Management des risques financiers et opérationnels de la « supply chain »
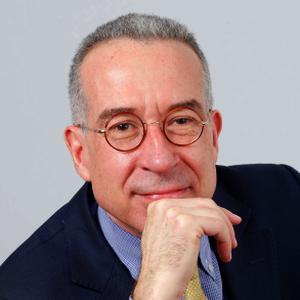
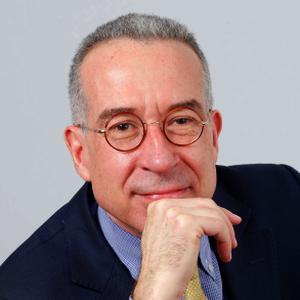
Beaucoup de progrès ont été réalisés depuis l’émergence, il y a une dizaine d’années, du concept de « supply chain management ». La réalité montre néanmoins que le niveau de performance des supply chains reste très en deçà des ambitions initiales, quel que soit le secteur d’activité : certains mettent en cause des erreurs de planification, d’autres des défaillances au niveau opérationnel.
Nous montrons pourquoi la gestion des risques est devenue l’enjeu majeur de la supply chain et quel peut être l’apport dans ce domaine, de techniques et d’outils largement éprouvés en finance.
Les enjeux de la supply chain
Rappelons que l’enjeu majeur de la supply chain, quel que soit le secteur d’activité, est d’assurer une meilleure synchronisation des flux de « bout en bout », des fournisseurs les plus en amont aux clients les plus en aval (voir schéma 1). Plusieurs facteurs ont rendu cette problématique de plus en plus complexe à traiter, notamment :
• l’explosion de la diversité produit,
• le raccourcissement drastique des cycles de vie,
• la mondialisation des marchés (clients et fournisseurs),
• les exigences de service (délais de livraison, personnalisation…),
• la pression croissante sur la réduction des coûts (logistiques, stocks…),
• la forte interdépendance entre tous les acteurs d’une filière (fournisseurs de plusieurs rangs, sous-traitants, constructeurs, distributeurs, prestataires logistiques…).
Le supply chain management (SCM) s’est imposé ces dix dernières années à la fois comme une discipline à part entière, comme une fonction-clé de management, et beaucoup d’entreprises y ont consacré des investissements en temps et en argent considérables.
Cependant le résultat n’a pas été, dans de nombreux cas et tous secteurs confondus, à la hauteur des ambitions, comme peuvent en témoigner les exemples récents de grandes entreprises confrontées :
• à des problèmes de dépréciation massive de leurs stocks (cas de l’industrie high-tech) ou de financement de leur BFR (Besoin en fonds de roulement),
• à de graves ruptures dans les services rendus aux clients, notamment par l’incapacité à tenir les engagements de délais, avec les conséquences potentielles de perte ou de décalage de revenus (cas de l’industrie aéronautique & défense),
• à l’explosion de stocks d’invendus, du fait notamment des politiques d’achats massifs dans les pays « à bas coûts » et de leurs effets induits sur le manque de flexibilité des approvisionnements (cas de la grande distribution).
Les prévisions sont toujours fausses
De manière quasi systématique, la première des causes incriminées vient du manque de fiabilité des prévisions, conduisant d’ailleurs à deux attitudes opposées :
• persévérer dans la « fiabilisation » des prévisions, par l’amélioration des pratiques, la mise en œuvre d’outils sophistiqués, le partage d’informations prévisionnelles avec ses clients, etc.,
• à l’inverse, se concentrer sur la réduction des délais à tous les niveaux et sur la « flexibilisation » de la supply chain, de façon à la « tirer » par la demande réelle.
Il est significatif de constater que, dans beaucoup de cas, aucune de ces deux politiques n’intègre un modèle d’évaluation du niveau de risque induit sur la supply chain, et surtout de la façon dont le risque est réparti entre les acteurs.
Cette situation pénalise fortement les initiatives d’amélioration, non pour des raisons de méthodologies ou de techniques de planification de la supply chain, mais en raison de freins culturels, organisationnels et contractuels :
• il est certes évident que prévoir un niveau de ventes moyen de 100 unités, avec un écart possible de + ou – 90 unités, ou bien faire la même prévision avec un écart possible de + ou – 10 unités réduit a priori le niveau de risque sur le stock ou le service. Comment inciter pour autant le client ou le commercial à faire durablement cet effort, sans un mécanisme clair de valorisation et de partage des risques associés ?
• de la même façon, chacun sait que les prévisions à moyen terme sont en général moins fiables que les prévisions à court terme, d’où l’intérêt d’une supply chain en « flux tiré ». Mais jusqu’où faut-il réduire les délais et tendre la supply chain, par rapport aux surcoûts et risques induits, que ce soit en augmentation de capacité, risques de rupture, etc. ?
Paradoxalement, notons que les efforts de flexibilisation ont été bien souvent imposés aux fournisseurs les plus en amont de la supply chain, là où la demande devrait précisément être la plus stable.
Modéliser et valoriser les risques de planification
En s’inspirant de techniques financières éprouvées, nous avons développé un ensemble de modèles et de « boîtes à outils » adaptés à la supply chain, et permettant notamment :
• de valoriser les risques, en particulier liés aux erreurs de planification,
• de réduire drastiquement le coût des erreurs de planification, qu’il s’agisse d’approvisionnement, de gestion des stocks ou de plans de production,
• de définir des conditions équilibrées de partage des bénéfices et des risques entre les partenaires (internes et externes) de la supply chain.
Nous donnons ci-après une illustration (voir figure 2), relative à la problématique d’évaluation de la rentabilité et des risques d’une politique de stock, utilisant les techniques de VaR (Value at Risk).
Figure 2
Modélisation de la VaR (value at risk) appliquée à la gestion des stocks
Les fondements de notre approche reposent sur deux constats :
• d’une part les erreurs de prévisions sont très souvent considérées comme un élément exogène à l’entreprise, du fait des incertitudes et de la volatilité de la demande. D’autres facteurs contribuent pourtant, parfois très significativement, à ces « erreurs » : évolution de la politique marketing, changement d’objectifs commerciaux, nouvelles contraintes financières, etc. D’où l’intérêt, pour mesurer les risques, de considérer les prévisions comme un objectif de vente (en quantités, prix) à un horizon donné et de s’intéresser à la probabilité (taux) de réalisation de cet objectif ;
• d’autre part le stock a trop longtemps été considéré comme un seul facteur de coût, amplifié par le dogme du « zéro stock » des années quatre-vingt-dix. Or le stock est d’abord un actif, au même titre qu’un investissement en capacité de production : sa rentabilité brute est fonction de la marge attendue de la vente des produits sur la durée d’écoulement planifiée du stock (sans tenir compte ici des délais de paiement). Bien entendu sa rentabilité nette est dans la pratique variable en raison des pertes potentielles, tant par le risque de surstock (engendrant une dépréciation), que par les risques de pénurie (engendrant une perte de CA).
Le modèle de la figure 2 illustre, de manière simplifiée, le calcul de la VaR, mesurant ainsi le niveau et la probabilité de perte potentielle sur l’actif (le stock), en fonction :
• des écarts probables de consommation,
• des délais d’approvisionnement et des écarts probables de réalisation,
• des délais d’écoulement planifié (ou du taux de rotation).
Ces outils permettent ainsi de simuler et de valoriser la rentabilité et le risque associé de différentes politiques de supply chain, comme le montre l’exemple de la figure 3 pour un portefeuille de produits dans l’univers de la distribution.
Figure 3
Valorisation de la rentabilité et des riques du portefeuille de produits en stock
Le coût du risque et l’impact sur la marge brute (gross margin) et nette (net margin) sont mesurés pour chacune des options, facilitant ainsi la résolution des arbitrages-clés :
• faut-il augmenter la fréquence d’approvisionnements (taux de rotation) ? Dans ce cas, les espérances de gains sur la marge nette (diminution du risque) compensent-elles la perte sur la marge brute (augmentation des coûts d’approvisionnement) ?
• faut-il négocier un raccourcissement des délais fournisseurs ? Dans ce cas, les espérances de gains sur la marge nette compensent-elles la perte sur la marge brute (augmentation des coûts d’achat) ? Comment partager la prime de risque avec mon fournisseur ?
• quelle est l’incidence du taux d’erreurs des prévisions et sur quels produits dois-je faire porter mes efforts de fiabilisation ?
• comment optimiser mon portefeuille de produits en stock afin, soit de maximiser ma rentabilité, soit de minimiser mon risque, ou en fonction de l’équilibre souhaité rentabilité-risque ?
Nous sommes évidemment bien loin de la fameuse formule de Wilson, encore malheureusement trop souvent employée, qui permettait de calculer l’optimum économique d’une politique de stock en fonction des coûts fixes d’approvisionnement et des coûts variables de stockage. Rappelons pour mémoire que celle-ci date de 1913 ! et fait l’hypothèse qu’il n’y a aucune incertitude sur la demande…
Maîtriser les risques opérationnels de la supply chain
La maîtrise des risques de planification, grâce aux méthodes et techniques exposées ci-dessus, n’a malheureusement qu’une portée limitée, si celle-ci ne se traduit pas dans la réalité opérationnelle de la supply chain. Or les exemples abondent encore dans toutes les entreprises, de brusques variations des niveaux de performance, sans qu’il faille pour autant remettre en cause la qualité intrinsèque des processus d’exécution.
Ces défaillances proviennent en effet du manque d’intégration et de coordination entre la planification et l’exécution, pour plusieurs raisons :
• la complexité des processus d’élaboration, de mise à jour et de partage des plannings, qu’il s’agisse de prévisions, réapprovisionnement des stocks, production, etc. : il n’est pas rare encore que chaque service-fonction (commerciale, logistique, production, finance…) dispose de sa propre version, souvent via une reconsolidation sur des fichiers Excel, faute de disposer de moyens simples et efficaces d’analyse et de restitution (même avec les ERPs ou les logiciels dédiés à la planification de la supply chain – les APS) ;
• le manque de visibilité sur l’état précis des stocks ou des engagements de capacité, souvent là aussi faute de disposer de moyens simples de consolidation, contrôle, analyse, diffusion dans des environnements multiacteurs, multisystèmes d’informations, et cela malgré les ERPs en place. Bien entendu les informations de reporting sont accessibles, mais elles ne sont pas synchronisées avec le rythme quasi-temps réel de déroulement des opérations de la supply chain ;
• citons également la problématique de foisonnement des indicateurs de performance, souvent contradictoires, entre les organisations, les géographies, les fonctions, etc.
C’est pourquoi l’enjeu majeur de gestion de la supply chain aujourd’hui ne réside pas dans une plus grande sophistication de la planification, ni dans une meilleure efficacité de l’exécution : c’est grâce à une meilleure synchronisation des informations de planification et d’exécution, qu’il devient possible de créer un cercle vertueux d’amélioration de la performance et de la robustesse de la supply chain.
Les solutions mises en œuvre par les entreprises les plus avancées dans ce domaine s’appuient sur :
• un modèle de gestion et valorisation des risques, à la fois financiers (voir ci-dessus) et opérationnels,
• des technologies de capture, filtrage, historisation, traitement événementiel et asynchrone du flux d’informations, permettant une collecte des données en « temps réel », multiprocessus, multisystèmes, multiformats,
• des processus et solutions de « monitoring » des aléas-écarts entre les valeurs planifiées et les valeurs réalisées (niveau de stock, consommation de la demande prévisionnelle, etc.) et de détection des niveaux de risque,
• des processus de déclenchement d’alertes permettant d’anticiper les problèmes potentiels et de propager l’information auprès des acteurs concernés,
• des solutions d’aide à la décision et de collaboration synchrone pour faciliter la résolution « temps réel » des problèmes et éviter leur propagation et leur amplification.
C’est ainsi qu’a été développé un poste de pilotage assurant une supervision continue des risques de la supply chain et la mise à jour en temps réel des indicateurs-clés de performance, accessible via le Web à tous les acteurs (internes et externes).
Bien entendu, les solutions que nous évoquons ne se réduisent pas à la mise en œuvre de technologies : c’est à la fois un changement d’approche dans l’organisation des processus de management de la supply chain, le développement d’un savoir-faire et d’une culture de gestion du risque, et enfin la mise en œuvre de pratiques beaucoup plus collaboratives entre les différents acteurs impliqués pour la résolution des arbitrages opérationnels.
Conclusion
Face à la complexité grandissante des supply chains, le pilotage par les risques apporte une solution efficace et robuste de gestion : au niveau de la planification, en fournissant une mesure objective du risque pris par chacun des acteurs au regard des engagements de coût et de performance. Au niveau de l’exécution, par une meilleure anticipation des problèmes et leur mise sous contrôle grâce à des décisions coordonnées et synchronisées.