L’usine du futur de Safran, atout majeur de compétitivité et réactivité
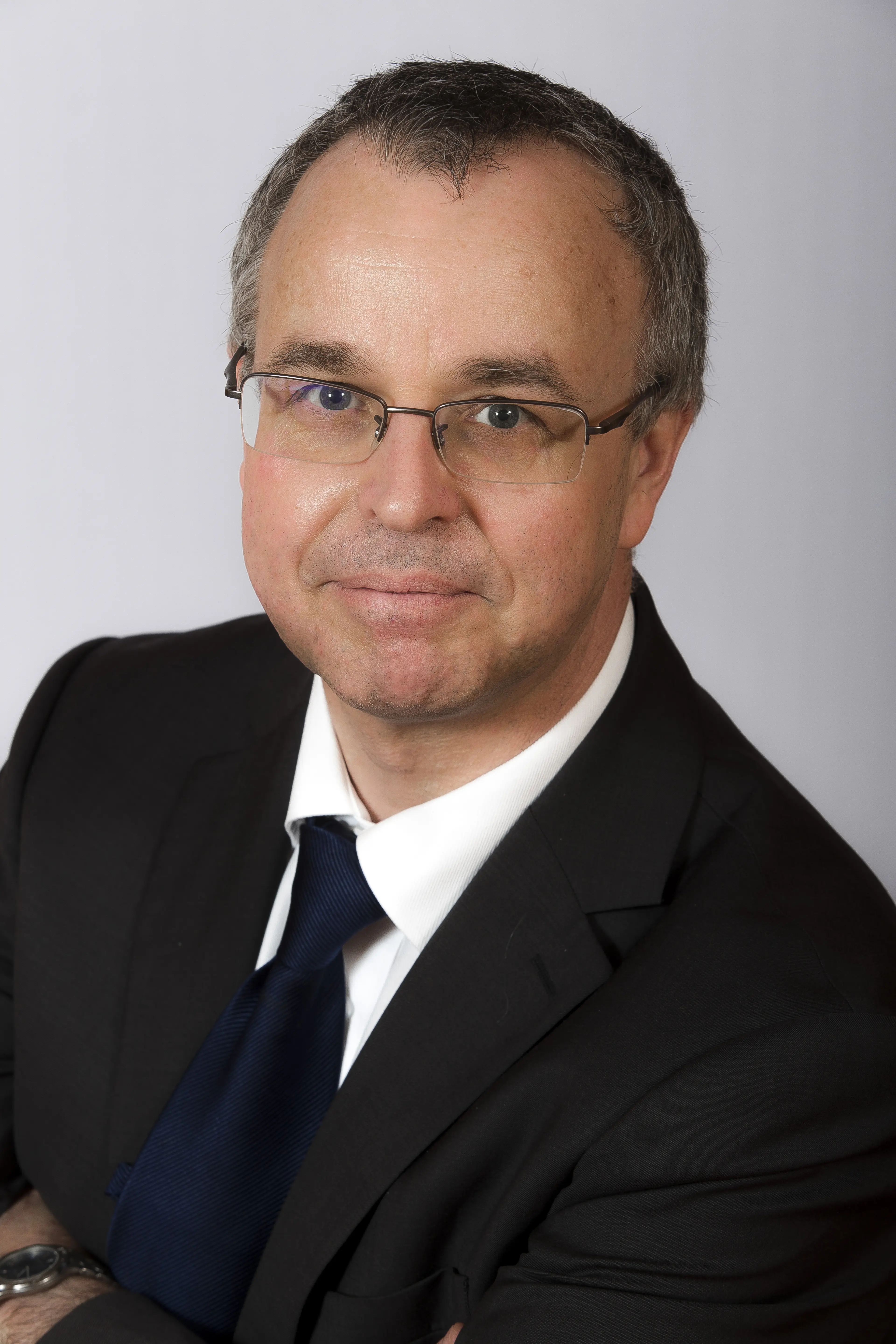
Devenu le troisième acteur aéronautique mondial, hors avionneurs, Safran met tout en œuvre pour assurer les montées en cadence et répondre aux besoins de ses clients. Outil de compétitivité en rupture engendrant des gains de productivité remarquables, l’usine du futur constitue un atout majeur dans l’activité du groupe et s’inscrit au cœur même de sa stratégie.
Commençons par ce que nous avons fait. Compte tenu de la nature de nos activités, nos lignes de production présentent des cadences faibles, nous sommes partis de l’idée de définir une approche globale pour une mise en œuvre locale. Cette spécificité de nos activités facilite le déploiement d’une transformation digitale à grande échelle. Les technologies de l’usine du futur permettent bel et bien d’améliorer la performance industrielle : techniques de simulation, réalités augmentée et virtuelle, contrôles numériques, objets et machines connectés.
Nous nous sommes aussi fixé comme objectif d’obtenir des gains à chaque étape de la vie des produits.
REPÈRES
Safran est un groupe international opérant dans les domaines de la propulsion et des équipements aéronautiques, de l’espace et de la défense. Depuis le rachat de Zodiac Aérospace en février 2018, son effectif est de 91 000 personnes pour un chiffre d’affaires d’environ 21 milliards d’euros (pro forma 2016).
Assurer la continuité numérique
La continuité du modèle numérique tout au long des différents processus (développer – fabriquer – maintenir en service) est en passe de devenir incontournable.
Pour préparer l’usine du futur, une expression standard des besoins à couvrir par le système d’information a été établie pour faire le lien entre les différents outils permettant de suivre la vie du produit, depuis sa conception jusqu’à sa livraison.
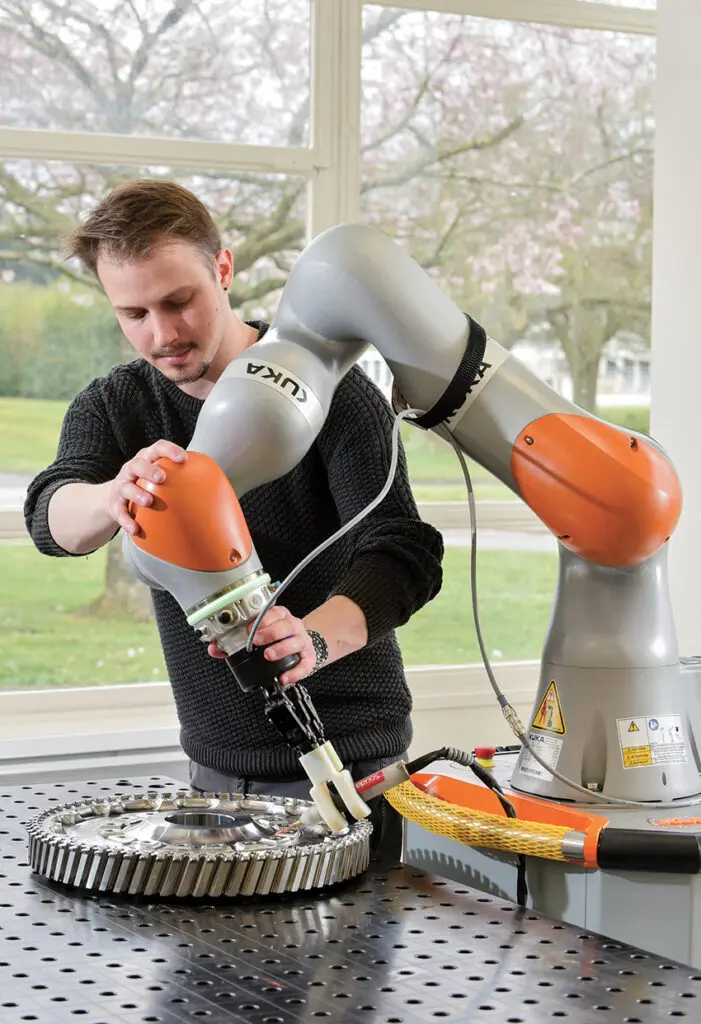
Modéliser et simuler
Modélisations et simulations d’une part et réalités augmentée et virtuelle d’autre part se nourrissent mutuellement pour anticiper les situations industrielles et diagnostiquer les écarts.
La réalité augmentée vise à superposer un modèle numérique représentatif de la théorie et de le comparer à une situation réelle pour détecter d’éventuels écarts. Safran travaille ces sujets en collaboration avec Diota, une start-up française dans laquelle Safran Corporate Ventures a investi, et la réalité virtuelle immerge les opérationnels dans la situation future de travail.
La réalité augmentée a été utilisée pour aider les opérateurs à monter les connecteurs sur la ligne d’assemblage des faisceaux avions (câblages) à Villemur. Grâce à la modélisation et la réalité virtuelle, la ligne de montage des nacelles A320neo au Havre a été conçue « bonne du 1er coup » en optimisant l’organisation et en intégrant les critères santé – sécurité – environnement.
Assister l’opérateur : Safran et la cobotique
Les travaux manufacturés représentent 25 % du coût de production. Les perspectives de gains ouvertes par la cobotique y sont nombreuses. La cobotique désigne la conception et la réalisation de systèmes d’interactions entre l’homme et le robot. Son développement permet d’éviter les situations de travail pénibles tout en optimisant la productivité. Safran met en œuvre des cas d’application : la téléopération est employée pour le nettoyage d’une cuve de propergol chez ArianeGroup, la colocalisation collaborative est utilisée sur des postes d’équipement nacelles au Havre et la comanipulation par le montage d’un module équipement est testée sur la ligne de production des moteurs LEAP (produit phare de Safran) à Villaroche.
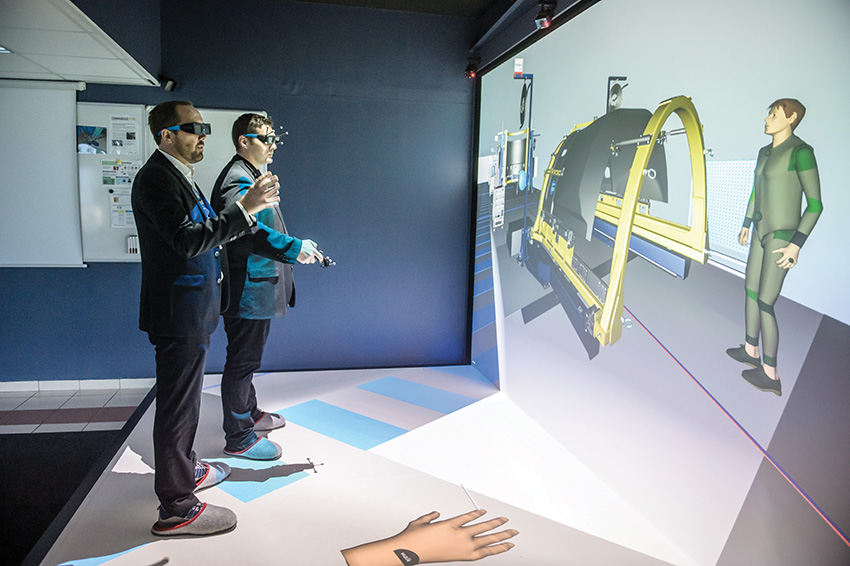
Contrôler
Le contrôle représente 25 % du coût de production d’une pièce. L’utilisation des technologies de contrôle numérique et d’analyse automatisée pour effectuer le contrôle final de conformité du produit assemblé peut permettre de réduire ce coût de moitié. Ainsi, sur la ligne de production des nacelles A320neo, Safran Composites a développé et mis au point de nouvelles techniques de contrôle par thermographie infrarouge sur les panneaux carbone. Safran Tech et Safran Engineering Services ont développé et mis au point des algorithmes de traitement de la donnée de contrôle et d’aide à la décision. Grâce à la réalité augmentée, l’opérateur réalise la contre-vérification des zones proposées par le système d’analyse.
Ce que nous faisons
Notre approche est basée sur une stratégie technologique et une méthode de déploiement organisée par étapes.
Le groupe coordonne ses efforts sur les sujets de R & T industrielle suivants : contrôles du futur ; cobotique ; nouveaux procédés de fabrication ; connectivité des moyens et assistance cognitive à l’opérateur.
Une partie de cette feuille de route R & T industrielle est réalisée en partenariat avec d’autres industriels et des laboratoires scientifiques. En particulier, Safran est partie prenante de l’écosystème Factory Lab à Saclay. Ce dernier regroupe des industriels (Safran, PSA, Vinci…), des acteurs académiques (Ensam, Cetim, CEA) et un écosystème de PME et de start-up.
Une méthode appliquée sur 65 lignes de production et 30 sites
La coordination centrale s’organise autour du projet usine du futur. Le chef de projet s’appuie sur des référents métiers dans les sociétés et sur un réseau dans chacune des sociétés du groupe pour partager les bonnes pratiques, mais aussi optimiser et harmoniser autant que possible les spécifications fonctionnelles.
Des projets de lignes de production du futur ont été identifiés et planifiés par toutes les sociétés. Ils concernent des activités industrielles de fabrication, de montage, ou encore de réparation (MRO). Cela représente un total de 65 lignes de production sur plus de 30 sites et 97 projets techniques ou relatifs aux systèmes d’information.
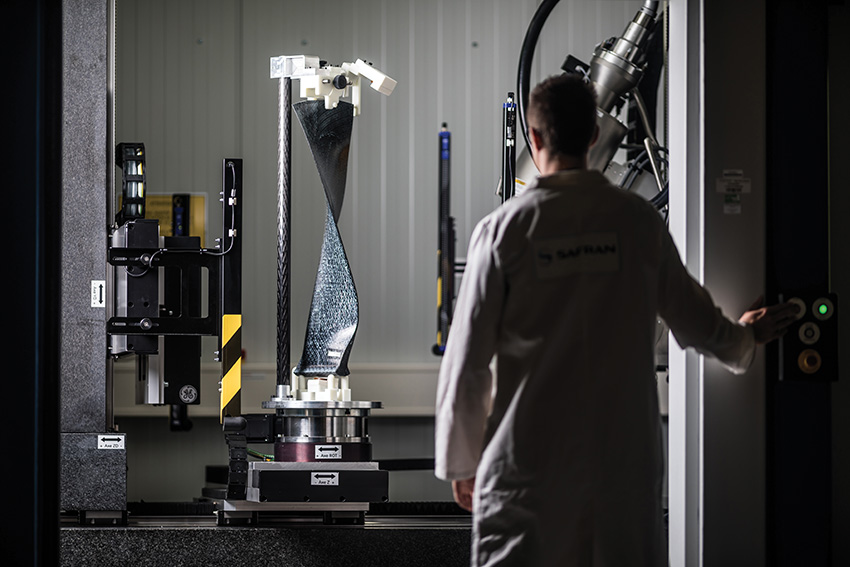
Ce que nous devons faire
Pour relever les challenges technologiques et industriels, il nous faut organiser la capture des données, connecter les machines et sécuriser nos systèmes d’information.
La capacité à capter des quantités importantes de données en temps réel, et les nouvelles technologies qui agrègent des données de l’amont à l’aval des processus invitent à rationaliser et interfacer les systèmes. La mise à profit des nouvelles technologies de l’usine du futur passe donc par une modernisation des systèmes d’information et le développement d’applicatifs agiles pour les capter, les stocker, les analyser et enfin les utiliser. C’est un travail que Safran a initié.
Connecter les machines
Les nouveaux équipements industriels sont conçus pour être de plus en plus intégrés avec le système d’information : services d’échange, transfert, traitement et stockage des données comme l’ERP. Pour profiter au mieux des nouvelles possibilités apportées par ces évolutions technologiques, Safran a identifié les développements prioritaires pour son système d’information appliqué à l’usine du futur dans les usines du groupe : la géolocalisation des outils et des produits ainsi que l’acquisition et la distribution des données machines, autre enjeu majeur. En front-office, les opérateurs de ligne pourront désormais piloter l’ensemble de la ligne de production via des cockpits de supervision transverse, pour intervenir dans un délai optimisé en cas d’anomalie. En back-office, les ingénieurs méthodes spécialistes des procédés pourront analyser les données de production pour corriger les dérives de production et stabiliser le niveau de qualité grâce aux outils d’analyse de données (Business Intelligence et Analytics).
Sécuriser
Conçus pour être robustes d’un point de vue de sûreté de fonctionnement, les systèmes d’information industriels doivent être protégés face à des cyberattaques dont ils sont la cible. Pour adapter le système de sécurité Safran à l’usine du futur, une coopération importante entre la direction des systèmes d’information (DSI) et la direction industrielle est déjà organisée pour définir et déployer des règles d’interconnexion des réseaux industriels avec les réseaux bureautiques et Internet.
Une profonde et nécessaire évolution des compétences
Sur la base du calendrier de déploiement par ligne de produits, on estime qu’environ un collaborateur sur cinq en France sera impliqué dans l’usine du futur d’ici à cinq ans. Tous les métiers seront concernés, mais ce sont la fabrication et la maintenance où l’évolution sera la plus forte.
L’analyse des évolutions de compétences induites par l’usine du futur s’appuie sur différents travaux issus des comités métiers, des groupes de travail des réseaux RH et des retours d’expérience internes et externes. Dans cette vision, l’opérateur effectue moins d’actions sur le produit, plus de supervision et de contrôle dans des lignes automatisées. En conséquence, il doit être plus polyvalent et piloter plusieurs machines plutôt qu’une seule dans l’organisation actuelle. Au-delà des opérateurs, toute l’équipe de production est plus autonome et responsabilisée. La maintenance industrielle évolue aussi pour pouvoir maintenir des machines plus complexes.
Dans l’usine du futur, c’est aux méthodes de fabrication qu’incombe le rôle majeur d’intégrer et tirer le meilleur parti de l’analyse de données des nouvelles technologies.
Investir dans de nouvelles formations et de nouvelles méthodes pédagogiques
Les formations en société et via Safran University intègrent déjà les notions de nouvelles technologies et de digitalisation dans les programmes, et il existe des exemples de formation incluant la réalité virtuelle / augmentée. Ces formations seront amenées à se développer prochainement.
Le CampusFab est la « Plateforme de formation à la mécanique industrielle de demain ». Le futur site est en cours de construction à Bondoufle et ouvrira en 2019. Le pilotage du projet CampusFab est réalisé par un consortium composé d’industriels (Safran, Fives Maintenance, le Gifas, le GIM, Dassault Systèmes et la CCI de l’Essonne), de centres de formation (l’Aforp, l’Afpa, la Faculté des métiers de l’Essonne), du pôle de compétitivité ASTech Paris Région et de The Adecco Group. Le CampusFab mettra à disposition des apprentis, des étudiants, des stagiaires et des formateurs les moyens industriels et numériques typiques d’une « usine du futur », ayant pour objectif d’accompagner la transformation de l’industrie en France et d’assurer la compétitivité du secteur. Il permettra notamment de satisfaire les besoins des entreprises industrielles dans le recrutement de techniciens et d’opérateurs formés aux nouveaux processus de production.
Chaque année, il accueillera en apprentissage une centaine d’alternants pour trois ans d’études menant au baccalauréat professionnel ou au brevet de technicien supérieur, ainsi que plusieurs centaines de salariés en formation continue. Safran prévoit notamment d’ouvrir cette plateforme de formation à ses collaborateurs dans le cadre de la formation continue.
Plus de compétivité et de satisfaction de la clientèle
À l’heure où Safran renouvelle et renforce son outil industriel, l’usine du futur revêt une importance toute particulière. Safran se réorganise pour répondre à son double objectif de compétitivité et de satisfaction toujours plus grande de nos engagements vis-à-vis de nos clients et fournisseurs.
Usinage portes fermées
De nouvelles applications permettent de mieux modéliser et de simuler des opérations pour les optimiser.
Le concept d’ « usinage portes fermées » permet ainsi de faire fonctionner plusieurs machines pendant des dizaines d’heures en pleine autonomie sous surveillance réduite ou distante : à Bidos chez Safran Landing Systems, 4 opérateurs pour 12 machines. Initialement, l’usinage d’une tige de train principal d’atterrisseur avait occasionné soixante arrêts machines. Nous sommes passés à deux arrêts grâce à ce nouveau procédé.
Nous retrouvons un modèle équivalent sur d’autres lignes, comme celle des pales de turbines de Safran Helicopter Engines à Bordes : la simulation et la refonte du procédé d’usinage ont permis de réduire le nombre de passes de rectification de 6 à 2.
L’usine du futur de Safran : un modèle d’ores et déjà éprouvé et reconnu
Sur les nouvelles lignes de produits labellisées « Usine du futur », les améliorations par rapport au modèle antérieur sont convaincantes, avec des gains en cycles et en coûts supérieurs à 15 %.
Ces avancées ont également valu à Safran deux distinctions, sur les 20 premiers labels « Vitrines industrie du futur » décernés en France par l’Alliance pour l’industrie du futur, toutes industries confondues. Elles ont été décernées à la ligne assemblage du moteur LEAP à Villaroche, et à la ligne de production de pales de turbines d’hélicoptères à Bordes.
Retours d’expérience
Les retours d’expérience sur les lignes pilotes Safran confirment que les compétences transverses sont essentielles pour travailler dans l’usine du futur : savoir s’adapter, être capable de travailler en mode collaboratif dans un environnement changeant et interactif, développer une culture de la donnée. En conséquence, le manager de proximité voit son rôle évoluer dans l’usine du futur. Il joue donc un rôle essentiel sur les sites dans l’accompagnement de ces transformations pour coconstruire avec les équipes concernées des plans d’action et des plans de conduite du changement adaptés. Le soutien du top management est aussi un facteur clé de réussite pour la mise en œuvre de cette stratégie.