Une technologie de rupture pour des lanceurs spatiaux compétitifs

Au-delà des coûts de fabrication, les gains de poids sont absolument déterminants dans la compétitivité des lanceurs spatiaux. La fabrication additive est dans ces conditions un outil prometteur pour cette industrie et elle est déjà largement utilisée. Où en est-on ?
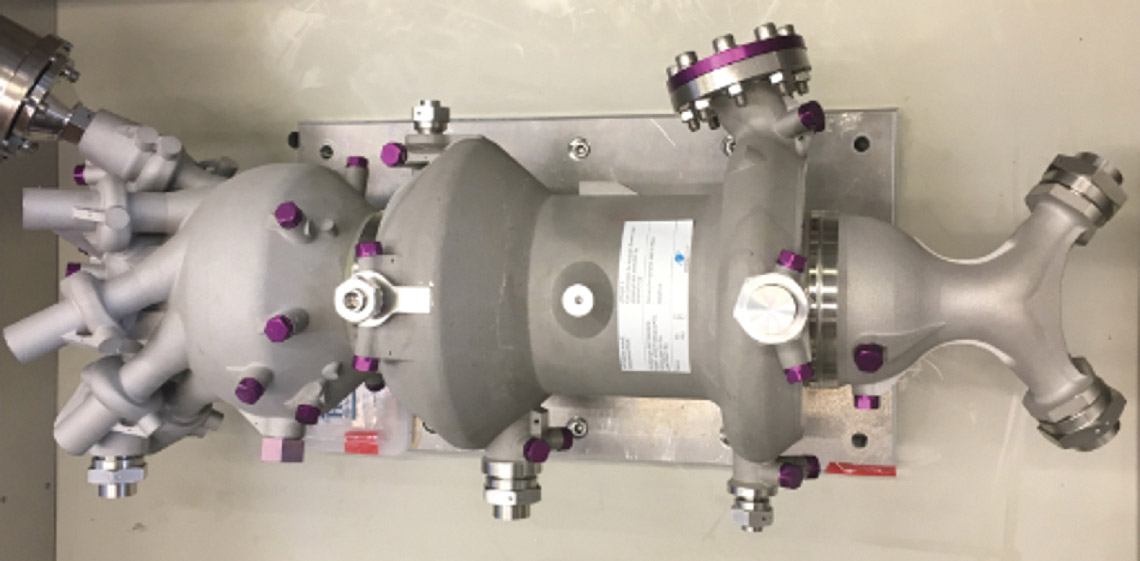
Sur un lanceur, chaque kilogramme de matière qui n’est pas expulsé à très grande vitesse pour contribuer à la fonction propulsive selon le principe de conservation de la quantité de mouvement est un kilogramme qui pénalise la performance finale du lanceur, c’est-à-dire la masse de charge utile (les satellites) qu’il peut injecter en orbite. La chasse à ces kilogrammes de « masse sèche » est fondamentale, surtout lorsque l’on sait qu’en final la masse des satellites représente de l’ordre de 1 % de la masse totale du lanceur au décollage : échouer en matière d’optimisation de la masse sèche est facilement synonyme d’échec total d’un programme, et réussir est synonyme de compétitivité. De tout temps, donc, l’industrie spatiale a cherché les solutions technologiques permettant de réduire à leur minimum les masses sèches des véhicules, aussi bien pour leurs structures que pour leurs moteurs.
Dans ce contexte, l’émergence de la technologie de fabrication additive (l’impression 3D) pour les matériaux métalliques à la fin des années 2000 représente une rupture majeure, la première de cette ampleur dans le domaine de la métallurgie depuis plusieurs décennies, et elle se concrétise d’ores et déjà par de multiples réalisations opérationnelles, en particulier sur le lanceur Ariane 6 qui finit actuellement son développement.
Le secteur spatial, champ d’application idéal pour l’impression 3D
Si le spatial a investi beaucoup et a tiré les applications de l’impression 3D sur les dix dernières années, ce n’est pas uniquement pour ce besoin d’optimisation des masses et volumes des pièces à bord des lanceurs et des satellites, c’est aussi parce que la nature même de l’activité spatiale permet de profiter à plein des bénéfices de cette technologie, tant au stade de la conception des pièces qu’au stade des cycles de fabrication. La plupart des pièces d’un moteur-fusée ou internes à un étage sont plutôt de taille modeste, ce qui colle assez bien avec les volumes utiles des machines de fabrication additive à lit de poudre ; leurs géométries sont souvent complexes et rendent l’application des techniques classiques de forgeage et de fabrication soustractive (fraisage, extrusion, etc.) compliquées et longues de mise en œuvre.
En outre l’impression 3D ouvre des opportunités d’optimisations topologiques infiniment supérieures, ce qui est particulièrement précieux pour les systèmes tels que les échangeurs thermiques où l’on cherche à maximiser l’imbrication de circuits d’échange dans un volume minimal, ou encore pour les divers appendices mécaniques dits « structures secondaires » qui supportent des équipements, de la connectique, etc., où l’on cherche à minimiser la quantité de matière à ce qui est strictement utile pour passer les efforts mécaniques.
Là où un procédé de fabrication classique traite le plus souvent une à une les pièces qu’il produit et est régulièrement limité à une seule typologie de pièces, les machines de fabrication additive sont naturellement des robots aptes à une très grande versatilité dans les fabrications qu’ils réalisent, en séquence ou même en parallèle : c’est ainsi le cas avec les machines à lit de poudre pour lesquelles on cherche à maximiser l’utilisation de la chambre en y plaçant un maximum de pièces différentes à réaliser dans une seule et même séquence. Dans le spatial, les séries sont limitées et les cadences de production sont faibles, de l’ordre du mois, voire de la semaine, ce qui va bien avec cette technologie qui est jusqu’à présent une technologie plutôt lente. Sans que ce soit contradictoire avec le point précédent, pour les produits autrefois fabriqués par assemblage de pièces élémentaires multiples, l’impression 3D donne souvent accès à des cycles très réduits et transforme les mois en jours, grâce à une fabrication directement intégrée, où toutes les pièces élémentaires sont directement fabriquées en même temps que leur support final ; l’exemple le plus spectaculaire pour les moteurs-fusées se trouve au niveau des plaques d’injection où l’assemblage d’environ 200 pièces usinées individuellement autrefois est remplacé par une fabrication en une seule passe. Et enfin, intérêt non des moindres, son empreinte écologique est toujours nettement inférieure, tout d’abord de par la limitation de la quantité de matière approvisionnée à la seule matière nécessaire, mais aussi de par les réductions de consommation électrique, etc.
REPÈRES
Les équipes d’ArianeGroup, le maître d’œuvre des lanceurs Ariane, ont identifié les promesses de la fabrication additive pour les nuances métalliques un peu avant 2010 et les premières activités de R & T ont démarré, pour en tester le potentiel réel et pour assurer la montée en maturité de la maîtrise des procédés et de la qualité des produits.
Cela a conduit à la première application commerciale dès 2012, avec la première pièce lancée dans l’espace, une ferrure de tripode de réflecteur d’antenne pour un gros satellite de télécommunications.
“Les résultats vont bien au-delà
de ce qui avait été escompté.”
La fabrication additive, sur Ariane 5 et Ariane 6
L’année 2014 a été celle du déclenchement du programme Ariane 6 ; dans le monde des lanceurs, le lancement d’un nouveau programme constitue un jalon majeur, qui ne se produit qu’une fois par génération d’ingénieurs, et c’est l’occasion de franchir une marche nouvelle, en renouvelant largement les produits et les outils industriels par rapport à la génération précédente. Dès lors, les progrès constants et les démonstrations de gains réalisés autour des technologies d’impression 3D sur les toutes dernières années amenaient une question évidente autour du recours plus ou moins massif à ces technologies pour la fabrication des milliers de pièces métalliques d’Ariane 6. Par provocation, l’atelier organisé début 2015 avec toutes les équipes concernées au sein de la société, mais également avec le tissu de partenaires académiques, institutionnels et industriels, s’intitula alors : « Voyons donc ce que, sur Ariane 6, nous ne fabriquerons pas en impression 3D… »
Aujourd’hui, cinq ans plus tard seulement, force est de constater que les résultats vont bien au-delà de ce qui avait été escompté alors, tant les progrès de la technologie ont été importants et tant ses promesses économiques se sont confirmées. Ainsi, par exemple, dès 2016 a été mis au point un système inédit sur un lanceur, l’APU (pour Auxiliary Power Unit), pour l’étage supérieur d’Ariane 6 : ce système ultra-compact et léger (plusieurs centaines de kilogrammes gagnées par rapport aux solutions antérieures) assure la pressurisation des réservoirs de l’étage, fonction fondamentale pour leur tenue structurale et pour l’alimentation du moteur ; il offre également un service additionnel de poussée, fort précieux pour les missions très polyvalentes qu’assurera cet étage dans l’espace, notamment pour le déploiement de constellations de satellites. Ce système n’est en fait concevable et fabricable que si l’on recourt à la fabrication additive (en l’occurrence par faisceau laser sur lit de poudre, ou LBM pour Laser Beam Melting) : son design fait appel à des circonvolutions de canaux d’échanges thermiques et à des imbrications complexes de pièces entre elles. Point essentiel à relever également : le passage du concept au premier exemplaire fabriqué s’est déroulé en moins d’une année, cycle très inférieur aux cycles habituels de conception d’organes propulsifs sur les lanceurs… Et aujourd’hui ce système apporte par avance un supplément de valeur pour les futurs clients d’Arianespace et constitue donc un avantage compétitif majeur pour les futures missions d’Ariane 6 dans l’espace.
Les années 2017 et 2018 ont été consacrées à exploiter toutes les vertus de la fabrication additive pour les systèmes propulsifs, non seulement pour Ariane 6 mais aussi déjà pour Ariane 5, qui vole depuis fin 2017 avec une « croix de cardan » de ligne d’échappement désormais produite ainsi. Aujourd’hui, l’additif a littéralement envahi les moteurs cryogéniques, pour les pièces de géométrie complexes certes, mais aussi pour les pièces tournantes les plus critiques. Ainsi, dans ce domaine, la réalisation de la turbine de la turbopompe hydrogène du moteur Vinci (pour l’étage supérieur d’Ariane 6, moteur cryogénique réallumable en vol) constitue une avancée majeure : si l’intérêt de l’impression 3D était évident au vu de la géométrie très travaillée de cette turbine, il fallait tout de même démontrer un niveau de caractéristiques mécaniques extrêmement élevé, pour une pièce tournant à 100 000 tours/min. C’est chose faite, la tenue à 140 000 tours/min a pu être démontrée, ainsi que la parfaite reproductibilité des qualités matériau d’une pièce à l’autre. Les qualités matériau atteintes sont désormais supérieures à ce que nous connaissions antérieurement…
Après les moteurs Vulcain et Vinci, le futur de la motorisation des lanceurs européens est d’ores et déjà en préparation, principalement avec le moteur Prometheus, en cours de conception et prototypage sur le site d’ArianeGroup à Vernon : Prometheus sera le premier moteur cryogénique européen de forte poussée conçu d’emblée avec l’additif, c’est l’une des options majeures qui ouvre aujourd’hui la perspective d’atteindre cet objectif incroyable de réduction de coût d’un facteur 10 par rapport au moteur Vulcain, de poussée équivalente ! En parallèle avec ces progrès majeurs sur les organes propulsifs, la démarche de R & T s’est poursuivie, explorant et développant les différentes techniques de fabrication (fusion sur lit de poudre par laser, par faisceau d’électrons ; technique de dépose de fil…) et pour les différentes nuances métalliques intéressant les produits spatiaux, chacune d’entre elles présentant des intérêts spécifiques, utiles pour des pièces différentes, mais aussi des difficultés de mise au point spécifiques à chaque couple procédé-matériau.
Dans ce contexte, les toutes dernières applications rendues opérationnelles, dès Ariane 5 en l’occurrence, sont des structures secondaires sur l’étage supérieur, où le bénéfice des gains de masse est directement transformé à 100 % en masse supplémentaire offerte aux satellites (contre 30 % pour chaque kilogramme gagné sur l’étage inférieur). Pour tirer le meilleur parti du potentiel de l’impression 3D, ces structures sont conçues à partir d’approches biomimétiques, faisant appel au concept de Generative Design. Ce dernier exemple illustre bien l’une des voies de progression d’ores et déjà engagée et pleine de perspectives pour la fabrication additive, celle d’une ingénierie qui intègre cette technologie pour la conception même des produits, nous y reviendrons d’ailleurs en conclusion.
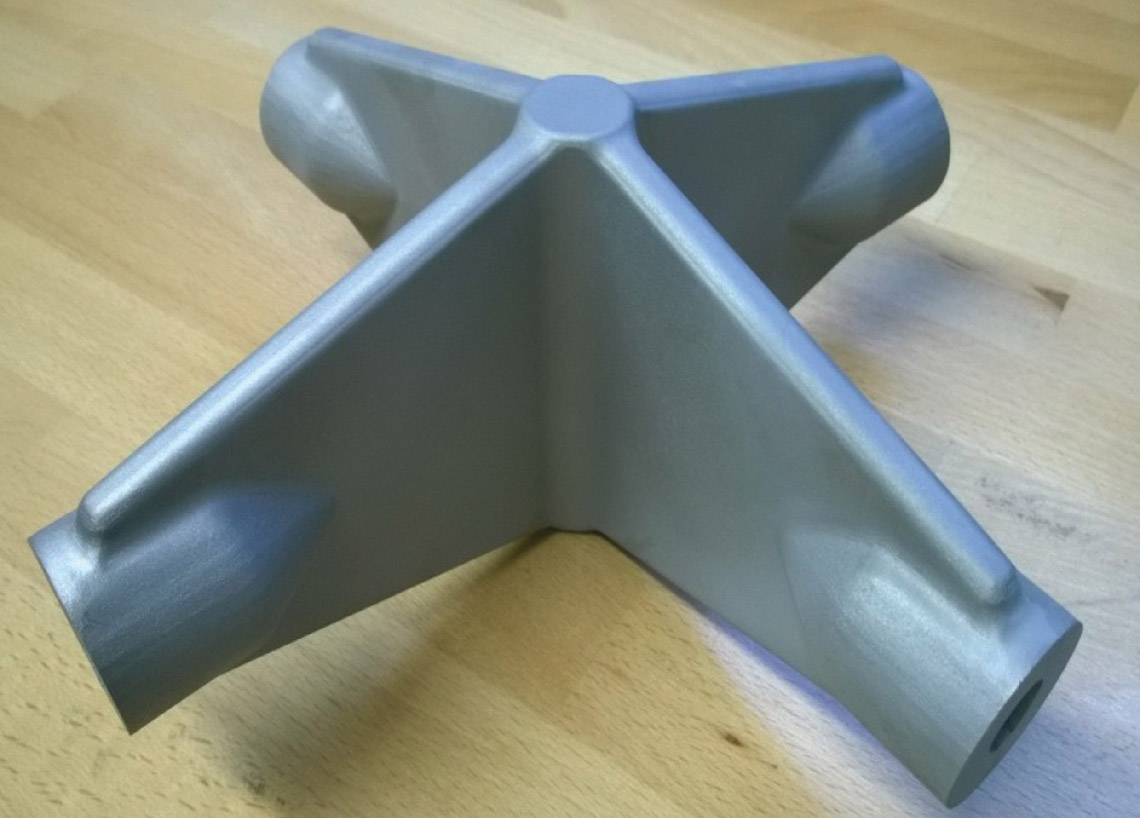
Le mouvement s’accélère dans l’industrie
Les progrès à court-moyen terme seront aussi relatifs aux capacités industrielles elles-mêmes, celles des procédés et des machines d’impression 3D, objet de travaux intensifs de R & D. Dans ce domaine, les besoins du secteur des lanceurs spatiaux sont d’une part une évolution vers l’aptitude à produire des pièces de plus grande taille, typiquement entre 1 et 2 m de dimension unitaire pour les fabrications sur lit de poudre, voire des tailles supérieures pour les ébauches de pièces structurales (technologie fil), nos lanceurs faisant plus de 5 m de diamètre. Concernant les matériaux, au-delà du titane déjà très utilisé pour l’impression 3D dont le prix est malheureusement un frein à la compétitivité, l’aluminium est un produit majeur sur nos lanceurs mais dont la soudabilité, essentielle pour notre sujet, est plutôt médiocre : le développement de procédés de dépose à base d’alliages d’aluminium bien dosés (lithium, scandium, etc.) est aujourd’hui suivi et soutenu de très près. De même pour le cuivre, qui présente les mêmes difficultés tout en étant un matériau essentiel pour certaines parties des moteurs.
Enfin, dernier besoin à relever pour ce qui concerne les progrès attendus directement sur les procédés eux-mêmes : la mise au point de solutions de contrôle non destructif exécuté en temps réel, pendant la fabrication elle-même. En effet, si les coûts de fabrication des pièces sont drastiquement réduits, les temps de fabrication sont longs pour les plus complexes d’entre elles, et s’apercevoir qu’il faut rebuter un produit seulement à l’issue d’une fabrication qui aura pris une ou deux semaines peut coûter plus cher qu’une fabrication classique réussie du premier coup… Le contrôle non destructif en temps réel est donc essentiel, tout comme la possibilité également de déclencher en temps réel la réparation des anomalies détectées, pour minimiser les impacts sur le produit et sur la durée de cycle. Cette thématique nous emmène vers la question de la maîtrise des procédés, de leur validation / qualification, le tout dans la meilleure économie bien entendu.

La maîtrise des procédés
Décrivons le sujet comme nous l’avons vécu ces dernières années : les premières tentatives de recourir à l’impression 3D sont intervenues sur des pièces déjà existantes, fabriquées classiquement jusque-là. Les business cases associés au basculement à l’impression 3D pour fabriquer ces pièces montraient certes un gain intéressant sur le coût de fabrication future, mais au prix d’une dépense initiale qui ne trouvait son amortissement que très tardivement (c’est l’inconvénient, pour le coup, des fabrications à faible cadence…). Si bien que la conclusion était invariablement : « Oubliez, ça ne vaut pas le coup ». Pour ne pas condamner le recours à l’impression 3D uniquement sur les produits nouvellement définis, mais aussi pour réduire les coûts du développement de ces derniers, est donc venue la notion de « qualification de procédé pour une typologie donnée de pièces », par opposition à l’approche qui consiste à réaliser cette qualification produit par produit, avec le procédé et la machine visés. On opère donc désormais la qualification d’une machine avec ses paramètres de réglage pour un métal donné et pour un ensemble de produits similaires, et l’on opère ensuite une « validation » légère, produit par produit, pour chacun des produits dont la fabrication est visée sur cette machine. On mutualise ainsi les coûts non récurrents sur un budget d’investissement central et la facture de la validation individuelle pour chaque produit s’en trouvera allégée, rendant son business case de nouveau attractif. Cette approche structurée est très cohérente de celle adoptée pour les « procédés spéciaux » (cf. normes ISO, AS9100) et d’ores et déjà largement déployée dans l’industrie et l’on va progressivement vers une standardisation des méthodes et critères en la matière.
Plus généralement, notons la mise en ordre progressive d’un nouvel écosystème industriel, où coexistent les fabricants de machines, les fabricants de produits utilisant ces machines et les sociétés offrant du service de fabrication à partir d’un parc de machines, puisque ces robots permettent de fabriquer à distance, sur simple envoi d’un fichier informatique.
“L’approche Generative Design
s’appuie sur des principes de biomimétisme.”
Le Generative Design
Mais revenons dans le domaine de l’ingénierie et de la conception, car c’est là que se dessine certainement la révolution la plus importante à court terme, tant la fabrication additive augmente le champ des possibles dans le dessin des pièces : la soustraction de matière pratiquée jusqu’alors reste toujours possible et l’addition de matière ajoute son potentiel. Pour les structures porteuses de charges mécaniques l’approche Generative Design, déjà mentionnée plus haut, s’appuie sur des principes de biomimétisme et recourt dès lors de plus en plus à l’intelligence artificielle, qui assiste la conception à travers des démarches inspirées de la croissance des organismes vivants en fonction des contraintes qu’ils subissent. Les contraintes en question, simulées dans les calculs, peuvent être de différentes natures : les efforts à passer à travers la pièce, les fréquences propres à respecter, etc., et le design qui en résultera mettra de la matière là et uniquement là où elle est nécessaire, partout ailleurs la pièce sera évidée. Petite subtilité qui ouvre un champ de progrès pour les modélisations mécaniques : à partir du moment où l’on optimise ainsi les structures, on les met aux limites de performance vis-à-vis des modes de rupture associés et l’on fait donc apparaître le risque de déclencher d’autres modes de défaillance. Ainsi donc, pour une structure ultra-optimisée apparaît très vite la problématique de sa tenue en flambage qui nécessite à la fois d’abord une modélisation en propre (jamais simple) et une maîtrise de la qualité de production ensuite, pour éviter les défauts limites qui généreront l’instabilité redoutée. Il en ira de même avec la tenue à la fatigue, la propagation de défauts, etc.
On notera finalement que cette notion de « structure porteuse de charges mécaniques » est en fait très vaste et même universelle : toutes les pièces sont finalement porteuses de charges mécaniques et peuvent donc bénéficier de cette approche, certaines d’entre elles doivent certes répondre en plus à des exigences de conduite de fluide et donc des exigences d’étanchéité qui empêchent de les évider, mais cela n’empêche pas de les optimiser du point de vue mécanique, en jouant localement sur des raidissages bien placés, permettant de minimiser les épaisseurs des canaux là où c’est possible, ce qui réduit d’autant la masse de la pièce. Dans tous les cas, cette approche Generative Design est gagnante sur tous les plans, celui des coûts de fabrication avec des réductions allant jusqu’à 60 %, celui de la masse (gains régulièrement supérieurs à 50 %), mais aussi sur celui des durées et coûts de conception et développement eux-mêmes (typiquement 80 % !).
Reconfigurer toute la chaîne industrielle
Ainsi donc, nos bureaux d’études doivent-ils aujourd’hui se reconfigurer, développer de nouvelles méthodologies de conception, et même… se laisser guider par les jeunes ingénieurs que nos écoles ont déjà bien familiarisés avec les techniques de l’intelligence artificielle pour l’optimisation par autoapprentissage. Au-delà de cette rupture au sein des bureaux d’études, c’est toute la chaîne industrielle, son organisation et ses schémas traditionnels qui sont bouleversés. En effet, sur les dernières décennies, nos industries ont pris le soin de structurer la démarche de conception-production en étapes marquées, celle de la détermination des charges et environnements par le bureau d’analyse système, celle de la conception par le bureau d’études qui réceptionne les spécifications du précédent et définit la pièce qui répond au besoin, puis celle du bureau des méthodes qui réceptionne la définition précédente et définit la manière (les gammes, l’outillage) à adopter pour la fabriquer, puis les équipes de production qui ensuite mettent ça en œuvre. Aujourd’hui, l’impression 3D traverse ces schémas et connecte directement le spécificateur amont et la réalisation du produit, court-circuitant largement les étapes intermédiaires.
C’est ainsi que l’impression 3D est identifiée souvent avant tout comme une technique de prototypage, permettant la conception-validation rapide de pièces prototypes. Aujourd’hui, la fiabilité des procédés de fabrication est acquise pour nombre de nuances métalliques, on passe donc très directement à l’industrialisation dès l’issue de la conception. Et, si l’on va encore un peu plus loin dans cette direction du prototypage opérationnel, on voit que l’on peut même réadapter complètement et très utilement les logiques mêmes de nos programmes. Le changement de paradigme consiste alors à sortir du schéma actuel qui vise à modéliser, modéliser de plus en plus finement le produit le long du cycle de conception, puis le fabriquer tardivement et le tester pour démontrer que la conception par modèle a été correcte. Les essais en question sont donc tardifs et n’ont qu’une seule issue possible : ils doivent être concluants, sinon c’est tout le planning du programme qui est en jeu. Dès lors, la conception amont est volontairement conservative et dote le produit de marges forcément exagérées, qui pénalisent la performance finale. Par opposition, le prototypage rapide par impression 3D et le faible coût des pièces permettent de fabriquer très tôt dans le cycle, de fabriquer pour tester tôt, de tester tôt pour corriger le cas échéant le design, le refabriquer ensuite et converger ainsi rapidement vers un produit dont les performances sont démontrées bien plus tôt dans le cycle de développement. La pièce est alors aussi mieux optimisée, les conservatismes de l’approche précédente sont facilement éliminés.
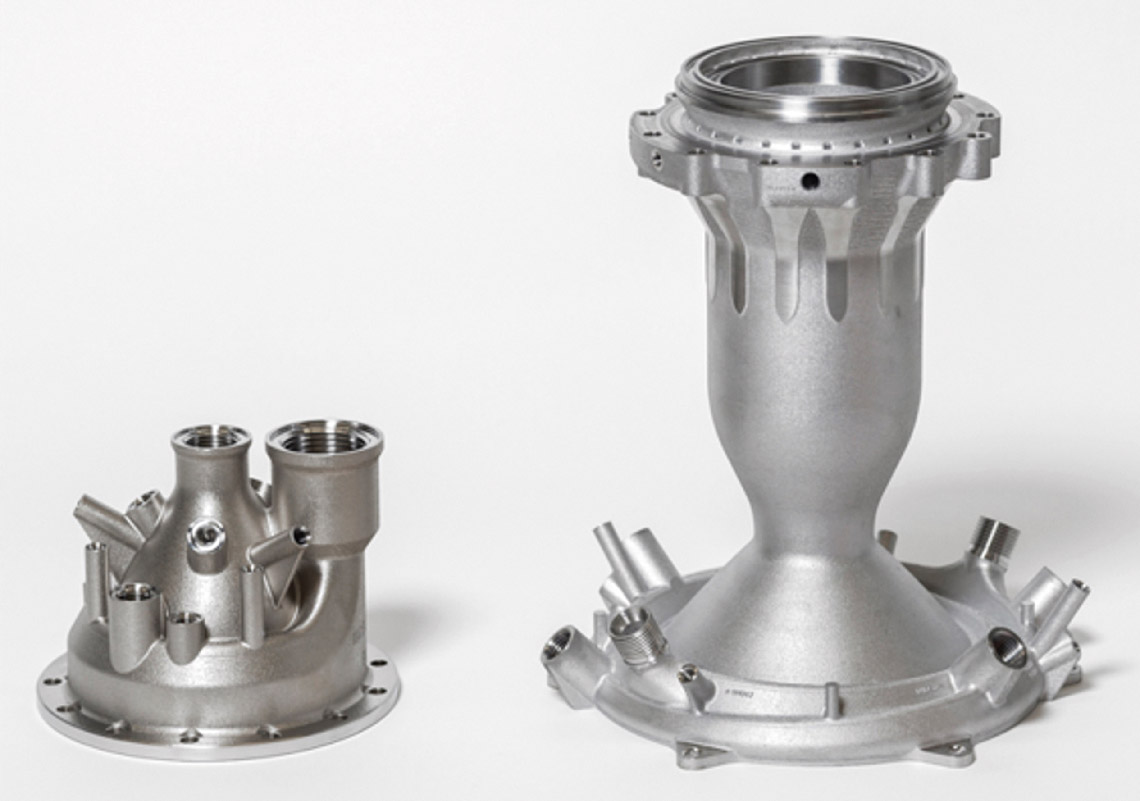
Hardware et software
Ce faisant, la fabrication additive rapproche d’une certaine manière l’ingénierie du hardware de celle du software : la conception s’appuie sur une logique « conçoit, teste et corrige » dans des temps raccourcis, à l’image des méthodes de développement logiciel, et l’on ouvre directement la voie vers l’application des méthodes de développement agile, pour produire des pièces comme des applications. On a donc là une belle convergence entre l’industrie du hardware et celle du logiciel : l’impression 3D est au cœur de la digitalisation de nos usines, pas seulement des usines en tant que telles, mais des usines en relation avec les bureaux d’études. Ce mouvement préfigure aussi certainement l’industrie post 4.0, y compris pour les pièces qui ne se fabriquent pas en procédé additif : elles seront produites aussi de manière largement robotisée, avec des robots aptes à produire tous types de pièces en parallèle dans un atelier donné, comme on remplit aujourd’hui une machine d’impression 3D sur lit de poudre en lui faisant fabriquer de multiples pièces ensemble. Du point de vue de l’efficacité industrielle, on atteindra alors l’objectif tant recherché, celui de charger en continu chaque atelier de nos usines et de s’adapter immédiatement à toute évolution de définition des produits à fabriquer…