Une révolution : le traitement thermique
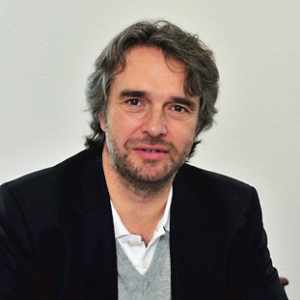
Avec l’avènement de l’ère industrielle, l’essor de la métallurgie a fait naître des ateliers spécialisés dans les recuits, la cémentation et la trempe des aciers au sein des usines de la mécanique. Mais la peur ancestrale du feu et aussi une certaine crainte de ces hommes rejetèrent toujours ces ateliers » dans le fond, à l’autre bout… »
Il y a peu de temps encore, l’atelier de traitements thermiques était souvent celui que l’on ne visitait pas car trop sale, le sol huileux, l’atmosphère enfumée, des flammes partout et le tout dans un local sans fenêtres et pratiquement pas éclairé. Il faut dire que toute source de lumière, solaire ou artificielle, faussait les appréciations de température faites par l’œil exercé des compagnons.
Une technologie en constante évolution
Créée en 1928 à Grenoble, l’entité de construction de fours du groupe Ugine, dont ECM assure la pérennité ainsi que d’autres marques depuis 1985, n’a jamais cessé ses activités et a toujours été le moteur dans l’évolution des technologies. Dans les années soixante, Ugine-Infra construisait des fours sous vide industriels. Cette technologie » propre » a tout d’abord été utilisée par l’industrie aéronautique pour le traitement et le brasage de métaux et alliages haut de gamme comme, entre autres, le titane et les inconels. Les performances de refroidissement de cette génération de fours ne permettaient pas de tremper les aciers, si ce n’est quelques nuances dites » autotrempantes » au Ni-Cr-Mo.
La première grande évolution fut d’introduire dans la technologie des fours sous vide la possibilité de refroidir sous pression de gaz, jusqu’à 5 bars d’azote et, ainsi, de tremper la plupart des aciers fortement alliés pour outillages.
La qualité des traitements obtenus et le confort d’utilisation de ce genre de matériel ont vite été acceptés dans le monde du traitement thermique mais ont aussi suscité beaucoup d’envie, de la part du personnel qui continuait à travailler dans les anciens ateliers, par rapport à cette nouvelle génération de » trempeurs » officiant en blouses blanches… !
La part des traitements sous vide restait confidentielle par rapport à tout ce qui était encore traité de manière conventionnelle en particulier pour l’industrie automobile. Deux verrous restaient à faire sauter : obtenir des vitesses de refroidissement sous gaz surpressé comparables à une trempe à l’huile pour les aciers de construction et, surtout, éliminer les atmosphères carburant libérant de l’oxygène lors du craquage.
ICBP 600 sur site Renault Cléon. © SOCIÉTÉ ECM
Naissance de la cémentation basse pression
Dans les années 1980, ECM a réalisé de nombreuses campagnes d’essais avec des partenaires industriels tels que PSA et Turboméca. Ce développement, couronné de succès, a permis en 1990 de déposer des brevets concernant le procédé de cémentation basse pression » Infracarb® » et les installations modulaires capables de réaliser le traitement.
Le procédé consiste en une succession d’injections sous pression réduite (5 à 15 mbar) d’un gaz carburant dont la molécule est exempte d’oxygène : propane C3H8 ou, dans certains cas, acétylène C2H2. Ces injections, de courtes durées, s’effectuent à un flux maximum correspondant à la limite de solubilité du carbone dans l’acier à une température donnée comprise entre 850 et 1 050 °C.
Il se forme alors en surface un film de cémentite instable qui est diffusée dans la matrice pendant les phases intermédiaires de diffusion sous azote. Les périodes de renouvellement de l’atmosphère dans le laboratoire sont de l’ordre de 5 s, ce qui permet une conduite parfaite des temps d’enrichissement et de diffusion, d’où une maîtrise des profondeurs de cémentation de l’ordre de 5⁄100 mm.
Le procédé » Infracarb® » permet de réduire, dans certains cas, les temps de traitement de moitié par rapport aux procédés de cémentation gazeuse traditionnels.
Parallèlement au développement du procédé, l’entreprise a mis au point et breveté des cellules froides de trempe sous gaz admettant des pressions de 20 bars.
À ce jour, tous les constructeurs d’automobiles du monde, et certains constructeurs de poids lourds, ont investi dans des machines ICBP (Infracarb cémentation basse pression). ECM compte, à l’heure actuelle, 280 unités de cémentation » Infracarb® » en service dans 13 pays différents.
Les qualités de ce genre d’installations : absence de nuisances (bruit, fumée), absence de risques pour les utilisateurs (flammes, atmosphère explosible) ont permis de sortir ces nouveaux fours du fin fond des ateliers de traitements thermiques et la révolution est là : les machines ICBP sont désormais intégrées dans les lignes de fabrication !
ECM 46, rue Jean Vaujany, Techni Sud, 38100 Grenoble. Tél. : 04.76.49.65.60.
Commentaire
Ajouter un commentaire
cémentation basse pression
Le procédé décrit ci-dessus est-il une évolution de celui expérimenté fin 1980 en collaboration avec PSA par STEIN HEURTEY à l’usine de Borny ? (Machine Thor)