Une maturité internationale pour la fabrication additive
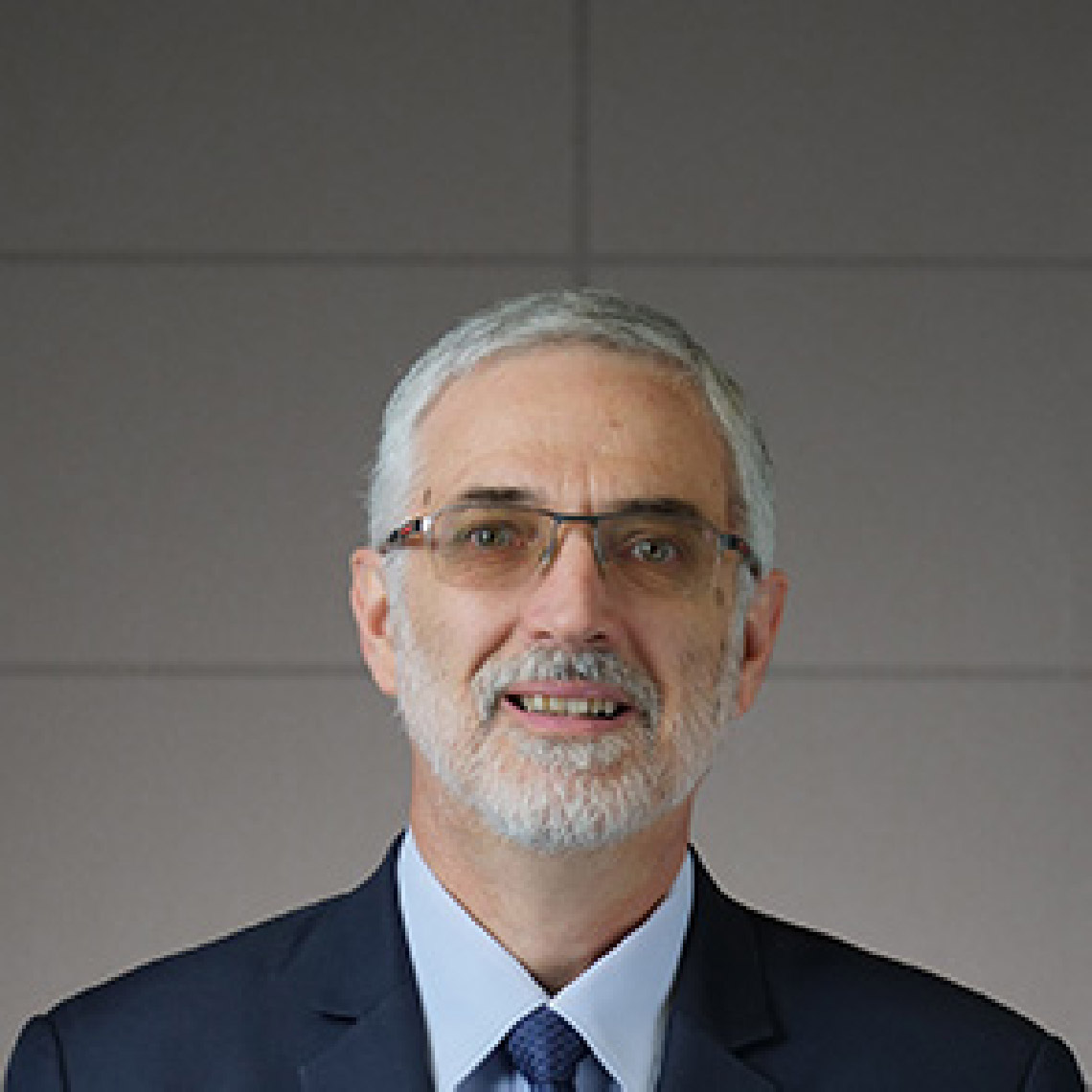
La fabrication additive a 35 ans et une grande dynamique de progrès. Dans cette dynamique mondiale, la France est bien placée. Les choix technologiques et industriels qui seront faits en la matière seront déterminants pour conserver voire développer cette position nationale et européenne.
Que dire quand on se réfère à plus de trente-cinq ans d’histoire depuis les premiers brevets de l’ère moderne jusqu’à nos jours ? Certes, il y a eu de nombreuses évolutions et de nombreuses étapes de progression. Mais beaucoup reste à faire. Notamment la mise en œuvre des matériaux métalliques pose de très nombreux problèmes sur l’ensemble de la chaîne de valeur fondée sur la fabrication additive. En effet, la plupart des pièces métalliques fabriquées sont des bruts qu’il faut ensuite parachever, comme cela est le cas pour la forge ou la fonderie. De plus, pour certains procédés fondés sur la fusion de poudre, les phénomènes et les transformations physico-chimiques mis en œuvre demandent un apport d’énergie conséquent, ce qui provoque des déformations et des contraintes résiduelles dans les pièces si rien n’est fait à la suite de la phase de fabrication additive.
REPÈRES
Au début, seule la stéréophotolithographie existait et elle permettait la mise en œuvre de résines dont la transformation physicochimique s’effectuait avec des lasers de faible énergie (quelques milliwatts). Malgré tout, on produisait des pièces en trois dimensions à partir d’un modèle numérique sans outillage et sans préparation compliquée de machines. Cette époque est bien lointaine et de nombreux autres principes physiques sont apparus, avec aujourd’hui sept classes de procédés répertoriés et normalisés (ISO 17296–2:2014E). Récemment, l’aéronautique a poussé en particulier vers la mise en œuvre de matériaux métalliques après s’être approprié celle des matériaux plastiques de manière générale.
Le métal se développe sous une poussée principalement européenne
De nombreux progrès sont malgré tout enregistrés et des évolutions de tendances ont été notées au cours des cinq dernières années. En effet, la fabrication de poudre métallique reste très coûteuse et la qualité de la poudre exigée pour les pièces aéronautiques ou pour le médical n’est pas négociable. Aussi, l’utilisation de procédés plus conventionnels utilisant du fil et fondés sur des principes de procédés de soudage plus traditionnels se sont développés et ont déjà trouvé des débouchés, en particulier pour la fabrication de pièces de grande taille dans de nombreux secteurs d’application. Certains de ces procédés ont trouvé des développements en Europe et au Japon, principalement, par le développement de machines ou d’environnement de production dits « hybrides » combinant plusieurs procédés, soit additifs, soit soustractifs, non seulement lors de phases de fabrication successives mais aussi par l’enchaînement d’opérations additives, soustractives et relevant d’autres procédés comme des traitements thermiques, des opérations spécifiques de finition ou de mesure, et d’autres encore.
D’autres procédés plus récemment disponibles sur le marché revisitent l’utilisation de matériaux de type MIM (moulage par injection métallique) à base de fils ou de granulés de matière thermoplastique enfermant des particules métalliques de taille et de nature diverses. Ainsi, il n’y a pas de manipulation de poudre, celle-ci étant « enfermée » dans le matériau plastique, lequel est ensuite extrait par déliantage thermique. La pièce est frittée thermiquement et éventuellement reprise en finition. D’autres procédés plus anciens ont eu un développement récent aux États-Unis d’Amérique tout d’abord, puis plus largement en Europe et en Asie, pour la fabrication de pièces métalliques à base de lit de poudre sur lequel on projette un liant. La pièce finale doit ensuite être déliantée, frittée ou infiltrée d’un autre matériau métallique à plus bas point de fusion. Le procédé de projection de liant est également utilisé pour la fabrication de moules ou de noyaux en sable pour la fonderie et aussi pour des pièces en matériaux plastiques ou céramiques. Parmi toutes les technologies, certaines constituent des solutions pour la fabrication de petites séries, alternatives à des procédés plus conventionnels. L’intérêt majeur dans ce cas est de disposer soit de pièces identiques de forme et topologie complexes en nombre important lors d’une même fabrication, ou bien de permettre la fabrication de pièces quelque peu différentes également en nombre, chacune pouvant être personnalisée.
“Le premier brevet contemporain de 1984
est français.”
Une plus grande variété d’utilisation et d’association de matériaux
Il y a donc aujourd’hui de très nombreuses possibilités d’aboutir à la fabrication de produits, pièces ou outillages, possédant des formes externes, internes, de géométrie et de topologie complexes, dans des matériaux uniques ou multiples, certaines zones possédant des propriétés et des caractéristiques variables et évoluant de manière plus ou moins brutale d’un matériau vers un autre. Cela est aujourd’hui possible pour les polymères (par la projection de plusieurs matériaux qui peuvent être combinés et déposés avec une grande précision et une très fine résolution) mais aussi pour les métaux (par la projection de poudre ou l’apport de fil dans un flux d’énergie). L’intérêt d’utiliser des pièces multimatériaux n’est pas à démontrer mais la fabrication additive apporte des possibilités incomparables pour des pièces intégrant également de nombreuses fonctions (ailettes, pales, bossages, chapes, collerettes, etc.) apportées sur un substrat pouvant être peu cher et facile à préparer (tube, plaque, etc.).
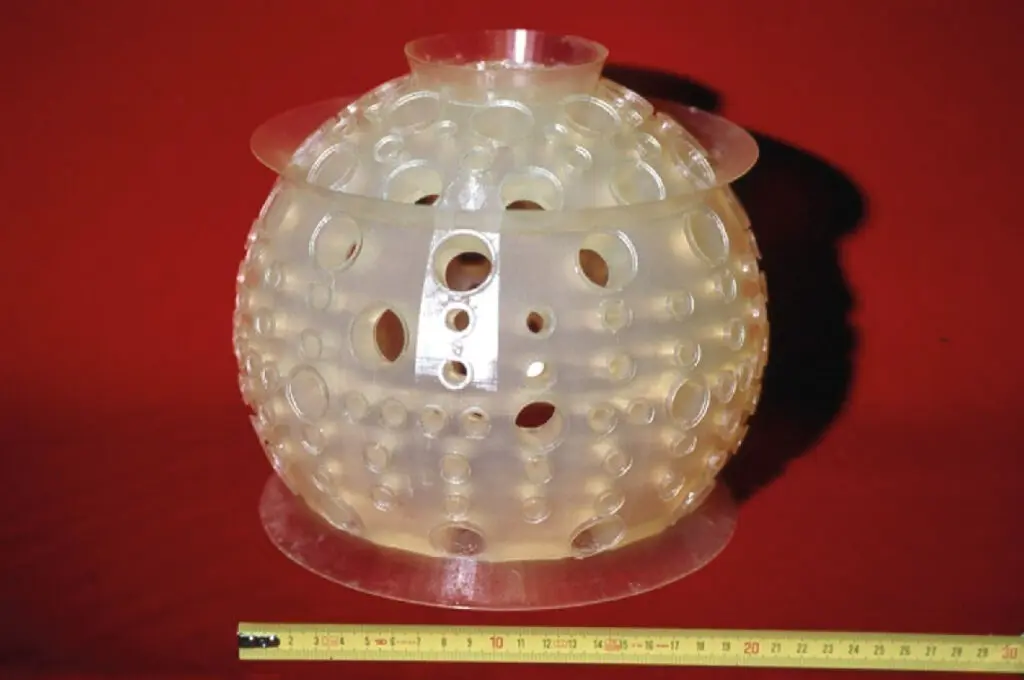
La France comme acteur significatif du progrès international
Si historiquement les États-Unis d’Amérique sont ceux qui ont su développer et commercialiser les premiers procédés à base de matériaux non métalliques (même si le premier brevet contemporain de 1984 est français, déposé par Jean-Claude André, Alain Le Méhauté et Olivier De Witte), l’Europe a pour le moins compensé ce déséquilibre en proposant de nombreuses solutions de fabrication additive de pièces plastiques, céramiques et métalliques. En France, Irepa Laser a créé la start-up BeAM qui appartient aujourd’hui à AddUp, société créée par Michelin et Fives en 2016. Sous ces deux marques, BeAM et AddUp, ces fleurons français du domaine de la fabrication additive de pièces métalliques proposent des solutions à base de projection de poudre dans un flux d’énergie et à base de fusion de lit de poudre. Leur progression sur le marché est intéressante face aux principaux concurrents allemands (EOS, SLM Solutions) ou anglais (Renishaw), et aussi Concept Laser et Arcam (ce dernier étant le seul constructeur européen proposant des machines dont l’apport d’énergie s’effectue par faisceau d’électrons) récemment rachetés par General Electric avec tous leurs écosystèmes (en particulier un fabricant de poudres métalliques (Tekna) et des sociétés de services utilisant des machines de ces constructeurs).
Dans le même temps, ne nous y trompons pas ! D’autres pays plus lointains continuent à développer des machines soit pour leur marché propre (comme la Chine ou le Japon), soit pour viser des partenariats internationaux, comme Hunan Farsoon Co. Ltd, société chinoise qui a signé un accord avec un autre des fleurons français, Prodways. Prodways, du groupe Gorgé, propose lui aussi différents procédés, principalement à base de résines, de résines chargées de céramiques ou d’alumines (voire d’autres matériaux en poudre pour des applications plus spécifiques), avec son procédé Moving Light (flashage mobile de résine par zone, sur le principe du Digital Light Processing, se différenciant du balayage de surface par faisceau laser). Prodways propose un autre procédé de fabrication de pièces métalliques, Rapid Additive Forging, fondé sur le principe du soudage à l’arc avec des matériaux sous forme de fil.
Le panel de technologies et d’acteurs expérimentés par plus de vingt-cinq ans d’expérience apporte une base opérationnelle qui est particulièrement riche en France et qui laisse à penser que le développement industriel de ces technologies est déjà là ou n’est qu’une question de mois ou d’années. Or cela fait effectivement plus qu’un quart de siècle que l’AFPR (Association française de prototypage rapide – fabrication additive) accompagne ces développements et met en relation offreurs de technologies et sociétés potentiels utilisateurs de ces technologies, en sollicitant les meilleures unités de recherche pour doper le développement et la mise en œuvre maîtrisée de ces technologies. Car il est bien question de maîtrise de ces technologies, de la chaîne de valeur complète, au regard des exigences des différents marchés. Cette question reste aujourd’hui d’une importance cruciale et suscite de nombreux développements tant matériels que logiciels.
“La fabrication additive devient plus robuste.”
La formalisation et la capitalisation des connaissances acquises
Tout d’abord, l’expertise est fondamentale à capitaliser et à réutiliser à la fois dans la mise en œuvre des machines et dans la construction de modèles de simulation, voire d’optimisation des produits et des processus technologiques, pour l’aide à la décision de manière générale. Pour cela la connaissance approfondie des phénomènes est indispensable afin de mieux en appréhender le potentiel et les limites, avec en particulier une connaissance complète des défauts potentiels qui peuvent apparaître et une connaissance fine des facteurs influant sur ces défauts. Des technologies principalement de vision et de traitement d’images, d’analyse thermique, ouvrent la voie vers la possibilité de réagir en temps réel sur la correction de défaut en cours de processus ou d’adaptation, voire d’arrêt de production en cas de défaut rédhibitoire. D’autres technologies postfabrication sont en train d’émerger en complément de la traditionnelle inspection par rayonnement X (en particulier dans le cadre du projet national I‑AM-SURE). Grâce à ces technologies, la fabrication additive devient plus robuste, mais tout cela a un coût et prend du temps pour l’acquisition de ces connaissances et leur utilisation opérationnelle de manière industrielle et durable. Car, au-delà de décisions en temps réel, la prédiction des caractéristiques des pièces produites au long de ces chaînes de valeur technologiques est essentielle, afin de minimiser les risques économiques et industriels. Ça passe par la traçabilité des données pertinentes influant sur les caractéristiques finales des produits et leur certification au regard d’un domaine d’utilisation donné. Le Big Data et les Data Analytics aident à exploiter les données et en tirer les facteurs essentiels pour une meilleure compréhension des phénomènes et pour une meilleure création de modèles.
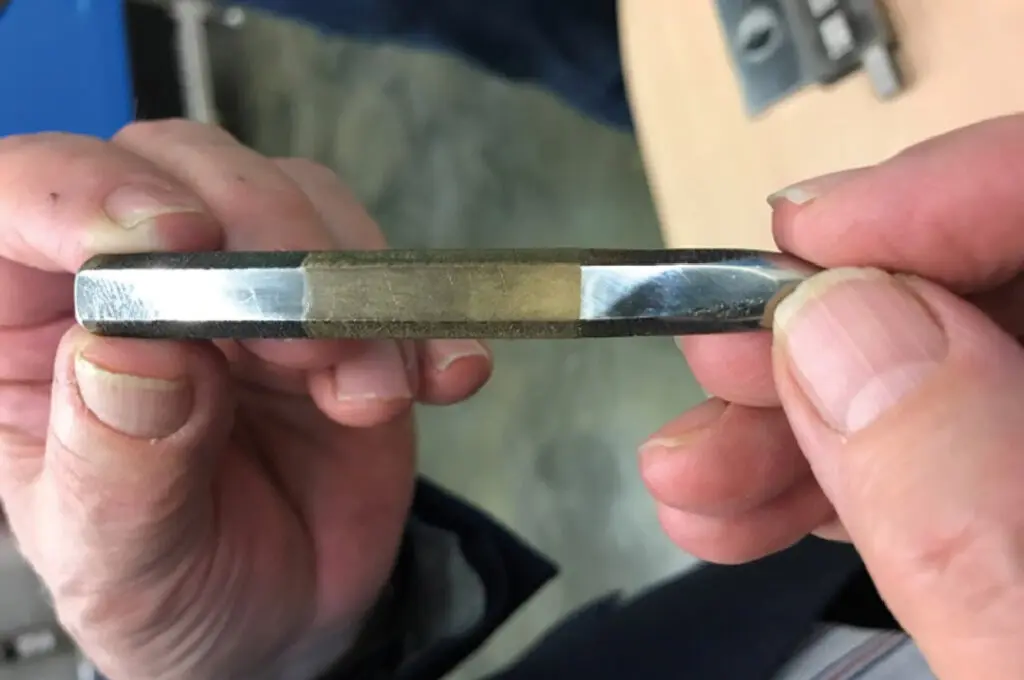
Des attentes pour la conception, la simulation et l’optimisation
Dans le même temps, il est indispensable de donner la possibilité aux ingénieurs de bureau d’études de conduire des analyses poussées des futurs phénomènes liés à la fabrication des pièces. Les modes de conception revisitent les approches d’analyse fonctionnelle très à la mode dans les années 80. Souvent, on cherche à optimiser non plus seulement des pièces mais des produits dans leur ensemble, et la conception se fonde sur l’intégration d’un plus grand nombre de fonctions sur chaque pièce afin de minimiser le nombre des opérations d’assemblage. Des exemples probants ont été proposés dans différents domaines, comme l’injecteur pour moteur d’avion fabriqué par General Electric. En effet, la fabrication additive apporte des solutions d’industrialisation ou de réindustrialisation de produits par l’utilisation de moins de pièces, et pour chaque pièce moins de matière, grâce à des allègements globaux par optimisation topologique, et plus locaux grâce à des structures lattices (en treillis). De grands acteurs de la modélisation développent des solutions commerciales, mais cela prend du temps et, comme les procédés eux-mêmes évoluent, il est compliqué de disposer de modèles conformes à la réalité des possibilités des machines en constante évolution.
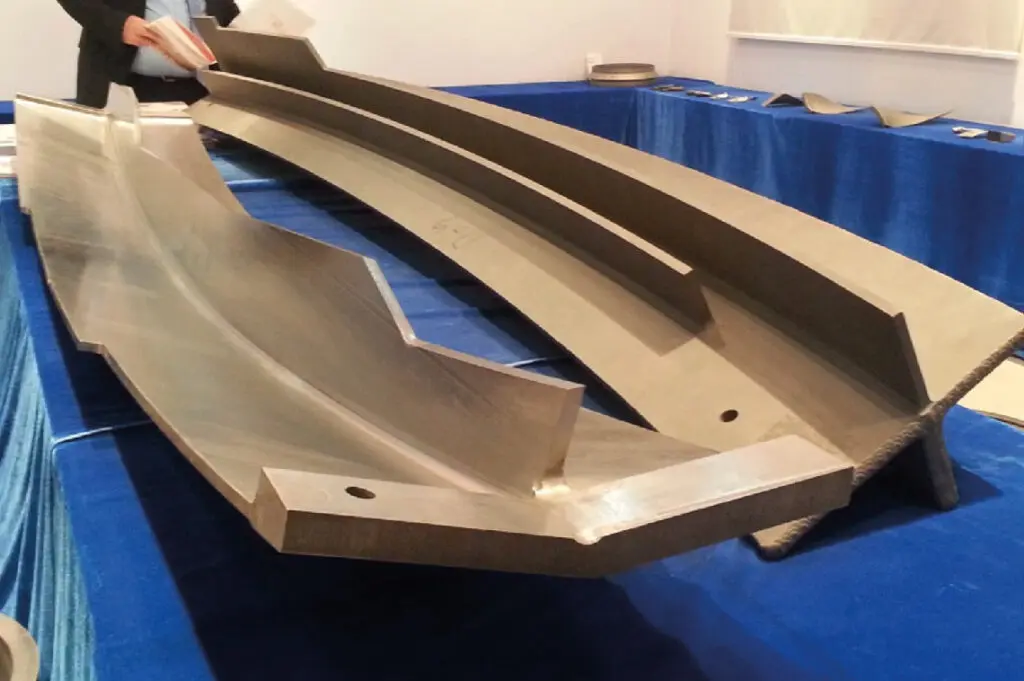
De nouvelles orientations de marché et de choix économiques
Alors que faire, face à ce marché pas encore complètement mature, à ces procédés en constante évolution, à ce manque d’outils intégrés de conception et de préparation, de technologies de contrôle suffisamment bien adaptées ? Bien sûr il faut continuer à avancer, car de très nombreuses solutions de fabrication existent déjà et sont au moins aussi fiables que d’autres procédés plus traditionnels. Ensuite, il ne faut pas demander à la fabrication additive de remplacer tous les procédés, elle en est bien incapable sur les plans technique et économique, et ce n’est pas l’objectif. C’est avant toute chose un « plus technologique » pour de nombreuses applications et il faut la considérer ainsi. Car, grâce à elle, on peut fabriquer des pièces sans avoir besoin d’outillage, mais on peut aussi fabriquer des outillages complexes (comme des moules avec circuits de refroidissement internes optimisés). On peut donc ainsi fabriquer des pièces de topologie complexe, interne comme externe. On peut fabriquer, dans un même batch de production, des pièces différentes sans surcoût de production ; on peut fabriquer à la demande et à l’endroit où l’on a besoin des pièces (sur un bateau, une plate-forme offshore, etc.) pour des actions de maintien en conditions opérationnelles, et dans n’importe quel endroit du Globe, à partir d’un stock de matériau de base et grâce à une « logistique numérique » fiable et sécurisée. Transformer une logistique physique en logistique numérique, c’est l’évolution actuelle qui se fonde sur une rationalisation des quantités fabriquées et sur le fait que, avec moins d’outillages, on peut faire baisser les coûts de fabrication et on peut mieux personnaliser les produits à la demande. Et puis, de manière plus globale, si on s’appuie sur l’ensemble des technologies disponibles, il est aujourd’hui admis que l’on peut exploiter ces technologies de fabrication directe par couche aux différents stades du cycle de vie des produits, depuis la validation des concepts (avec des machines à faible coût d’impression 3D), jusqu’à la réparation et la réutilisation des produits après leur première vie. Il est donc important de suivre l’actualité internationale de la fabrication additive, car de très nombreux centres de compétence apparaissent autour du monde.
“Il ne faut pas demander à la fabrication additive de remplacer tous les procédés.”

Une dynamique mondiale en marche
De nombreux pays proposent des plans nationaux de développement, coordonnés le plus souvent par les experts du domaine et valorisés par les principales filières industrielles, le tout sous la bienveillance et l’aide de fonds nationaux, comme au Royaume-Uni ou à Singapour. D’autres pays, comme la Chine, mettent en place des centres de référence, comme le NIIAM (National Innovation Institute of Additive Manufacturing) à Xi’an ou d’autres initiatives à Pékin, Shanghai ou Wuhan. Que fait la France dans ce domaine ? De nombreuses plates-formes technologiques ont vu le jour. Mais l’absence d’une coordination nationale unique pénalise la rationalisation des moyens au regard des nécessaires progrès indispensables à une stabilisation opérationnelle des pratiques et une diffusion à grande échelle. Cela passe par une sensibilisation dès la formation initiale des étudiants, mais aussi par une formation professionnelle efficace avec une réactivité dans l’adaptation des formations aux besoins, comme le propose le projet Erasmus+ SAM (Skills for Additive Manufacturing). Une indispensable solidarité est à finaliser, à la suite des très nombreux résultats obtenus lors de grands projets nationaux financés en partie par de l’argent public. Des exemples représentatifs ont été présentés lors des dernières Assises européennes de la fabrication additive, organisées par l’AFPR. Sans aucun doute, la création d’un Institut national serait bénéfique et cet institut constituerait une porte d’entrée efficace à l’information et aux formations. En attendant, il est possible de suivre l’actualité quasi en temps réel sur les réseaux sociaux (comme sur LinkedIn) et sur des listes de diffusion (comme info@3dprintingindustry.com) ou la revue A3DM en français, créée il y a quelques années.