sous-traite une partie de sa fabrication à LUCEAT, entreprise française basée à Sens.
Dans les années 70, suivant le choc pétrolier, FMC Loading Systems rachète LUCEAT et transfère progressivement toute son activité de systèmes de chargement en France à Sens.
Sur ce marché du bras de chargement, quel est votre positionnement ?
TechnipFMC Loading Systems est leader historique sur ce segment. Nous sommes le plus ancien acteur sur le secteur avec la plus grande base installée de systèmes de chargement au monde.
Notre leadership s’appuie, entre autres, sur notre capacité historique à nous démarquer grâce à des solutions innovantes. Depuis toujours, nous investissons intensivement dans la R&D et intégrons nos clients dans notre démarche d’innovation pour développer de nouvelles solutions.
Cette démarche nous permet d’accompagner nos clients dans leurs challenges en leur proposant des solutions toujours plus innovantes.
Le 17 janvier dernier, vous avez fusionné avec Technip.
Comment cela impacte-t-il votre R&D et le développement de vos bras de chargement ?
Cet évènement marque la fusion de deux gros acteurs du monde du Oil & Gas. C’est avant tout une fusion intelligente et complémentaire qui donne naissance à un nouveau leader mondial des projets, des technologies et des systèmes dans le secteur du pétrole et du gaz, visant à optimiser les performances de l’industrie mondiale de l’énergie.
Une des synergies liées à la fusion est la recherche et développement conjointe entre ex-FMC Loading Systems et la branche d’ex-Technip Coflexip, spécialiste reconnu en composants flexibles, afin de développer des solutions hybrides, flexibles ou rigides, qui permettra une optimisation des coûts des systèmes de chargement.
Nous allons pouvoir tirer profit du meilleur de Technip et de FMC Technologies pour développer des solutions mixtes inédites.
Le projet Prelude est d’ailleurs une illustration de cette fusion.
Pouvez-vous nous en dire plus ?
Le projet Prelude est né de la volonté de Shell d’exploiter les champs gaziers éloignés des côtes et en eaux profondes, pour lesquels une solution d’usine flottante de production de gaz était la plus économique. Jusque-là, les usines d’extraction, de traitement et de liquéfaction du gaz étaient exclusivement onshore.
Avec Prelude, nous avons contribué à la première usine offshore de 500 m de long. C’est d’ailleurs la plus longue unité flottante jamais construite. Dans ce projet, Technip avait pour mission de concevoir, de fabriquer et de mettre en service Prelude et FMC Technologies avait en charge, entre autres, le développement et la fourniture de la solution de chargement du gaz liquéfié entre l’usine flottante et les méthaniers.
Prelude a constitué un énorme challenge technique au vu des nombreuses contraintes spécifiques à cette configuration inédite : dimensionnement de l’équipement, résistance à la corrosion, fatigue des matériaux, connexion du bras de chargement à des bateaux en mouvement…
Enfin, à l’image d’autres innovations menées par Loading Systems, nous avons développé un centre d’essai et une maquette à l’échelle ¼ du bras de chargement de Prelude pour valider les aspects opérationnels, les calculs et le comportement du bras dans les conditions réelles d’utilisation.
Aujourd’hui, ces maquettes sont également un support marketing et de formation très important qui nous donne la possibilité de promouvoir nos produits, mais aussi notre expertise et savoir-faire technologiques en montrant à nos clients des éléments concrets.
Quelles sont les autres innovations sur lesquelles vous travaillez ?
Depuis 50 ans, l’industrie du bras de chargement utilise des systèmes hydrauliques pour l’opération de ceux-ci, principalement justifié par l’avantage économique fourni par les solutions hydrauliques, mais qui présentent certains inconvénients : coûts de maintenance élevés, complexité de la détection de panne et risque de pollution en cas de fuite d’huile.
Pour pallier cette situation, depuis plus de 20 ans, nous nous intéressons avec attention au monde de l’industrie et plus particulièrement aux systèmes électriques. Nous avons pu constater de nets progrès depuis 10 ans dans le monde de l’industrie électrique qui nous ont permis de nous lancer dans le développement de bras entièrement électriques afin de remplacer les systèmes hydrauliques par des moteurs et des actionneurs électriques.
Il nous a fallu plus de cinq ans pour développer cette innovation, d’abord en partenariat avec SHELL, avant de finaliser le processus de manière autonome ces deux dernières années.
Aujourd’hui, nous proposons cette innovation à nos clients qui expriment un fort intérêt pour cette solution plus fiable qui permet de réduire aussi bien les coûts d’exploitation que les risques de pollution.
La réduction des coûts est l’axe prioritaire qui guide aujourd’hui notre R&D. Il y a dix ans, les efforts en R&D étaient principalement menés par la volonté d’ajouter de nouvelles fonctions aux systèmes de chargement. Aujourd’hui, avec la baisse durable du prix du baril, les opérateurs pétroliers et gaziers sont contraints de réduire drastiquement leurs coûts pour rester rentables et rendre possible le développement de nouveaux projets.
En conséquence, nous devons proposer à nos clients des équipements moins chers à l’achat, mais aussi en maintenance, et c’est en misant sur l’innovation que nous réussissons les gains les plus significatifs.
AVEC PRELUDE, NOUS AVONS CONTRIBUÉ À LA PREMIÈRE USINE OFFSHORE DE 500 M DE LONG. C’EST D’AILLEURS LA PLUS LONGUE UNITÉ FLOTTANTE JAMAIS CONSTRUITE.
Il y a également un aspect humain dans l’innovation et la R&D qui se traduit généralement par l’accueil de thésards ou de stagiaires.
Comment cela se traduit-il chez vous ?
Nous avons noué de nombreux partenariats avec des universités et des écoles qui contribuent à travers leurs thésards et leurs stagiaires à notre R&D en prenant en charge des études.
Certaines autres industries ou domaines d’expertise trouvent des débouchés et une valeur ajoutée dans les développements de nouveaux systèmes de chargement. Ce travail en réseau apporte une valeur ajoutée réciproque à toutes les parties prenantes impliquées.
Et pour conclure ?
Malgré un apparent conservatisme, l’industrie pétrolière est un univers très dynamique propice à l’innovation en particulier dans un contexte difficile ou les réductions de coûts sont synonymes de survie et de pérennité.
Les mutations connues par le secteur au cours des dernières années ont renforcé la nécessité d’innover pour accompagner les attentes nouvelles des principaux acteurs de ce domaine, mais aussi pour se démarquer de nos concurrents.
Plus que jamais, nous mettons notre innovation au service de l’industrie pour apporter des solutions pertinentes et en adéquation avec les besoins des différentes parties prenantes.